Introduction
Hydraulic fittings usages are critical to the performance of today’s heavy-duty machinery and automated systems. These essential components lie at the heart of hydraulic systems, enabling the seamless transmission of pressurized fluids within closed-loop circuits. From construction sites to aerospace hangars, hydraulic fittings ensure system integrity, operational efficiency, and safety across a wide range of demanding industries.
This article explores the various applications of hydraulic fittings across major industries, highlights their critical roles, and outlines the best practices for maintenance and selection to maximize performance and longevity.
What Are Hydraulic Fittings?
Hydraulic fittings are mechanical components that join hoses, tubes, and pipes in hydraulic systems to facilitate fluid transfer. Designed to withstand high-pressure environments, these fittings are crucial for directing hydraulic fluid flow, ensuring leak-proof seals, and enabling the modular assembly of hydraulic networks.
Depending on their use case, hydraulic fittings may be designed for permanent connections or for easy disassembly. Key considerations in their design include pressure rating, material compatibility, corrosion resistance, and connection type. They are available in a variety of configurations, including elbows, tees, crosses, and adapters to accommodate complex routing requirements in equipment.
Types of Hydraulic Fittings
Compression Fittings
Compression fittings use a compression nut and ferrule to create a tight seal; moreover, they do so without requiring any welding or soldering. As a result, they are widely used in low to medium-pressure applications and are especially valued for their simplicity and ease of installation.
Flare Fittings
Flare fittings involve flaring the end of a tube and securing it with a flare nut. These fittings are common in high-pressure environments and provide excellent mechanical strength and vibration resistance.
Crimp Fittings
Crimp fittings are permanently attached to hoses using a hydraulic crimping machine. These fittings provide robust, leak-free connections and are ideal for high-pressure, high-vibration environments.
O-ring Face Seal (ORFS) Fittings
ORFS fittings use an O-ring seated in a groove on the face of the fitting to create a secure, leak-free seal. They are highly reliable under high pressure and widely used in heavy-duty machinery and hydraulic systems.
Pipe Fittings
Standardized threaded fittings that connect pipes in hydraulic systems. While cost-effective and easy to find, they are more prone to leakage and are typically reserved for low-pressure applications.
Push-to-Connect Fittings
Designed for speed and ease of use, these fittings allow for quick connection and disconnection without the need for tools. Consequently, they are ideal for low-pressure applications and are commonly found in industrial automation and light-duty machinery.
Key Functions of Hydraulic Fittings
Hydraulic fittings do far more than simply connect two components. Their role is central to maintaining the performance and safety of hydraulic systems, especially under extreme operational conditions. Here are the key functions they perform:
1. Leak-Free Connections
One of the most critical requirements in hydraulic systems is preventing fluid leakage. Hydraulic fittings must maintain tight seals even under high pressure and temperature fluctuations. Leaks not only reduce system efficiency but also pose serious safety and environmental hazards.
2. Pressure Integrity
Hydraulic systems operate at pressures that often exceed 3,000 psi (pounds per square inch). Therefore, a fitting failure at this level can result in serious equipment damage or even operator injury. However, when fittings are properly selected and installed, they help ensure the system maintains consistent pressure and flow rates.
3. Maintenance and Modularity
Fittings allow for modular system design, making it easier to assemble, disassemble, inspect, and maintain various parts of a hydraulic system. This is particularly important in industries where downtime can result in significant financial loss.
4. Flexible Routing and Component Integration
Hydraulic fittings are available in various shapes and connection types (elbows, tees, crosses) that enable complex routing of hoses and tubes, helping engineers optimize spatial layouts and component positioning.
Applications in the Automotive Industry
The automotive industry relies heavily on hydraulic systems for performance, safety, and automation. Consequently, hydraulic fittings in this sector are specifically engineered to handle high pressure, extreme temperatures, and the vibrations commonly found in automotive environments.
Brake Systems
Hydraulic fittings play a critical role in braking systems by connecting master cylinders to brake calipers. Since these systems rely on pressurized brake fluid for immediate response, they require fittings that provide high reliability and ensure zero leakage.
