Hydraulic systems are essential in a variety of industries, powering machinery, equipment, and tools that require high pressure to operate. One of the most critical elements in a hydraulic system is the hydraulic hose connection. Choosing the correct type to ensures optimal performance, efficiency, and safety. In this guide, we’ll explore the different types of hydraulic hose connections, their benefits, and how to select the best one for your system.
What is a Hydraulic Hose Connection?
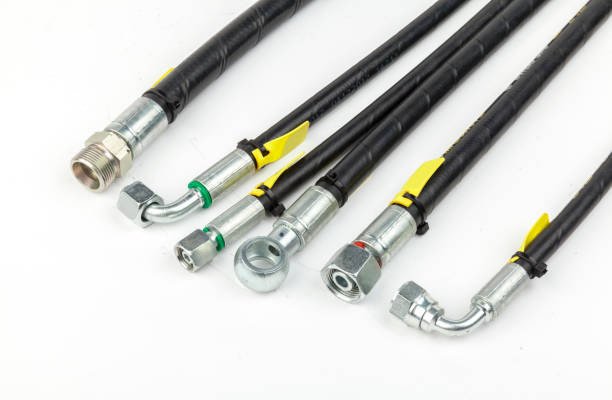
A hydraulic hose connection is a coupling that links hydraulic hoses to components such as pumps, cylinders, valves, and more. These connections allow hydraulic fluid to flow through the system under pressure, transmitting energy to perform various functions. They come in various shapes, sizes, and types to fit specific applications and system requirements.
Each connection type is designed to handle specific pressure levels, environmental conditions, and mechanical stresses. The right connection type improves system efficiency, reduces the risk of leaks, and enhances the overall longevity of the system. Whether you’re in construction, agriculture, or manufacturing, understanding hydraulic hose connection types is crucial for smooth operations.
Different Types of Hydraulic Hose Connections
There are several types of hydraulic hose connections used across different industries. The most common types include:
- Standard
- Quick-Connect
- Swivel
Each type has its own advantages and applications. Let’s dive deeper into the details of these types.
Standard Hydraulic Hose Connections
They are the most commonly used type, especially in industrial applications. These connections typically feature threads and require a proper seal to prevent leaks. Some common standard connection types include:
- BSP (British Standard Pipe): Often used in Europe and Asia, BSP threads are versatile and can handle high-pressure applications.
- NPT (National Pipe Thread): Common in North America, NPT threads provide a tight seal and are ideal for high-pressure environments.
- JIC (Joint Industrial Council): Known for its robust design, JIC connections provide a secure seal and are widely used in fluid power systems.
Standard connections are reliable and cost-effective, making them suitable for a wide range of hydraulic systems. However, they may require tools and expertise for proper installation and maintenance.
Quick-Connect Hydraulic Hose Connections
Quick-connect hydraulic hose connections are designed for easy, tool-free installation and removal. These connections allow for rapid connection and disconnection, making them ideal for systems that require frequent changes or maintenance. Some popular quick-connect types include:
- ISO A/B: These are universal quick-connect fittings used in various industries, providing secure connections without the need for threaded parts.
- NPTF (National Pipe Thread Fuel): NPTF connections are designed to prevent leaks in high-pressure applications and are commonly used in automotive and industrial systems.
- SAE (Society of Automotive Engineers): SAE fittings are designed for both hydraulic and pneumatic systems, ensuring a strong, leak-proof connection.
They save time and reduce labor costs. They are particularly useful in mobile equipment, maintenance, and other dynamic environments.
Swivel Hydraulic Hose Connections
Swivel hydraulic hose connections rotate to provide flexibility during installation and operation. Unlike standard connections, which remain fixed, swivel connections allow rotation at the connection point, reducing stress on hoses and preventing twisting or kinking. This feature is particularly beneficial in applications where hoses need to move or bend in multiple directions.
Hydraulic systems with mobile or rotating machinery, such as cranes, excavators, and agricultural equipment, often use these connections. By allowing freedom of movement, swivel hydraulic hose connections help to avoid premature wear and extend the service life of the hoses.
Advantages include:
- Reduced hose twisting and bending.
- Improved flexibility for dynamic applications.
