Hydraulic systems are essential in various industries, ensuring the smooth operation of heavy machinery, vehicles, and industrial equipment. But have you ever considered the consequences of using non-standard hydraulic fittings? The risks range from operational inefficiencies to catastrophic system failures.
International standards such as ISO, SAE, DIN, and JIS help regulate the quality, safety, and compatibility of hydraulic fittings. By adhering to these guidelines, businesses can ensure seamless operations, avoid costly downtime, and protect workers from hazardous failures.
This article will explore why compliance with international standards in hydraulic fittings is crucial, the key standards involved, and the potential risks of non-compliance. Let’s dive in!
Why Compliance with International Standards is Crucial
Hydraulic fittings play a pivotal role in ensuring the safe and efficient operation of hydraulic systems. Compliance with international standards is not just a formality—it’s a necessity for maintaining operational integrity. Below, we explore the key reasons why businesses must adhere to these regulations.
1. Ensuring Safety and Reliability

Hydraulic systems operate under extreme pressures, sometimes exceeding 5,000 psi (pounds per square inch) in industrial applications. A minor defect in a fitting can lead to a catastrophic failure, causing injuries, equipment damage, or even fatalities.
Standard-compliant hydraulic fittings undergo rigorous testing to ensure they can withstand high pressures, temperature variations, and environmental stress.
Real-World Example:
In 2017, a major hydraulic failure at a construction site resulted in a burst hydraulic hose due to a substandard fitting. The incident led to a worker injury and a multi-million dollar lawsuit. This could have been avoided if the company had used ISO 8434-compliant fittings.
By following standards, companies can prevent such incidents and maintain a safe working environment.
2. Improving System Efficiency
Efficiency in hydraulic systems is crucial for reducing energy consumption and ensuring smooth operations. Subpar fittings contribute to fluid leakage, pressure drops, and inconsistent performance, all of which lead to energy loss and reduced efficiency.
Key Efficiency Factors:
- Leak Prevention: Standardized fittings use high-quality seals to minimize leaks.
- Optimized Flow: Properly engineered fittings reduce turbulence in hydraulic fluid flow, improving performance.
- Temperature Resistance: Certified fittings are designed to withstand temperature variations, preventing material degradation.
Industry Insight:
A study by the Fluid Power Institute found that fluid leaks in hydraulic systems account for up to 20% of energy loss in industrial machinery. Investing in quality, compliant fittings directly impacts energy efficiency and cost savings.
3. Compatibility Across Global Markets
Hydraulic components are often sourced from different manufacturers around the world. Without standardized specifications, businesses would struggle with compatibility issues, leading to delays, additional costs, and logistical headaches.
Benefits of Standardization:
- Interchangeability: ISO, SAE, and DIN-compliant fittings are universally recognized, allowing seamless replacement across brands.
- Supply Chain Efficiency: Companies can source parts from multiple suppliers without worrying about mismatched components.
- Reduced Costs: Eliminates the need for custom-fabricated fittings, lowering production and maintenance expenses.
Example:
A manufacturing plant using ISO 12151-certified hose fittings can easily replace parts from various vendors without compatibility issues, ensuring uninterrupted operations.
4. Legal and Regulatory Compliance
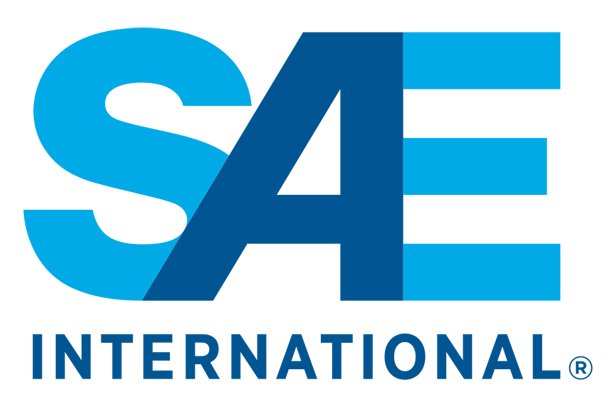
Industries such as aerospace, automotive, construction, and oil & gas have stringent regulatory requirements for hydraulic components. Failure to comply with these standards can result in fines, legal actions, and even shutdowns.
Industry-Specific Regulations:
- Aerospace: SAE J1926 mandates leak-proof hydraulic fittings for aircraft systems.
- Manufacturing: The European Union’s Machinery Directive enforces ISO and EN standards for hydraulic equipment.
- Automotive: SAE J514 sets requirements for automotive hydraulic tube fittings.
Non-compliance can not only result in financial penalties but also reputational damage, making it harder for businesses to secure contracts and partnerships.
