Introduction
Hydraulic systems play a critical role in a wide range of industries, from heavy equipment to aerospace technology. These systems rely on pressurized fluid to transmit energy and perform work, often in high-stress or high-pressure environments. One of the often-overlooked yet crucial components in maintaining the integrity and efficiency of these systems is the hydraulic swivel fitting.
Without proper fittings, even the most advanced hydraulic systems can suffer from leaks, reduced performance, or complete failure. Swivel fittings help combat these challenges by allowing for controlled rotational movement between hoses and components. This reduces wear and tear, enhances safety, and extends the service life of the system.
What Are Hydraulic Swivel Fittings?
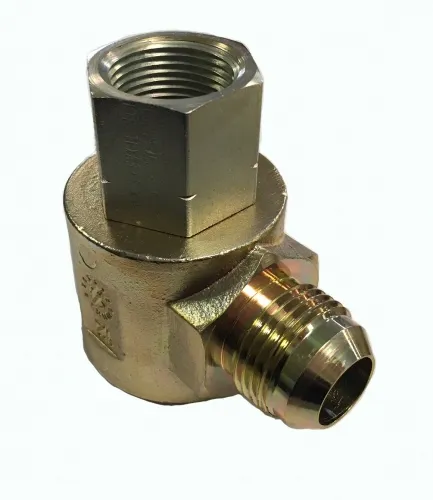
Hydraulic swivel fittings are specialized connectors designed to allow rotational movement while maintaining a secure, leak-free seal in hydraulic systems. Unlike standard hydraulic fittings—which are rigid and prone to causing hose twisting or kinking—swivel fittings provide 360-degree rotational capability between different parts of a hydraulic assembly.
They are essential wherever hoses or components need to move freely under pressure without causing stress on the hydraulic line. These fittings are commonly used in systems that involve repetitive motion or oscillating components, offering a reliable solution to dynamic hydraulic challenges.
Swivel fittings come in various shapes, sizes, and configurations, allowing them to be customized for different applications. Whether it’s in a mobile excavator arm or a marine winch system, the right swivel fitting can drastically improve efficiency and longevity.
Key Components and Design Features
A hydraulic swivel fitting typically consists of several critical components that work together to ensure both rotational flexibility and a tight hydraulic seal:
1. Body
The body serves as the main structure of the fitting and is often crafted from high-strength materials like carbon steel, stainless steel, or brass. The body is designed to withstand high pressures and corrosive environments.
2. Seals
Manufacturers use high-performance seals to prevent fluid leakage during operation. They commonly make these seals from materials such as nitrile (NBR), Viton, or PTFE, depending on the fluid type and operating temperature. In demanding applications, they sometimes use multi-seal designs for added security.
3. Bearings
Bearings allow the rotating and stationary components to move independently without causing internal wear. Precision ball or roller bearings are often employed to support smooth rotation even under load and high-pressure conditions.
4. Ports and Threads
Depending on the application, swivel fittings are available with various port types such as NPT, JIC, SAE, BSP, and ORFS. The correct threading ensures compatibility with other hydraulic components.
The design must balance the need for flexibility with the requirement for mechanical strength and pressure resistance. Engineers often select fittings based on specific system parameters, including operating pressure, flow rate, and rotational demands.
How Do Hydraulic Swivel Fittings Work?
Hydraulic swivel fittings function by enabling rotational movement between connected components without compromising the integrity of the hydraulic seal. The fitting contains an internal bearing mechanism that allows the outer body (connected to the hose or pipe) to rotate around a central axis while the inner body remains stationary—or vice versa—depending on the design.
These fittings are engineered to handle high-pressure fluid flow even as they rotate. The use of specialized seals ensures that the hydraulic fluid does not escape during operation. Some high-performance swivel fittings can support rotational movements under pressures exceeding 5,000 PSI, making them suitable for rugged industrial applications.
There are typically two movement types in hydraulic swivel joints:
- Single-plane rotation: Rotation around one axis, commonly used in standard equipment like tractors or forklifts.
- Multi-plane rotation: Allows movement in multiple axes, often used in complex assemblies such as robotic arms or construction machinery.
