Introduction to Hydraulic Sealing Failures
The importance of secure hydraulic sealing
In high-pressure hydraulic systems, achieving a perfect seal is not just a best practice—it’s a necessity. A secure hydraulic seal ensures that pressurized fluids are contained within the system, maintaining operational efficiency, protecting components, and preventing hazardous leaks. However, even minor imperfections in hydraulic fittings can lead to significant sealing issues, especially when tolerances fall outside of acceptable limits.
Common consequences of sealing failures
When a hydraulic system experiences sealing failure, the effects can be immediate and severe. These include:
- Loss of system pressure and performance
- Increased wear on components due to fluid leakage
- Environmental contamination and safety risks
- Unexpected downtime and costly repairs
By understanding the critical role that hydraulic fitting size tolerance plays in sealing reliability, technicians and engineers can better prevent these outcomes.
Understanding Hydraulic Fittings
What are hydraulic fittings?
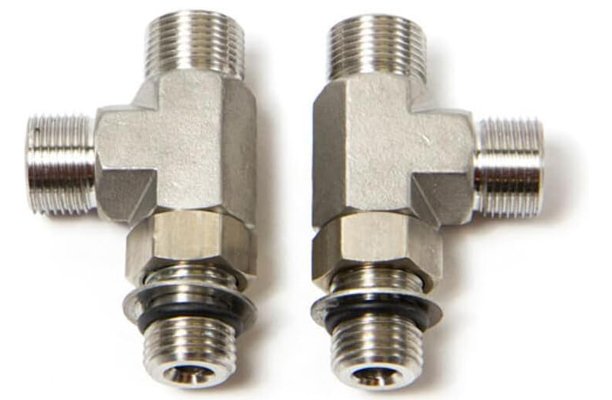
Hydraulic fittings are components used to connect hoses, pipes, and tubes within a hydraulic system. They allow for the safe transfer of fluid between different sections of the system while withstanding high pressure and temperature variations. Their functionality is highly dependent on accurate dimensions and material compatibility.
Types of hydraulic fittings
There are various types of hydraulic fittings, each designed for specific applications:
- Compression fittings: Used for secure and leak-free connections without welding.
- Flare fittings: Known for their reliability in high-pressure applications.
- O-ring face seal fittings: Provide a strong seal through a captured O-ring design.
- Threaded fittings: Common in many systems, relying on thread engagement for sealing.
Each type has its own tolerance range, and deviations can significantly affect sealing performance.
The Role of Size Tolerance in Hydraulic Systems
Definition of size tolerance
Size tolerance refers to the permissible variation in the physical dimensions of a component from its specified measurement. In hydraulic systems, this means how closely a fitting’s actual size matches the design specifications. Tighter tolerances equate to more precise fits, which are essential for maintaining leak-proof connections under pressure.
Precision engineering in hydraulic systems
Hydraulic systems demand precision engineering due to the extreme conditions they operate under. Tolerance errors as small as a few microns can disrupt the seal, leading to fluid loss and system failure. This makes hydraulic fitting size tolerance one of the most overlooked yet essential factors in system design and maintenance.
Why Hydraulic Fitting Size Tolerance Is Critical
Impact on pressure retention
The integrity of a hydraulic seal depends on the precise contact between mating surfaces. When the fitting size deviates beyond acceptable tolerance ranges, it creates microscopic gaps that allow pressurized fluid to escape. This not only reduces overall system efficiency but also poses safety risks, especially in high-load applications such as construction equipment, aircraft hydraulics, and industrial automation systems.
Effects on O-ring and seal performance
Seals and O-rings are engineered to operate within specific dimensional parameters. When a fitting is undersized or oversized, it can:
- Over-compress the O-ring, causing premature wear or extrusion
- Leave a loose fit, failing to achieve a complete seal
- Create uneven surface pressure, leading to seal distortion and leaks
These conditions significantly reduce the lifespan of sealing components and increase maintenance frequency. Therefore, maintaining optimal hydraulic fitting size tolerance is essential for reliable sealing.
Common Causes of Tolerance-Related Failures
Manufacturing defects
Even the best design is vulnerable to poor manufacturing practices. Minor machining errors or inconsistencies in production runs can introduce dimensional deviations. These flaws may not be visible to the naked eye but can severely compromise the fitting’s sealing ability, especially under high pressure and thermal cycling.
