Introduction
Hydraulic flanges play a critical role in fluid power systems, providing secure connections between different components of hydraulic machinery. These specialized mechanical connectors ensure high-pressure integrity, prevent leaks, and allow for easy assembly and disassembly of hydraulic lines. With industries increasingly relying on hydraulics for automation, mobility, and heavy-duty operations, understanding the ins and outs of hydraulic flanges is more important than ever.
This comprehensive guide covers everything you need to know about hydraulic flanges—from types and industry standards to installation tips and future trends. This article aims to deepen your knowledge and help you make informed decisions—whether you are a hydraulic engineer, maintenance technician, or equipment supplier.
What Is a Hydraulic Flange?
Engineers use hydraulic flanges to connect pipes, hoses, and other components in a hydraulic system. They design flanges to handle high pressure and reduce leakage risks. Technicians typically install them in areas that require frequent maintenance or experience high mechanical stress. Unlike simple threaded or crimped connectors, hydraulic flanges offer robust sealing capabilities through precision machining and the use of O-ring face seals (ORFS).
Manufacturers commonly use carbon steel or stainless steel to produce these flanges and apply protective coatings such as zinc-nickel or phosphate to help them withstand harsh industrial environments. Engineers use them extensively in construction, oil and gas, and marine systems because they are durable and easy to install.
Types of Hydraulic Flanges
SAE Code 61 vs SAE Code 62 Flanges
The SAE J518 standard defines SAE Code 61 and Code 62 flanges, which engineers widely use in hydraulic applications. Code 61 flanges handle medium pressure, typically up to 3,000 psi, while Code 62 flanges support high-pressure systems reaching up to 6,000 psi. They are not interchangeable due to differences in bolt patterns and pressure ratings.
Threaded Flanges
Threaded flanges are used in systems where welding is not feasible. They feature internal threads that match the threads of pipes or fittings, making installation quick and straightforward. These flanges are ideal for low to moderate pressure applications but are less reliable under vibration or thermal expansion conditions.
Split Flanges
Split flanges consist of two interlocking halves that bolt together around a hydraulic fitting. This design facilitates easy maintenance, especially in confined spaces or retrofit installations. They often comply with ISO 6162 standards and are used in high-pressure lines with large diameter pipes.
Hydraulic Flange Standards
SAE J518 Standard
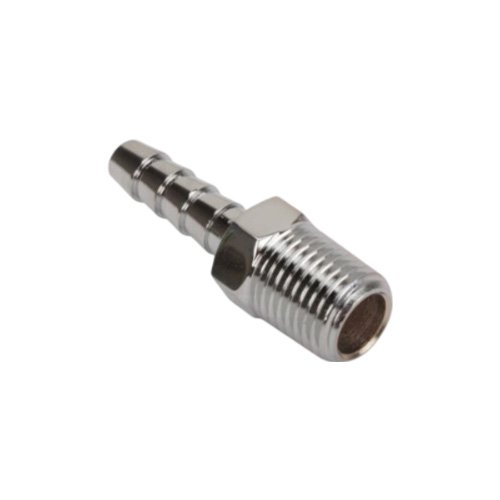
The SAE J518 standard, established by the Society of Automotive Engineers, governs the design, dimensions, and performance of hydraulic flanges, particularly Code 61 and Code 62. These standards ensure global interoperability, quality control, and compatibility across different manufacturers and systems.
ISO 6162-1 & 6162-2
ISO 6162-1 corresponds to Code 61 flanges, while ISO 6162-2 covers Code 62 high-pressure flanges. Both provide detailed guidelines on flange dimensions, bolt hole patterns, and pressure ratings. Following ISO standards is essential for international operations and export-oriented machinery manufacturers.
ANSI/ASME B16.5 and DIN Standards
Engineers also use ANSI/ASME B16.5 flanges and DIN (Deutsches Institut für Normung) flanges in fluid systems when they need to connect piping with hydraulic components, even though these flanges are not exclusively hydraulic. These standards primarily cover material specifications, flange face types (raised, flat, or ring-type joint), and pressure classes.
Key Components and Features
O-Ring Face Seal (ORFS)
One of the defining characteristics of hydraulic flanges is the O-ring face seal. This feature enhances sealing performance by preventing fluid leakage under high pressure. The O-ring, typically made of nitrile or Viton, sits in a machined groove on the flange face and compresses upon tightening to create a reliable seal.