The core advantage lies in preventing hose twisting, which is a major cause of premature hose failure. By maintaining flexibility while preserving hydraulic pressure, swivel fittings significantly reduce downtime and maintenance costs.
Applications of Hydraulic Swivel Fittings
Many industries use hydraulic swivel fittings where rotational motion and pressurized fluid transmission must coexist. Below are some of the key application areas:
1. Industrial Machinery
In manufacturing plants, swivel fittings are used in injection molding machines, stamping presses, and CNC machines. They ensure reliable fluid transmission in dynamic systems where parts constantly move or vibrate.
2. Agricultural Equipment
Swivel fittings are essential in tractors, harvesters, and irrigation systems where constant motion and shifting angles are the norm. They help maintain fluid flow without causing hose fatigue.
3. Construction and Mining
Excavators, bulldozers, and hydraulic rock drills utilize swivel joints to accommodate rotating arms and booms. These fittings are built to handle extreme pressures and dirty environments.
4. Marine and Offshore Platforms
On ships and oil rigs, swivel fittings ensure fluid power for cranes, winches, and propulsion systems. Corrosion-resistant materials like stainless steel are often used in these applications.
5. Aerospace and Defense
Hydraulic swivel fittings are used in aircraft landing gear, weapon systems, and flight control mechanisms. They provide precise, high-reliability movement in mission-critical applications.
Types of Hydraulic Swivel Fittings
Hydraulic swivel fittings come in several configurations to meet diverse operational needs. Understanding the different types can help engineers and maintenance teams select the right fitting for their system.
1. In-line Swivel Fittings
These are the most common type, allowing for axial rotation along the flow path. They are ideal for reducing hose twist in straight-line systems.
2. 90-Degree Swivel Fittings
These fittings offer a right-angle design, allowing both directional and rotational flexibility. Often used in tight spaces or systems with complex geometries.
3. Flange Swivel Joints
Engineers commonly use flange-mounted designs in heavy-duty applications like marine cranes and drilling platforms because these designs provide high-pressure tolerance.
4. Custom Swivel Configurations
Some manufacturers offer custom-engineered swivel joints tailored to unique system specifications, including multi-port options and compact form factors.
Selecting the right type depends on the application’s spatial constraints, pressure requirements, and range of motion needed.
Benefits of Using Hydraulic Swivel Fittings
Implementing hydraulic swivel fittings in fluid power systems offers numerous advantages; moreover, these benefits contribute to better performance, reduced downtime, and increased equipment longevity.
1. Reduced Hose Twisting and Wear
One of the primary causes of hydraulic hose failure is torsional stress caused by twisting during operation. Swivel fittings eliminate this issue by allowing the hose to rotate freely, significantly extending the hose lifespan.
2. Enhanced Equipment Longevity
By minimizing stress on hydraulic components, swivel fittings prevent damage to hoses, connectors, and seals. This leads to fewer replacements and longer intervals between maintenance, ultimately improving the overall life expectancy of the system.
3. Improved Safety and Reliability
Hydraulic leaks and bursts are hazardous, particularly in high-pressure systems. Swivel fittings reduce the risk of these failures by ensuring secure, flexible connections. Their rotational capability also helps maintain proper hose alignment, reducing potential for accidents and equipment failure.
4. Increased System Efficiency
By maintaining consistent fluid flow and reducing unnecessary resistance caused by kinked hoses, swivel fittings help improve system responsiveness and energy efficiency.
Materials and Coatings
The materials and coatings used in constructing hydraulic swivel fittings largely influence their performance and durability. Therefore, choosing the right combination ensures compatibility with system fluids and resistance to environmental factors.
1. Steel and Stainless Steel
Engineers widely use carbon steel for its strength and cost-effectiveness, while they choose stainless steel for its superior corrosion resistance, especially in marine, chemical, or food-grade applications.
2. Brass
Brass fittings are suitable for low to moderate pressure systems and provide good resistance to water and some hydraulic oils. They are commonly found in agriculture and light-duty equipment.
3. Plating and Surface Treatments
Many swivel fittings feature coatings such as zinc plating, trivalent chrome, or electroless nickel to enhance corrosion resistance. Manufacturers apply these coatings to protect fittings in outdoor or corrosive environments where they are exposed to moisture, chemicals, or salt.
