Introduction
Noise in hydraulic systems is more than just an annoyance—it’s often a warning sign of underlying mechanical issues. Whether it’s a screech, hiss, or thump, excessive noise can indicate air contamination, cavitation, or loose fittings, all of which affect performance and lifespan. Reducing hydraulic noise not only protects machinery but also safeguards operators from hearing damage and fatigue, all while helping you meet industrial noise regulations. This article dives into the causes, effects, and solutions for hydraulic fitting system noise, equipping engineers, maintenance teams, and equipment owners with actionable insights.
Understanding Hydraulic Systems and Their Components
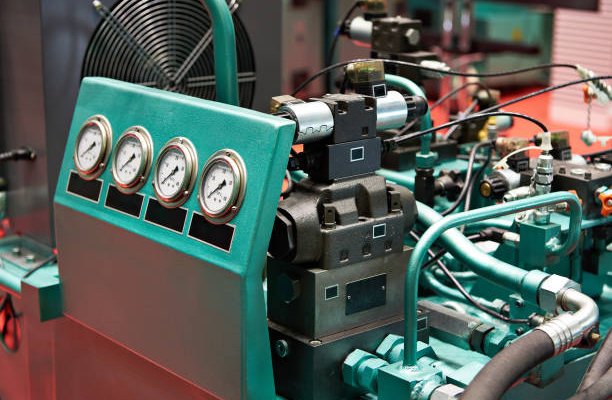
Hydraulic systems use pressurized fluid to transmit energy across various components, enabling tasks like lifting, pressing, and steering. At the core of these systems are hydraulic fittings—connectors that guide fluid flow between components such as pumps, valves, actuators, and hoses. These fittings are crucial for maintaining pressure integrity and minimizing leaks, but when improperly selected or installed, they can become major noise sources. Understanding each part’s function—pump, reservoir, valves, cylinders, filters, and fittings—provides the foundation for diagnosing and preventing noise issues in a hydraulic circuit.
Major Causes of Noise in Hydraulic Fitting Systems
Aeration: Air Contamination in Hydraulic Fluid
Aeration occurs when air becomes trapped in the hydraulic fluid. This air enters through loose fittings, worn seals, or poor maintenance practices. As air bubbles collapse under pressure, they generate a high-pitched noise and degrade hydraulic fluid, causing wear on internal components. Aeration is not only noisy—it also reduces system efficiency and can lead to failure if not addressed.
Cavitation: Vapor Bubbles Under Pressure
Unlike aeration, cavitation involves vapor bubbles forming due to rapid pressure drops in the system. When these bubbles implode, they produce sharp knocking sounds and cause pitting damage to pumps and valves. Cavitation is often linked to restricted fluid flow, improper reservoir levels, or incorrect line sizing. It’s a major contributor to both hydraulic noise and long-term equipment damage.
Mechanical Issues: Vibration and Wear
Loose or misaligned hydraulic fittings can vibrate during operation, creating rattling or buzzing noises. Over time, these vibrations lead to wear and even catastrophic fitting failures. Excessive mechanical friction between moving parts, or poorly mounted hoses and lines, also increases acoustic output. Identifying and securing these components is essential to keeping noise levels low.
Implications of Hydraulic System Noise
Excessive noise in a hydraulic system is more than a comfort issue—it has operational, safety, and compliance consequences. Prolonged exposure to loud machinery can cause hearing loss and fatigue among operators, reducing overall workplace productivity. Additionally, noisy systems often signal inefficiencies such as air leaks, pressure fluctuations, or internal wear, which accelerate component degradation and lead to costly downtime. From a regulatory perspective, industries are increasingly required to comply with noise level standards set by organizations like OSHA, ISO, and EU Machinery Directives. Addressing hydraulic noise early helps meet these standards and prolongs the system’s lifespan.
Strategies for Reducing Hydraulic System Noise
Diagnosing Noise Sources
The first step in reducing noise is identifying its root cause. Conduct a visual inspection for loose or damaged fittings, fluid leaks, or improper hose routing. Use diagnostic tools like ultrasonic leak detectors, stethoscopes, and vibration sensors to pinpoint the origin of the sound. Frequency analysis can help distinguish between aeration, cavitation, and mechanical issues, enabling targeted interventions.
Upgrading to Noise-Resistant Fittings
Replacing low-grade or worn-out fittings with high-quality, vibration-resistant alternatives can significantly reduce noise. Look for fittings with precision machining, reinforced materials, and anti-vibration features. It’s essential to match the fitting’s pressure rating and material with system requirements to prevent future noise issues and ensure safe operation.