Bolt Patterns and Pressure Ratings
Hydraulic flanges are engineered with specific bolt patterns to ensure uniform clamping and to prevent deformation under pressure. The number and size of bolts directly influence the flange’s pressure-handling capabilities. Proper alignment and torque application are crucial during installation to achieve maximum performance.
Surface Finishes and Coatings
To extend their lifespan and resist corrosion, hydraulic flanges are often coated with materials such as zinc-nickel, phosphate, or chrome. Smooth surface finishes not only enhance sealing efficiency but also reduce the risk of O-ring damage during assembly. Advanced coatings can also provide dielectric insulation and improved wear resistance.
Materials and Coatings Used
Carbon Steel
Manufacturers most commonly use carbon steel to make hydraulic flanges because of its strength, durability, and cost-effectiveness. They typically treat it with anti-corrosive coatings to extend its service life in industrial environments.
Stainless Steel
Stainless steel offers superior corrosion resistance, making it ideal for marine, offshore, and food-grade applications. Engineers prefer it—despite the higher cost—when hygiene, chemical exposure, or saltwater environments are a concern.
Zinc-Nickel, Phosphate, and Chrome Plating
These coatings serve multiple purposes: preventing corrosion, improving appearance, and reducing friction during assembly. Zinc-nickel is especially noted for its high corrosion resistance, while phosphate provides a good base for painting and rust prevention. Chrome plating adds hardness and enhances surface finish quality.
Applications Across Industries
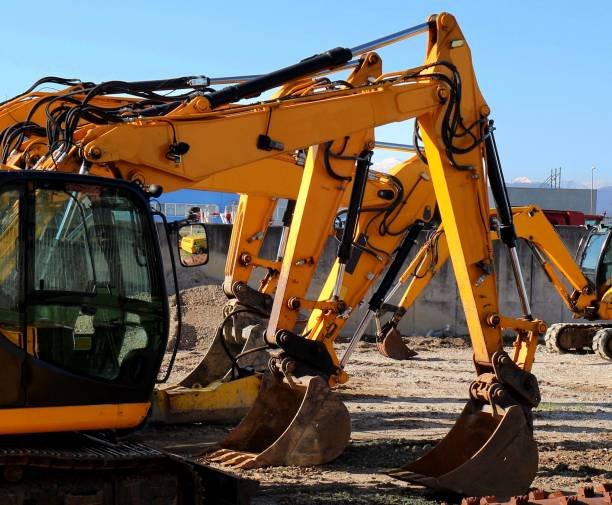
Construction Equipment
Hydraulic flanges are essential in construction machinery such as excavators, bulldozers, and cranes. These machines rely on high-pressure hydraulic systems for power and movement, where flanges provide robust and secure connections capable of withstanding rough terrain and heavy loads.
Agricultural Machinery
In agriculture, hydraulic flanges are used in tractors, harvesters, and irrigation systems. They enable efficient fluid transfer and system maintenance, which is crucial for time-sensitive farming operations. Resistance to dirt, dust, and vibration makes them ideal for outdoor and off-road applications.
Marine Hydraulics
Ships, submarines, and offshore platforms use hydraulic flanges in steering systems, winches, and stabilizers. The flanges must resist saltwater corrosion and high pressure, which is why stainless steel and corrosion-resistant coatings are frequently used in marine environments.
Oil and Gas Sector
In the oil and gas industry, hydraulic flanges are employed in drilling rigs, pipeline systems, and blowout preventers. These applications demand high reliability and adherence to strict industry standards due to the risk and complexity involved in operations.
Aerospace and Defense
Precision, reliability, and weight are critical in aerospace and defense applications. Manufacturers make the hydraulic flanges used here from lightweight, high-strength alloys and ensure they comply with rigorous safety and performance standards. Engineers often integrate them into flight control systems, landing gear, and weapon mechanisms.
Benefits of Using Hydraulic Flanges
Leak Prevention
One of the most important benefits of hydraulic flanges is their ability to prevent leaks. The O-ring seal and precision machining ensure a tight fit that can handle high-pressure fluids without failure, even under extreme environmental conditions.
Pressure Handling
Hydraulic flanges are specifically designed to operate in high-pressure environments, often exceeding 3,000 psi. The use of robust materials and engineering designs allows them to maintain integrity and performance under these demanding conditions.
Ease of Maintenance and Replacement
Flanged connections allow for quick disassembly and reassembly of hydraulic systems, reducing downtime during maintenance. This modularity also simplifies troubleshooting and part replacement, making hydraulic flanges a preferred choice for complex systems requiring regular servicing.