4. Material Compatibility
It’s essential to match the fitting material with the hydraulic fluid in use. For instance, aggressive fluids like phosphate esters require fittings with specialized seal materials and corrosion-resistant metals like stainless steel or coated aluminum.
Choosing the Right Hydraulic Swivel Fitting
Selecting the appropriate swivel fitting involves more than just matching thread sizes. Engineers must evaluate a range of factors to ensure the fitting performs optimally in the intended application.
1. Pressure Rating
Each swivel fitting is designed to withstand a maximum pressure. Always choose a fitting with a pressure rating that exceeds your system’s operating pressure to maintain safety and performance margins.
2. Rotation Speed
In high-speed rotating applications, bearings and seals must handle not only fluid pressure but also friction and heat. Consult manufacturer specs to ensure the selected fitting meets your operational speed requirements.
3. Fluid Compatibility
The hydraulic fluid type (e.g., mineral oil, water glycol, synthetic fluids) determines the choice of seals and base materials. Incompatible materials can lead to swelling, degradation, and leaks.
4. Port Type and Thread Standards
Make sure the swivel fitting’s ports match your system’s threading standard (NPT, BSP, JIC, etc.) to ensure proper fit and seal integrity.
5. Environmental Conditions
For outdoor or offshore installations, select fittings with enhanced corrosion resistance, UV protection, and temperature tolerance.
Always consult OEM guidelines and industry standards (like SAE and ISO) during the selection process to ensure full compliance and reliability.
Common Challenges and Solutions
While hydraulic swivel fittings offer numerous benefits, users may still encounter operational challenges. Understanding these issues and their solutions is key to ensuring long-term performance and reliability.
1. Leakage Issues
Leaks can occur due to worn seals, improper installation, or incompatible materials. To resolve this, always use high-quality seals rated for the fluid type and temperature range. Regular inspections and timely seal replacements are also essential to prevent leaks before they become catastrophic.
2. Misalignment
Installing a swivel fitting at an incorrect angle or under strain can prevent it from rotating properly, which puts stress on the hose or fitting body. Using support brackets and ensuring proper alignment during installation can mitigate this issue.
3. Excessive Wear
In high-speed or high-pressure systems, bearings and seals may wear faster. Choose swivel fittings specifically rated for your system’s operational parameters and follow a routine maintenance schedule to monitor internal wear.
4. Contamination
Dirt or debris entering the fitting can damage internal components. You can prevent this by using proper filtration in your hydraulic system and installing protective caps when you disconnect fittings.
Installation Best Practices
Proper installation of hydraulic swivel fittings is vital to ensuring leak-free operation and maximizing lifespan. Even a high-quality fitting can fail prematurely if not installed correctly.
1. Cleanliness First
Always clean the fitting and hose ends before installation. Contaminants can damage seals and internal components, leading to leaks and reduced performance.
2. Use Correct Torque Values
Overtightening can damage threads and seals, while under-tightening can cause leaks. Always refer to the manufacturer’s recommended torque specifications for each connection type.
3. Avoid Cross-Threading
Ensure threads are properly aligned before tightening. Cross-threading not only damages the fitting but also compromises the sealing surface, making future maintenance difficult.
4. Use Thread Sealants Wisely
For tapered threads, it is important to use an appropriate hydraulic thread sealant or PTFE tape. However, avoid excessive use, as sealant particles can enter the hydraulic system and cause contamination.
5. Check for Free Rotation
After installation, be sure to verify that the swivel fitting rotates freely under load. Otherwise, restricted movement may indicate misalignment or internal binding, which could eventually lead to premature failure.
Maintenance and Inspection Guidelines
Routine maintenance ensures that hydraulic swivel fittings continue to operate effectively and safely. Scheduled inspections help identify potential issues early, preventing costly system failures.
1. Visual Inspections
Regularly inspect the fitting for visible signs of wear, leakage, or corrosion. Pay close attention to the seal areas, bearings, and contact points for early signs of failure.
2. Lubrication
Some swivel fittings feature lubrication ports or grease fittings. Follow manufacturer guidelines to apply the appropriate lubricant at recommended intervals, which reduces friction and extends bearing life.
3. Seal Replacement
Seals are typically the first component to wear. Keep seal kits on hand and replace seals at the first sign of leakage or during scheduled maintenance shutdowns.