Power Steering
Modern vehicles use hydraulic power steering systems, where fittings connect the steering pump, rack, and fluid reservoirs. These connections must be flexible and strong enough to endure continuous motion and pressure surges.
Automatic Transmissions
Hydraulic circuits in automatic transmissions rely on a network of fittings to manage gear shifts and lubrication. Precision and durability are crucial here, as failure can lead to costly transmission damage.
Usage in the Construction Industry
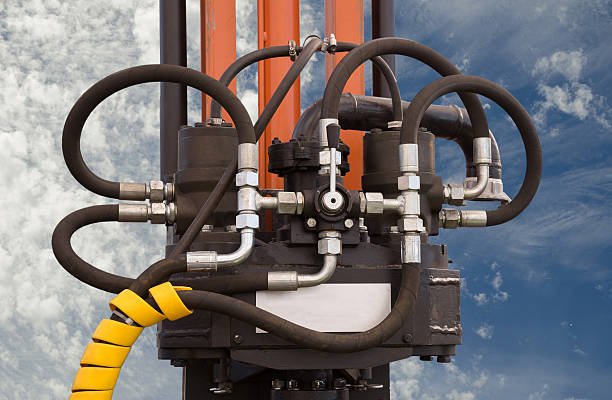
Construction equipment like excavators, backhoes, cranes, and bulldozers use extensive hydraulic systems for lifting, digging, and moving heavy loads. Hydraulic fittings in these machines must endure harsh environments, including dust, moisture, and vibration.
Hydraulic Cylinders
Fittings connect the hydraulic pump to the actuators (cylinders) that power the arm or bucket of machinery. These connections are constantly under stress and must resist loosening or leaking under extreme operational loads.
Hydraulic Motors
For machines requiring rotary motion (e.g., trenchers, augers), hydraulic motors are used. The fittings supplying these motors need to be able to handle rapid pressure spikes and continuous operation.
Attachment and Tool Integration
Many machines use interchangeable tools — such as hydraulic hammers or compactors — which connect via quick-disconnect fittings. These fittings allow fast changeover on the job site while maintaining pressure integrity and safety.
Role in Aerospace Engineering
In aerospace, hydraulic systems are mission-critical. Aircraft use them for functions ranging from flight control to landing gear deployment. The extreme conditions in aviation — such as high altitude, rapid temperature shifts, and vibration — require fittings of the highest precision and durability.
Flight Control Systems
Hydraulic fittings help operate flight surfaces such as ailerons, elevators, and rudders. These systems require pinpoint accuracy and rapid response, demanding fittings that can maintain tight seals under fluctuating loads and harsh atmospheric conditions.
Landing Gear Mechanisms
Hydraulics control the deployment and retraction of landing gear. The fittings in these assemblies must perform flawlessly during every flight cycle, supporting high-pressure fluid movement within compact and tightly engineered systems.
Emergency and Backup Systems
Aircraft also include redundant hydraulic systems for safety. Fittings in these backup lines must be equally robust, ready to activate during critical moments without failure or leakage.
Hydraulic Fittings in Agriculture
Modern agricultural machinery has evolved far beyond simple mechanical tools. Tractors, combines, seeders, and sprayers now rely on advanced hydraulic systems for efficiency, power, and automation. Fittings in these systems must withstand dirt, moisture, and variable weather conditions.
Hydraulic Lifting and Tilting
Hydraulic fittings are used to connect the lifting arms, front loaders, and three-point hitches in tractors. These components frequently change position under load, requiring fittings that offer both flexibility and strength.
Spraying and Seeding Systems
Precision agriculture equipment uses hydraulics to control spray booms and seeders. Fittings must ensure consistent flow rates and pressures to support the precise application of fertilizers, pesticides, and seeds.
Harvesting Equipment
Combine harvesters and balers use hydraulic-powered components such as conveyor belts and cutting mechanisms. The fittings involved must resist vibration and exposure to plant residues, ensuring consistent output during long workdays.
Marine Industry Applications
Marine environments introduce a unique set of challenges — saltwater corrosion, constant movement, and tight spatial constraints. Hydraulic systems in this industry are used for propulsion, steering, cargo handling, and safety mechanisms, requiring fittings that are exceptionally corrosion-resistant and reliable.