Choosing the Right Hydraulic Flange
Compatibility and System Pressure
Selecting the appropriate hydraulic flange involves ensuring that it matches the system’s pressure requirements and other components. Using mismatched flanges can lead to failure and safety hazards, so it’s crucial to follow manufacturer recommendations and industry standards.
Corrosion Resistance Needs
Environmental conditions—such as exposure to chemicals, moisture, or salt—must be considered when choosing flange materials and coatings. Stainless steel or zinc-nickel-plated flanges offer superior corrosion resistance for harsh operating environments.
Space and Installation Constraints
Installation space often dictates the choice of flange design. Engineers choose split flanges for confined or hard-to-access areas, while they prefer weld neck flanges for large, open systems that require permanent installation.
Applications Across Industries
Construction Equipment
Hydraulic flanges are essential in construction machinery such as excavators, bulldozers, and cranes. These machines rely on high-pressure hydraulic systems for power and movement, where flanges provide robust and secure connections capable of withstanding rough terrain and heavy loads.
Agricultural Machinery
In agriculture, hydraulic flanges are used in tractors, harvesters, and irrigation systems. They enable efficient fluid transfer and system maintenance, which is crucial for time-sensitive farming operations. Resistance to dirt, dust, and vibration makes them ideal for outdoor and off-road applications.
Marine Hydraulics
Ships, submarines, and offshore platforms use hydraulic flanges in steering systems, winches, and stabilizers. Engineers design the flanges to resist saltwater corrosion and high pressure, which is why they frequently use stainless steel and apply corrosion-resistant coatings in marine environments.
Oil and Gas Sector
Engineers use hydraulic flanges in the oil and gas industry for drilling rigs, pipeline systems, and blowout preventers. These applications demand high reliability and adherence to strict industry standards due to the risk and complexity involved in operations.
Aerospace and Defense
Precision, reliability, and weight are critical in aerospace and defense applications. Manufacturers produce the hydraulic flanges used here from lightweight, high-strength alloys and ensure they meet rigorous safety and performance standards. Engineers often integrate these flanges into flight control systems, landing gear, and weapon mechanisms.
Benefits of Using Hydraulic Flanges
Leak Prevention
One of the most important benefits of hydraulic flanges is their ability to prevent leaks. The O-ring seal and precision machining ensure a tight fit that can handle high-pressure fluids without failure, even under extreme environmental conditions.
Pressure Handling
Hydraulic flanges are specifically designed to operate in high-pressure environments, often exceeding 3,000 psi. The use of robust materials and engineering designs allows them to maintain integrity and performance under these demanding conditions.
Ease of Maintenance and Replacement
Flanged connections allow for quick disassembly and reassembly of hydraulic systems, reducing downtime during maintenance. This modularity also simplifies troubleshooting and part replacement, making hydraulic flanges a preferred choice for complex systems requiring regular servicing.
Choosing the Right Hydraulic Flange
Compatibility and System Pressure
Selecting the appropriate hydraulic flange involves ensuring that it matches the system’s pressure requirements and other components. Using mismatched flanges can lead to failure and safety hazards, so it’s crucial to follow manufacturer recommendations and industry standards.
Corrosion Resistance Needs
Engineers must consider environmental conditions—such as exposure to chemicals, moisture, or salt—when selecting flange materials and coatings. Stainless steel or zinc-nickel-plated flanges offer superior corrosion resistance for harsh operating environments.
Space and Installation Constraints
Installation space often dictates the choice of flange design. Engineers often choose split flanges for confined or hard-to-access areas, while they prefer weld neck flanges in large, open systems that require permanent installation.
Installation Best Practices
Torque Specifications
Proper torque application is essential when installing hydraulic flanges. Under-tightening can result in leaks, while over-tightening can damage the flange or deform the O-ring. Always refer to manufacturer-provided torque charts that correspond to the specific flange size and material used.
Seal Alignment and Bolt Tightening Sequence
Correct alignment of the O-ring face seal is critical to avoid cutting or displacing the seal during assembly. When tightening bolts, follow a cross-pattern sequence to ensure even compression across the flange face. This method reduces stress concentrations and improves sealing effectiveness.
Inspection Tips
Inspect all mating surfaces for debris, scratches, or nicks before installation. Check O-rings for signs of wear or damage. After installation, visually inspect the flange for gaps or misalignment and test the system under pressure to verify seal integrity.
Common Problems and Troubleshooting
Leak Diagnosis
Leaks often result from improperly installed O-rings, incorrect torque, or damage to flange surfaces. Use a clean cloth to identify the leak source and avoid using sealants that may contaminate the system. If the O-ring is pinched or cut, it should be replaced immediately.