4. Rotation Test
Manually test the swivel motion periodically. If you notice resistance or grinding, it may be time to service or replace the unit.
5. Documentation
Maintain logs of inspections, replacements, and servicing for each swivel fitting. This helps track component life cycles and schedule preventative maintenance effectively.
When selecting hydraulic swivel fittings, choosing a reputable manufacturer is essential for quality assurance, performance reliability, and long-term support. Below are some of the top names in the industry:
1. Eaton
Eaton offers a wide range of high-performance swivel fittings suitable for mobile and industrial applications. Known for advanced engineering and durable materials, Eaton’s fittings are widely used in construction and energy sectors.
2. Parker Hannifin
Parker is a globally recognized leader in motion and control technologies. Their swivel fittings are engineered with cutting-edge sealing solutions and designed for extreme environments, including aerospace and marine applications.
3. Stucchi
Based in Italy, Stucchi specializes in hydraulic quick couplings and swivel joints. Their products are known for high precision, safety features, and reliability under extreme pressures and temperatures.
4. Ryco Hydraulics
Ryco manufactures a variety of hydraulic connectors, including swivel fittings, tailored for rugged applications. Their products often exceed industry standards, making them a trusted choice in mining and heavy-duty transport industries.
5. Taske
Taske is a trusted provider of high-quality hydraulic swivel fittings, known for durability, precision, and compliance with SAE and ISO standards. Their fittings are widely used in construction, agriculture, and heavy equipment industries, offering reliable performance under high-pressure and harsh conditions.
Innovations and Future Trends
The hydraulic swivel fittings market is evolving with new technologies aimed at improving system intelligence, efficiency, and environmental responsibility. Key trends include:
1. Smart Swivel Fittings
Equipped with sensors and telemetry, smart swivel fittings can monitor rotation speed, temperature, and pressure in real-time. This data can be integrated into predictive maintenance systems to reduce downtime and improve safety.
2. Eco-Friendly Materials
As sustainability becomes a growing concern, manufacturers are developing fittings using recyclable materials and low-impact coatings. Some are also eliminating harmful plating chemicals like hexavalent chrome.
3. Compact and Modular Designs
Modern hydraulic systems demand compact solutions. New swivel fittings feature modular architecture for easy integration, enabling quick customization without compromising strength or durability.
4. Advanced Coating Technologies
Next-generation coatings provide enhanced corrosion resistance and wear protection, especially for offshore, marine, and chemical processing environments. These coatings extend component lifespan and reduce replacement costs.
Conclusion
Hydraulic swivel fittings are a vital component in modern fluid power systems, offering flexibility, durability, and enhanced performance. From preventing hose failures to improving system reliability, these fittings play an essential role across multiple industries.
Whether you’re managing a construction fleet, overseeing an offshore rig, or designing an industrial system, choosing the right hydraulic swivel fitting—based on application, pressure rating, and material compatibility—can make a substantial difference in operational efficiency and cost savings.
By staying informed on the latest technologies, materials, and best practices, engineers and maintenance teams can ensure long-term reliability and optimal performance of their hydraulic systems.
FAQs
1. What is the typical lifespan of a hydraulic swivel fitting?
With proper maintenance and application-specific selection, a high-quality hydraulic swivel fitting can last 3 to 10 years or longer, depending on pressure, fluid type, and rotation frequency.
2. Can swivel fittings be reused after disassembly?
Some swivel fittings are reusable if disassembled carefully and inspected for wear or damage. Always replace seals and follow manufacturer guidelines before reusing a fitting.
3. Are swivel fittings suitable for high-pressure systems?
Yes, many hydraulic swivel fittings are designed to handle pressures up to and beyond 6,000 PSI. It’s crucial to verify the pressure rating on the specific fitting model.
4. What maintenance is required for optimal performance?
Routine inspection, lubrication (if applicable), and periodic seal replacement are essential. Ensure proper torque and alignment during installation to prevent premature wear.
5. How do I know if a swivel fitting is failing?
Signs of failure include fluid leaks, restricted rotation, grinding noises, or visible wear on seals and bearings. Immediate inspection and replacement are recommended to avoid system failure.