Poor quality control
Without rigorous quality assurance protocols, defective or out-of-spec fittings can easily enter circulation. Inadequate inspection tools, inconsistent measurement techniques, or skipped testing steps are all potential contributors to tolerance-related sealing failures. Establishing standardized inspection criteria is essential for maintaining consistent quality across batches.
Incorrect fitting selection
Sometimes the issue is not with the fitting itself but with how it’s chosen. Mismatching fittings from different standards (e.g., mixing metric and imperial), selecting the wrong pressure rating, or ignoring the system’s environmental conditions can result in fittings that don’t fit correctly, leading to sealing failure. Always verify compatibility and tolerance specs before installation.
Signs of a Tolerance-Induced Sealing Failure
Leaks and pressure drops
The most immediate indicator of a sealing failure is a visible fluid leak or a sudden drop in system pressure. These symptoms often point directly to poor contact between components, a hallmark of tolerance issues. In systems where pressure is closely monitored, fluctuations can also suggest internal leakage caused by misfit fittings.
Vibration and noise
Improperly sized fittings can lead to unstable hydraulic connections, which manifest as abnormal vibrations or acoustic emissions such as hissing or knocking. These noises are early warning signs that the connection is not secure—possibly due to a dimensional mismatch—and should be inspected immediately to prevent further damage.
How to Ensure Proper Hydraulic Fitting Tolerance
Using certified and standardized fittings
The first step in ensuring proper size tolerance is sourcing fittings from certified, reputable manufacturers who adhere to international standards such as ISO 8434, SAE J514, or DIN 2353. These standards establish acceptable tolerance ranges and testing protocols that ensure dimensional accuracy and performance reliability.
Beware of off-brand components that may lack rigorous quality control. A low-cost fitting might save a few dollars upfront but could cost significantly more if it results in system failure or downtime.
Importance of component inspection
Before installation, fittings should be inspected using precision measuring tools such as calipers, micrometers, and optical comparators. Check for:
- Correct thread pitch and depth
- Surface finish and roundness
- O-ring groove dimensions
Documenting these inspections not only helps prevent future failures but also establishes traceability in case of warranty claims or audits.
The Role of Quality Control in Sealing Success
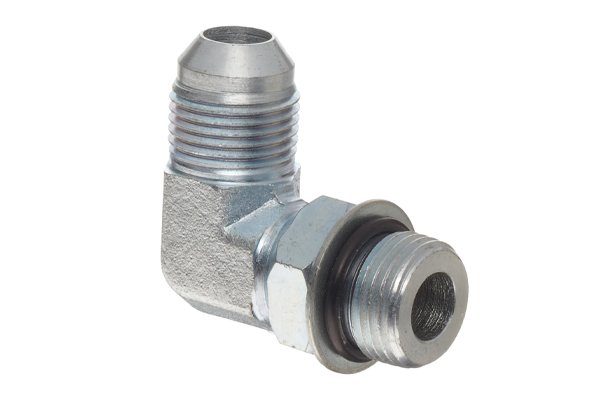
Inspection tools and techniques
Modern quality control in hydraulic component manufacturing employs a combination of traditional tools and advanced technologies. These include:
- Coordinate Measuring Machines (CMM): For 3D dimensional verification
- Optical measurement systems: Ideal for detecting micro-defects in seal surfaces
- Laser scanning: Offers high-speed, non-contact profiling of complex geometries
Using such tools ensures that every fitting meets strict tolerance requirements before being approved for use.
Testing and validation procedures
Post-manufacturing tests such as hydrostatic pressure testing, helium leak detection, and thermal cycling simulations provide assurance that the fittings perform reliably under real-world conditions. These procedures validate not only the dimensional tolerance but also the functional integrity of the seal when installed.
Tips for Selecting the Right Fittings
Matching application requirements
Choosing the right hydraulic fitting involves more than matching thread types and sizes. The operating environment, fluid type, pressure level, and temperature range all influence the appropriate selection. For example, fittings designed for high-temperature environments must accommodate thermal expansion, which directly impacts hydraulic fitting size tolerance over time.
Failing to match the fitting to the application can result in premature seal degradation, corrosion, or mechanical failure. Always consult with hydraulic specialists or engineers when designing or modifying a hydraulic circuit to ensure the components meet the required specifications.
Consulting manufacturers’ specifications
All reputable fitting manufacturers provide detailed technical documentation, including dimensional drawings, tolerance ranges, pressure ratings, and material specifications. Use these resources to verify that the chosen fitting aligns with the system’s performance demands.