- Enhanced durability and longer lifespan of hydraulic systems.
Material and Construction
The material and construction of hydraulic hose connections play a crucial role in their performance. Manufacturers make hydraulic hose connections from high-strength materials that withstand the demands of high-pressure and harsh operating environments. Common materials used include:
- Steel: Steel is a popular choice due to its strength, durability, and ability to withstand high pressures. It is commonly used for industrial and heavy-duty applications.
- Brass: Brass is resistant to corrosion, making it ideal for low- to medium-pressure systems exposed to moisture or chemicals.
- Stainless Steel: Stainless steel, known for its excellent corrosion resistance, is used in systems exposed to chemicals, high temperatures, or saltwater.
Choosing the right material is essential to ensure that the hose connections can handle the operating conditions. For example, if your system operates in a high-temperature environment, stainless steel or a material with better heat resistance may be necessary.
Factors that influence the choice of materials include:
- Pressure Rating: Different materials have different pressure ratings. Ensure that the material selected can handle the maximum pressure of your hydraulic system.
- Temperature Resistance: High-temperature applications require materials that can withstand heat without degrading or losing strength.
- Corrosion Resistance: In environments where exposure to moisture, chemicals, or saltwater is common, corrosion-resistant materials like stainless steel are preferred.
Choosing the Right Hydraulic Hose Connection for Your System
When selecting the right hydraulic hose connection, you must consider several factors to ensure optimal performance. Making the wrong choice can result in system failure, leaks, or inefficient operation. Here are the key factors to consider when choosing:
- Pressure: You must use connections rated for the pressure your system will generate. High-pressure systems require connections specifically designed to handle intense force.
- Temperature: The operating temperature range of the system is crucial when selecting materials for the hose connection. Choose materials that can withstand both high and low temperatures without failing.
- Environment: Consider whether the hydraulic system will face exposure to chemicals, moisture, dust, or extreme weather conditions. Some environments require specialized connections designed to resist corrosion and other environmental factors.
- Flow Rate: The connection must allow for the required flow rate of hydraulic fluid. Too small of a connection can result in pressure drops, while too large can lead to inefficient performance.
Improper hydraulic hose connections can lead to performance issues, such as pressure loss, overheating, or contamination. It’s crucial to evaluate the system’s requirements and match them with the appropriate connection type, material, and design.
Pressure Ratings
One of the most important factors when selecting hydraulic hose connections is ensuring that they match the required pressure ratings of your system. Each connection type handles a specific level of pressure, so choosing one that doesn’t meet the system’s pressure requirements can cause failure, leaks, or hazardous situations.
Manufacturers typically define pressure ratings, which can vary based on the material and design of the connection.Common pressure ratings include:
- Low-Pressure Systems: These systems generally operate at pressures below 1,000 psi. They are suitable for general applications such as agricultural machinery and light-duty equipment.
- Medium-Pressure Systems: These systems, with pressures ranging from 1,000 to 5,000 psi, are commonly used in industrial machinery, forklifts, and automotive applications.
- High-Pressure Systems: These systems operate at pressures above 5,000 psi and are typically used in critical applications like hydraulic presses, construction machinery, and aerospace systems.
To avoid safety hazards and ensure the longevity of the system, always choose hose connections that meet or exceed the system’s pressure rating. Over-pressurizing a system with incorrect connections can cause catastrophic failures.
Temperature and Types
Temperature can significantly affect the performance of hydraulic hose connections. High temperatures can cause materials to degrade or weaken, while low temperatures can result in brittle materials that are prone to cracking. Therefore, selecting the right hydraulic hose connection material for your system’s temperature range is essential for ensuring safe and efficient operation.
When selecting hydraulic hose connections, consider the following:
- High-Temperature Systems: For systems operating in high-temperature environments (above 250°F), use materials like stainless steel or heat-resistant alloys.
- Low-Temperature Systems: For cold weather applications, materials that remain flexible in freezing conditions (such as brass or special alloys) are ideal.
By choosing the correct material and connection type, you can prevent issues like leaks, material failure, or reduced performance caused by temperature extremes.