Pressure Loss
Unexpected pressure drops may indicate internal leakage or improper flange engagement. Inspect connections for alignment, verify torque specifications, and ensure no components are worn or degraded. System pressure tests can help pinpoint the issue more accurately.
Vibration and Fatigue Failures
Vibration from pumps, motors, or nearby equipment can lead to flange fatigue over time. Use vibration dampers, secure mounting brackets, and regularly inspect for microcracks or signs of wear around the bolt holes and mating faces.
Innovations and Trends in Hydraulic Flanges
Smart Sensors and Predictive Maintenance
Modern hydraulic systems increasingly incorporate sensors that monitor flange pressure, temperature, and vibration. These sensors feed real-time data into predictive maintenance software, allowing technicians to address issues before they lead to system failures.
Advanced Materials
Manufacturers are introducing new materials like duplex stainless steel and polymer composites for specialized flange applications to provide a balance of strength, corrosion resistance, and weight savings. These materials are particularly relevant in aerospace and offshore applications.
Modular Flange Systems
Modular flange designs allow for flexibility and scalability in complex hydraulic systems. They enable engineers to configure systems without custom machining, speeding up prototyping and reducing manufacturing costs. This trend supports just-in-time manufacturing and rapid system reconfiguration.
Maintenance and Lifespan
Regular Inspection Intervals
Maintenance teams should schedule routine inspections based on the system’s operating hours and environmental conditions. Visual checks, pressure tests, and torque verifications help detect early signs of wear or fatigue, ensuring continued performance and safety.
Signs of Wear
Common indicators of flange wear include corrosion, surface pitting, deformation, loose bolts, and degraded O-rings. Any unusual noise, vibration, or fluid seepage around the flange should prompt immediate investigation.
Repair vs Replacement Criteria
If a flange shows minor wear or surface damage, resurfacing or replacing the O-ring might restore function. However, flanges with cracks, warping, or significant corrosion should be replaced entirely to avoid system failure. Always follow OEM recommendations for part lifespan and service limits.
How to Source Quality Hydraulic Flanges
OEMs vs Aftermarket
OEM (Original Equipment Manufacturer) flanges guarantee compatibility and quality, making them ideal for critical or high-pressure systems. Aftermarket options may be more cost-effective but require thorough vetting for quality assurance and standards compliance.
Certifications and Supplier Audits
Reputable suppliers provide certifications like ISO 9001, API, or CE marking. Conducting supplier audits or requesting quality control documentation helps ensure you receive products that meet industry standards and performance expectations.
Buying Tips
When sourcing flanges, always verify pressure ratings, material composition, and dimensional compatibility. Request datasheets, inquire about warranty terms, and ensure the supplier supports technical documentation and after-sales service.
Conclusion
Hydraulic flanges are indispensable in building safe, efficient, and high-pressure fluid systems. From understanding types and standards to mastering installation and maintenance best practices, knowing the intricacies of these components enhances system reliability and longevity. As technologies advance, the integration of smart sensors and high-performance materials continues to transform the hydraulic landscape.
Whether you’re designing new systems or maintaining existing ones, always choose flanges that align with your operational needs and industry standards. For complex installations or specialized environments, consult with hydraulic experts to avoid costly mistakes and ensure long-term performance.
FAQs
What’s the difference between SAE and ISO flange standards?
SAE standards, such as J518, are primarily used in North America and define flanges by pressure ratings and bolt patterns (e.g., Code 61 and 62). Engineers and manufacturers internationally adopt ISO standards like 6162, often using them interchangeably with SAE standards when the classifications are compatible.
Can I reuse a hydraulic flange?
Yes, hydraulic flanges can be reused if they are undamaged and within wear tolerances. However, they should always replace the O-ring and inspect the mating surfaces for scratches or warping before reinstallation.
How do I know if my flange is leaking?
Signs of a leaking flange include visible fluid seepage, pressure drops, or pooling around the connection. A clean cloth or UV dye can be used to detect leaks more precisely. Always inspect O-rings and bolt torque when troubleshooting leaks.
What tools are needed for hydraulic flange installation?
Installation typically requires a calibrated torque wrench, alignment pins, clean cloths, O-ring lubricant, and possibly a dial indicator for precise measurements. Following the correct bolt sequence and torque specs is crucial for a secure fit.
How often should flanges be inspected?
Inspection frequency depends on operating conditions but generally ranges from every 500 to 1,000 operating hours. High-pressure or high-vibration systems may require more frequent checks to catch early signs of wear or fatigue.