Additionally, cross-referencing specifications ensures compatibility with existing components and helps avoid costly mistakes associated with mismatched tolerances.
Preventive Maintenance and Monitoring
Regular inspection schedules
Even the highest-quality fittings are subject to wear and fatigue. Implementing a routine maintenance schedule helps detect early signs of failure before they escalate into serious issues. Key inspection points include:
- Checking for micro-leaks around fittings
- Examining O-rings and seals for wear or extrusion
- Rechecking torque and alignment of fittings
These checks should be logged and tracked over time to identify patterns and predict failures more accurately.
Diagnostic tools for early detection
Modern hydraulic systems can be equipped with sensors that detect changes in pressure, temperature, and vibration. Abnormal readings may indicate issues with seal integrity or fitting stability. Thermal imaging cameras can also be used to identify hot spots where fluid leakage might be occurring due to a tolerance mismatch.
Proactive monitoring ensures the longevity of the system and provides data to support predictive maintenance strategies.
Role of Material Compatibility
How different materials affect tolerance
Different metals and alloys expand and contract at different rates based on temperature, pressure, and chemical exposure. This directly impacts the effectiveness of a hydraulic seal. For example, fittings made from stainless steel and those from brass will respond differently to thermal cycling, potentially altering the mating dimensions and causing sealing gaps.
Additionally, softer materials may deform under torque, skewing the intended dimensions and making the tolerance specifications meaningless. Understanding these behaviors is essential to selecting fittings that maintain their tolerance over the service life of the system.
Importance of material testing
Before integrating new materials into a hydraulic system, it’s critical to test for:
- Corrosion resistance with specific fluids
- Mechanical stability under load
- Thermal expansion rates
Material testing helps ensure that both the physical dimensions and long-term performance characteristics align with system demands, preserving optimal hydraulic fitting size tolerance even under stress.
Innovations in Hydraulic Fitting Design
Smart fittings and sensors
The hydraulic industry is embracing innovation to solve traditional challenges such as sealing failures caused by tolerance discrepancies. One of the most promising developments is the integration of smart fittings—components equipped with sensors that monitor pressure, temperature, and vibration in real time. These sensors can alert operators when fittings are under stress or when a tolerance issue may be causing a micro-leak, preventing failure before it happens.
Tolerance compensation technologies
Advanced manufacturing techniques, such as precision CNC machining and additive manufacturing (3D printing), now allow for tighter and more consistent tolerance control. Some fittings are being designed with built-in features like elastomeric inserts or self-adjusting seals that can compensate for minor dimensional variations, increasing sealing reliability even under less-than-ideal conditions.
These innovations reflect a growing recognition across the industry that hydraulic fitting size tolerance is a critical factor in system design and long-term operational success.
Conclusion
Hydraulic sealing failures are often symptoms of deeper issues—most notably, poor adherence to size tolerance standards. From manufacturing defects and improper fitting selection to material incompatibilities and lack of quality control, the causes are varied but often preventable.
Understanding and managing hydraulic fitting size tolerance is not merely a technical detail—it’s a foundational aspect of system integrity, safety, and efficiency. By investing in high-quality fittings, enforcing precise inspection routines, and staying up-to-date with emerging technologies, engineers and technicians can drastically reduce the risk of failure, minimize downtime, and optimize performance in hydraulic applications.
FAQs
What is the ideal size tolerance for hydraulic fittings?
The ideal size tolerance varies depending on the fitting type and application, but it generally falls within ±0.01 mm to ±0.05 mm. Always refer to the manufacturer’s or applicable standard’s specification for precise values.
Can size tolerance be corrected after installation?
No, once a fitting is installed, dimensional errors cannot be corrected. Attempting to force a fit or use sealants may lead to further failure. Instead, the out-of-spec component should be replaced with one that meets the correct tolerance.
How do I know if a fitting is out of tolerance?
Use precise measuring instruments such as micrometers or coordinate measuring machines (CMM) to verify the dimensions against the manufacturer’s specifications. Leaks, vibrations, or installation difficulties are also indirect signs.
Are all hydraulic fittings manufactured to the same standards?
No. Different regions and applications may use varying standards such as ISO, SAE, DIN, and JIS. It’s essential to match fittings within the same standard to ensure tolerance compatibility and sealing reliability.
What tools can measure fitting tolerance accurately?
Common tools include digital calipers, micrometers, go/no-go gauges, thread pitch gauges, and CMMs. Optical comparators and laser scanners are also used for high-precision inspection in manufacturing environments.