5. Enhancing Product Longevity
Hydraulic systems are expensive investments, and ensuring their longevity is crucial for businesses looking to optimize costs. Standard-compliant fittings are made from high-grade materials such as stainless steel, brass, and reinforced polymers, offering superior durability and resistance to wear and tear.
Lifespan Benefits:
- Corrosion Resistance: ISO 8434 fittings use anti-corrosion coatings to prevent rust and degradation.
- Pressure Durability: SAE J517 hoses are designed to withstand repeated high-pressure cycles without failure.
- Reduced Maintenance Costs: Longer-lasting fittings mean fewer replacements and reduced downtime.
Case Study:
A mining company switched from non-standard hydraulic fittings to DIN 2353-compliant compression fittings and saw a 35% reduction in maintenance costs due to increased system longevity.
Key International Standards for Hydraulic Fittings
Hydraulic fittings must meet internationally recognized standards to ensure performance, compatibility, and safety. Here’s a breakdown of some key standards:
1. ISO (International Organization for Standardization) Standards
- ISO 8434 – Covers metallic tube fittings used in hydraulic systems.
- ISO 4413 – Defines general rules for hydraulic fluid power systems, including safety measures.
- ISO 12151 – Regulates hydraulic hose fittings for durability and pressure resistance.
2. SAE (Society of Automotive Engineers) Standards
- SAE J514 – Governs flare-type tube fittings for high-pressure systems.
- SAE J1926 – Ensures O-ring face seal fittings meet leak-prevention standards.
- SAE J517 – Covers performance requirements for hydraulic hoses.
3. DIN (Deutsches Institut für Normung) Standards
- DIN 2353 – Regulates compression fittings for hydraulic applications.
- DIN EN 853 – Defines performance standards for hydraulic hoses.
4. JIS (Japanese Industrial Standards)
- JIS B8363 – Covers metric hydraulic fittings used in Japanese industrial machinery.
Risks of Non-Compliance with Hydraulic Standards
Using non-compliant fittings poses several risks, including:
- Workplace Accidents: Hydraulic failures can cause severe injuries or fatalities.
- Increased Maintenance Costs: Inferior fittings require frequent replacements, increasing downtime.
- Operational Disruptions: Equipment failures due to faulty fittings can halt production lines.
- Legal Liabilities: Companies may face lawsuits and regulatory fines for non-compliance.
Real-Life Incident:
In 2019, a manufacturing plant suffered a major system failure due to a non-compliant fitting rupture, resulting in a $2 million loss in production delays and legal fines.
How to Ensure Compliance with International Standards
1. Source from Certified Manufacturers
Work with trusted suppliers who provide ISO, SAE, DIN, or JIS-certified hydraulic fittings.
2. Conduct Regular Inspections
Perform routine maintenance and inspections to detect early signs of wear or failure.
3. Train Employees on Compliance
Educate your workforce on the importance of using standardized hydraulic components.
4. Work with Industry Experts
Consult hydraulic engineers and compliance specialists to ensure adherence to global standards.
Conclusion
Compliance with international standards in hydraulic fittings isn’t just about following regulations—it’s a business necessity. It ensures safety, efficiency, compatibility, and longevity, protecting both workers and equipment.
By investing in high-quality, standard-compliant fittings, businesses can reduce risks, lower maintenance costs, and improve operational performance. Are your hydraulic systems meeting global standards? If not, now is the time to take action.
FAQs
1. Why is compliance with international standards important for hydraulic fittings?
Compliance ensures safety, efficiency, and reliability by reducing the risk of system failures, leaks, and workplace accidents. It also ensures compatibility with global suppliers and meets legal regulations.
2. What are the most common international standards for hydraulic fittings?
The key standards include ISO 8434, SAE J514, DIN 2353, and JIS B8363, each regulating different aspects of hydraulic fittings like material quality, pressure resistance, and leak prevention.
3. What happens if a company uses non-compliant hydraulic fittings?
Non-compliant fittings can lead to leaks, equipment failure, increased maintenance costs, legal penalties, and safety hazards. In extreme cases, they can cause injuries or fatalities.
4. How can I check if a hydraulic fitting meets international standards?
Always purchase from certified manufacturers, look for compliance markings (ISO, SAE, DIN, JIS), and request documentation such as certificates of conformity or test reports.
5. Do all industries need to follow the same hydraulic fitting standards?
No, different industries have specific standards. For example, SAE standards are common in automotive and aerospace, while ISO and DIN standards are widely used in industrial and construction applications.
6. How can a business ensure ongoing compliance with hydraulic fitting standards?
Regularly inspect and maintain hydraulic systems, train employees on proper fitting selection, and source components only from reputable suppliers who follow international standards.