Environmental Factors
Hydraulic systems often operate in harsh environments that include exposure to moisture, chemicals, dirt, or extreme weather conditions. These factors can have a detrimental effect on the performance of hydraulic hose connections, causing corrosion, wear, or even failure. Therefore, selecting the right connection type for your environment is critical.
- Corrosion Resistance: In environments exposed to water, salt, or chemicals, corrosion-resistant materials like stainless steel are necessary to ensure the longevity of the system.
- Dust and Dirt: In dusty environments, you may need sealed connections and covers to prevent contaminants from entering the system and causing blockages or wear.
- UV Exposure: Select materials resistant to UV degradation, such as certain plastics and rubber compounds, for systems operating outdoors to prevent weakening of the hose connections.
Specialized hydraulic hose connections are available for extreme environments, providing additional protection against wear and failure. These connections are critical for maintaining system efficiency and safety in challenging conditions.
Maintenance and Troubleshooting
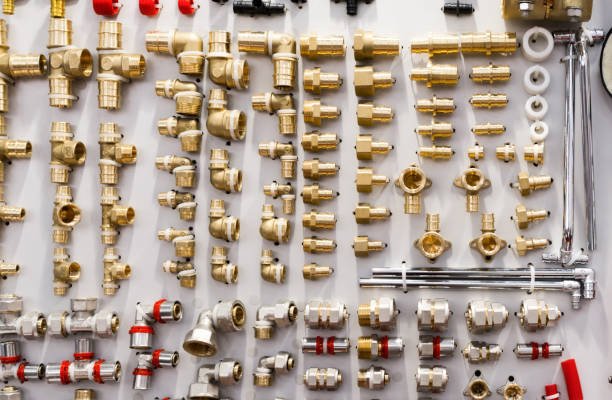
Regular maintenance and troubleshooting of hydraulic hose connections are essential for ensuring the long-term reliability and efficiency of the system. Some common maintenance tasks include:
- Inspection for Leaks: Periodically check for signs of fluid leakage at connection points. Leaks can lead to pressure loss and contamination of the system.
- Cleaning: Dust, dirt, and other debris can accumulate around hose connections. Regular cleaning prevents contamination and ensures smooth operation.
- Checking for Wear: Over time, hoses and connections may wear due to abrasion, vibration, or exposure to harsh chemicals. Inspect hoses for cracks or signs of damage.
If you experience issues like leaks or reduced performance, check the connection points, tighten all fittings properly, and verify that the pressure ratings and connection type match the system’s requirements.
Conclusion
Choosing the right hydraulic hose connection is crucial for ensuring the efficiency, safety, and longevity of a hydraulic system. By understanding the various types of connections, materials, and environmental factors, you can make an informed decision that optimizes system performance. Whether you’re working with industrial, mobile, or high-pressure systems, selecting the right connection type is key to preventing costly downtime and ensuring reliable operations.
By investing in high-quality, properly matched hydraulic hose connections, you are ensuring the longevity and performance of your hydraulic systems for years to come.
FAQs
Q1: What is a hydraulic hose connection?
A1: A hydraulic hose connection is a fitting used to join hydraulic hoses to other components in a hydraulic system. It ensures a secure, leak-proof connection for the transfer of hydraulic fluid.
Q2: What are the most common types of hydraulic hose connections?
A2: The most common types of hydraulic hose connections include threaded, quick-connect, flanged, and swivel connections.
Q3: How do I choose the right hydraulic hose connection for my system?
A3: Choose a hydraulic hose connection based on the system’s pressure, temperature, material compatibility, and environmental conditions to ensure optimal performance.
Q4: What materials are commonly used for hydraulic hose connections?
A4: Manufacturers often make hydraulic hose connections from steel, brass, or stainless steel, with each material offering unique benefits such as corrosion resistance or strength under pressure.
Q5: Can hydraulic hose connections be reused?
A5: You can reuse hydraulic hose connections if they are not damaged and have been properly inspected for wear or corrosion. Always check for leaks or cracks before reuse.
Q6: How often should hydraulic hose connections be maintained?
A6: Inspect hydraulic hose connections regularly for leaks, wear, and corrosion. Check them at least once every 3 to 6 months, depending on system usage.