System Design Improvements
Good design minimizes the conditions that cause noise. Shorten fluid paths where possible, avoid sharp bends in tubing, and ensure proper mounting of hoses and lines. Adding acoustic insulation, shock absorbers, and vibration dampers to fittings and nearby components helps absorb sound energy. Additionally, maintaining a proper fluid temperature and avoiding over-pressurization contributes to a quieter system.
Choosing the Right Hydraulic Fittings for Noise Control
The materials and design of hydraulic fittings play a crucial role in noise management. Steel fittings offer high strength and are commonly used in high-pressure systems but may transfer more vibration. Brass and stainless steel provide corrosion resistance and are often quieter in operation. When selecting fittings, consider compatibility with the hydraulic fluid, pressure range, environmental conditions, and vibration levels. Using compression or flare-type fittings can also help create a tighter, more secure seal that reduces the chances of air ingress and fluid turbulence—key contributors to noise.
The Role of Hydraulic Hose Assemblies
Hydraulic hoses act as the arteries of the system, transferring pressurized fluid between components. Their layout and support significantly affect system noise. Poorly routed or unsupported hoses can flex and vibrate under pressure surges, amplifying sound and contributing to wear. To reduce noise, hoses should be routed in smooth curves—avoiding kinks or tight bends—and secured with clamps or brackets that dampen vibration. Additionally, using hoses with reinforced layers or internal dampening materials can help suppress high-frequency noise, especially in high-speed or high-pressure applications.
Training and Best Practices for Technicians
Even the most advanced hydraulic components can fail to perform if not installed or maintained correctly. Technicians should be trained in proper fitting selection, torque specifications, hose routing techniques, and diagnostic practices. Educating personnel on recognizing early signs of aeration, cavitation, and mechanical wear can prevent noise issues before they escalate. Furthermore, technicians should follow manufacturer-recommended procedures for tightening fittings and conducting post-installation leak tests, ensuring that no air enters the system and fluid flows remain smooth and quiet.
Case Study: Real-World Hydraulic Noise Problem and Fix
Background: A manufacturing facility experienced excessive noise from a hydraulic press used in metal forming. The high-pitched whining and irregular thumping sounds not only disrupted workflow but also raised safety concerns among operators.
Diagnosis: Upon inspection, the maintenance team discovered multiple loose fittings and evidence of cavitation within the pump. Vibration analysis and ultrasonic sensors confirmed high levels of acoustic energy near the hose junctions and return lines.
Solution: The team replaced all suspect fittings with high-quality, vibration-resistant models and rerouted hoses to reduce sharp bends. They also flushed the system to remove air and adjusted fluid levels to meet OEM specifications. After these changes, noise levels dropped by over 50%, restoring operator comfort and system performance while extending the equipment’s operational life.
Emerging Technologies and Trends in Noise Reduction
As hydraulic systems evolve, so do the technologies aimed at making them quieter and more efficient. One of the most promising trends is the use of smart sensors for real-time vibration and noise monitoring. These devices detect early signs of air intrusion, cavitation, or component failure, enabling predictive maintenance before issues worsen. Additionally, manufacturers are developing advanced fitting materials and geometries designed to reduce turbulence and minimize sound propagation. Acoustic enclosures, noise-absorbing coatings, and digital noise filters are also being integrated into modern systems, especially in industries like aerospace and medical manufacturing where silence is critical.
Conclusion and Key Takeaways
Hydraulic fitting system noise is not just a nuisance—it’s a signal. By understanding the causes of noise such as aeration, cavitation, and mechanical vibration, businesses can diagnose and fix issues before they lead to major failures. Choosing the right fittings, following sound installation practices, and adopting proactive maintenance can greatly reduce noise levels. Training technicians and leveraging new technologies further enhances noise control and system reliability. Ultimately, a quieter hydraulic system means improved safety, regulatory compliance, equipment longevity, and a better working environment for operators.
Frequently Asked Questions (FAQs)
1. What is the most common cause of noise in hydraulic fittings?
The most common cause is air trapped in the hydraulic fluid (aeration), often due to loose or improperly sealed fittings.
2. How can I tell if cavitation is happening in my hydraulic system?
Cavitation often produces a knocking or rattling noise and is usually accompanied by reduced system performance or visible damage to pumps and valves.
3. Do certain materials for fittings reduce noise better than others?
Yes. Brass and stainless steel fittings tend to transmit less vibration than steel, making them better options for noise-sensitive environments.
4. How often should hydraulic systems be checked for noise issues?
Regular inspections should be done monthly, with more frequent checks during peak operation periods or after system changes.
5. Can smart sensors really help reduce hydraulic system noise?
Absolutely. Smart sensors detect subtle changes in vibration and noise, allowing for early diagnosis and intervention, which reduces both noise and maintenance costs.