Steering and Navigation Systems
Hydraulic steering systems rely on fittings to connect pumps, rams, and reservoirs. These fittings must offer absolute integrity to prevent fluid leaks that could compromise maneuverability at sea.
Deck Machinery and Winches
Hydraulics power mooring winches, cranes, and anchor handling gear. These components operate under heavy loads and frequent starts and stops. Fittings must handle dynamic pressures and resist both corrosion and mechanical fatigue.
Hatch Covers and Cargo Doors
Hydraulic fittings are also used in automated hatch covers and cargo doors, where safe, watertight seals are essential. Stainless steel and brass fittings are typically used here to ensure durability and prevent rust over time.
Use in Manufacturing and Automation
Manufacturing environments are increasingly automated, relying heavily on hydraulic power for precise, repeatable motion in assembly lines and robotic systems. Hydraulic fittings in this sector must ensure high cycle durability, minimal maintenance, and compatibility with complex control systems.
Robotic Arms
Industrial robotic arms used for welding, painting, or part assembly utilize compact hydraulic systems. The fittings used must accommodate rapid motion, tight bends, and frequent directional changes while maintaining fluid integrity and minimizing pressure drop.
Conveyor Systems
Heavy-duty conveyors use hydraulic drives for load-bearing rollers and lifting platforms. Fittings here must handle continuous operation and offer easy disconnection for maintenance without disrupting overall plant workflow.
Hydraulic Presses and Molding Machines
In injection molding, metal forming, and stamping operations, large hydraulic presses rely on fittings that can endure extreme pressures and repeated use. The reliability of these fittings directly affects production uptime and component quality.
Importance in Oil and Gas Industry
The oil and gas sector operates under some of the harshest environmental and operational conditions, making the performance of hydraulic fittings especially critical. Applications range from offshore drilling rigs to onshore processing facilities, all requiring high-pressure, corrosion-resistant, and explosion-proof components.
Valve Actuation Systems
Remote-controlled hydraulic valve actuators regulate the flow of oil and gas. These systems use fittings to connect pumps to actuators, often over long distances. Any leak or failure can lead to operational delays and environmental hazards.
Drilling Equipment
Hydraulics are essential in powering rotary tables, top drives, and pipe handling systems. The fittings must withstand shock loads, vibration, and exposure to drilling muds and chemicals. Stainless steel and special alloys are commonly used for these applications.
Blowout Preventers (BOPs)
BOPs are critical safety devices used in drilling operations to seal wells in emergencies. Their hydraulic systems rely on ultra-reliable fittings that must perform flawlessly under immense pressure to prevent catastrophic failures.
Utilization in Renewable Energy Systems
Hydraulic systems are gaining traction in the renewable energy sector, particularly in wind, hydro, and solar installations. Fittings in these applications need to support long lifespans with minimal maintenance while operating in remote or elevated locations.
Wind Turbines
Hydraulic pitch systems control the angle of turbine blades to optimize wind capture. Fittings must endure exposure to moisture, temperature fluctuations, and vibrations within nacelles located hundreds of feet above the ground.
Solar Panel Trackers
Some large-scale solar farms use hydraulic actuators to move solar panels and follow the sun’s path. Fittings in these systems must allow precise motion control and resist corrosion from outdoor exposure.
Hydroelectric Dams
Hydraulic systems control sluice gates and turbine flow mechanisms in hydroelectric plants. These fittings must remain operational for decades under heavy pressure and in constant contact with water, making stainless steel and bronze ideal choices.
Benefits of Using the Right Hydraulic Fittings
Choosing the correct hydraulic fitting isn’t just a matter of compatibility; it has a direct impact on system performance, operational efficiency, and workplace safety. The right fittings can transform system reliability and reduce long-term operating costs.
Improved System Efficiency
Properly sized and matched fittings minimize flow restrictions, reduce pressure drops, and maintain consistent fluid velocity. This boosts overall energy efficiency and ensures smoother operation across applications.
Reduced Maintenance Costs
High-quality fittings reduce the frequency of leaks, component wear, and failure. This translates to less downtime, lower labor costs for repairs, and extended equipment lifespan.
Enhanced Safety
Leaks and blowouts can pose serious hazards, especially in high-pressure or high-temperature systems. Using the correct fittings ensures compliance with safety standards and significantly lowers the risk of workplace accidents.
Longer Equipment Lifespan
Reduced vibration, improved sealing, and corrosion resistance all contribute to less wear and tear on hydraulic components, helping machinery last longer and operate with greater reliability.
Material Considerations
Hydraulic fittings come in a variety of materials, each selected based on the application’s environmental and mechanical demands. Material selection plays a crucial role in the fitting’s durability, performance, and cost-effectiveness.
Stainless Steel
Highly resistant to corrosion and oxidation, stainless steel fittings are ideal for marine, chemical, and food-grade applications. They are slightly more expensive but offer unmatched longevity and cleanliness.
Carbon Steel
Carbon steel fittings are strong, durable, and suitable for high-pressure systems. They are often coated with zinc or chrome to enhance corrosion resistance and are widely used in industrial and automotive applications.
Brass
Brass fittings offer excellent corrosion resistance and are easy to machine, making them a good choice for low to medium pressure applications, including agriculture and plumbing systems.
Plastic and Composite Materials
Used primarily in low-pressure systems, these fittings are lightweight and corrosion-resistant. They’re common in water filtration systems and some agricultural machinery, but not suitable for heavy-duty use.
Safety and Maintenance Tips
Even the best hydraulic fittings can fail without proper care. Adopting rigorous maintenance practices ensures reliability, performance, and system longevity. Here are best practices to follow:
Regular Inspection
Conduct routine checks for leaks, cracks, or wear. Pay special attention to areas exposed to high vibration or environmental stress. Early detection prevents minor issues from becoming major failures.
Proper Installation Techniques
Always follow manufacturer torque specifications and use appropriate tools during installation. Avoid over-tightening or misalignment, which can damage threads and sealing surfaces.
Use Compatible Components
Ensure all components — hoses, tubes, and fittings — are compatible in terms of pressure rating, material, and thread type. Mismatched parts are a common cause of system failure.
Replace Worn or Damaged Parts Promptly
Do not attempt to repair damaged fittings. Replace them immediately with certified, quality parts to maintain system integrity and avoid costly breakdowns.
Conclusion
Hydraulic fittings are critical connectors that ensure the safe and efficient operation of fluid power systems across industries. From aerospace to agriculture, their role in maintaining pressure integrity, leak resistance, and system flexibility cannot be overstated.
Choosing the right type, material, and configuration — and maintaining fittings properly — can lead to dramatic improvements in system performance, cost savings, and operational safety. As industries evolve toward greater automation and sustainability, hydraulic fittings will continue to be foundational to industrial innovation and efficiency.
FAQs
1. How do I choose the correct hydraulic fitting for my application?
Start by identifying your system’s pressure requirements, fluid type, temperature range, and material compatibility. You’ll also need to match fitting types with hose or tube specifications and consider environmental factors like vibration or exposure to chemicals.
2. What is the difference between JIC and ORFS fittings?
JIC (Joint Industry Council) fittings use a 37-degree flare for sealing and are commonly used in medium-pressure systems. ORFS (O-Ring Face Seal) fittings provide a more robust seal using an O-ring and are ideal for high-pressure, leak-sensitive applications.
3. Can I mix different brands of hydraulic fittings?
While some fittings may appear interchangeable, mixing brands can lead to mismatched threads or sealing surfaces, increasing the risk of leaks or failure. Always ensure compatibility by checking industry standards (e.g., SAE, ISO) or sticking to one manufacturer.
4. What causes hydraulic fitting failures most often?
Common causes include incorrect installation, over-tightening, vibration fatigue, material incompatibility, and exposure to corrosive fluids. Regular inspection and preventive maintenance can help avoid premature failure.
5. Are quick-connect fittings reliable for heavy-duty applications?
Quick-connect fittings can be reliable if rated for high pressure and installed correctly. However, they are generally more common in mobile or light-duty systems. For extreme environments or constant flow systems, crimped or ORFS fittings are usually preferred.