Flow control is the heartbeat of industrial systems. It’s the key to ensuring processes run efficiently, safely, and consistently. Whether it’s a sprawling oil refinery, a water treatment facility, or a cutting-edge chemical plant, the need for precise control over the movement of liquids, gases, or even solid materials cannot be overstated.
In this article, we’ll take a deeper dive into the concept of flow control, breaking down its significance, benefits, and applications in different industries. Plus, we’ll explore the devices that make flow control possible and discuss how to overcome the common challenges it presents.
What Is Flow Control in Industrial Systems?
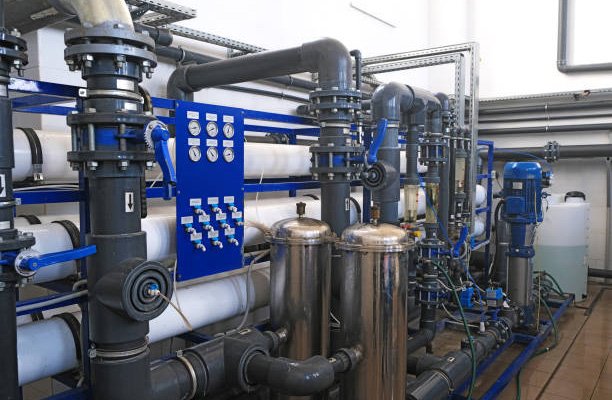
At its core, flow control refers to regulating the movement of fluids, gases, or granular materials within an industrial system. These systems are often complex, with networks of pipes, pumps, valves, and sensors working in tandem to transport materials from one point to another.
Flow control devices enable operators to adjust factors such as:
- Pressure: Keeping pressure within desired limits prevents system failures.
- Velocity: Ensures materials flow at an optimal speed to maintain efficiency.
- Direction: Prevents backflow or undesired diversion of materials.
- Volume: Controls the amount of material being transported, reducing waste and enhancing precision.
For example, in a water treatment plant, valves regulate the water pressure and flow rate to ensure proper purification. In contrast, in a chemical plant, flow meters and sensors help maintain precise ingredient ratios in production processes. Without these mechanisms, industrial systems would lack control, leading to inefficiencies, safety risks, and costly downtimes.
The Key Benefits of Flow Control
Now that we understand what flow control is, let’s dig deeper into the benefits it offers across industries:
1. Enhances Efficiency
Flow control systems ensure that industrial resources—whether it’s water, oil, or chemicals—are used in the most efficient way possible. Imagine a scenario in which excessive fluid or gas flows through a system. Not only does this lead to waste, but it also increases energy costs. By regulating flow rates, industries can cut down on unnecessary energy consumption, improve overall system performance, and ultimately save money.
Take the oil and gas sector, for instance. Here, flow control ensures that crude oil moves through pipelines at an optimal rate, reducing wear on the equipment and preventing bottlenecks. Similarly, in food manufacturing, flow control devices ensure consistent ingredient delivery, speeding up production without compromising quality.
2. Boosts Safety
Safety is a non-negotiable aspect of industrial operations. Uncontrolled flow—be it of water, gas, or chemicals—can lead to hazardous situations. High-pressure systems without proper flow control can rupture, causing leaks, spills, or even explosions.
Flow control devices, such as pressure-relief valves and automated shut-off valves, act as safety nets. For instance, in a gas refinery, these systems can detect abnormal pressure levels and immediately close off sections of the pipeline to prevent disaster. Real-time monitoring through IoT-enabled sensors also ensures that anomalies are detected and resolved quickly.
3. Improves Product Quality
Consistency is king in industries like pharmaceuticals, food production, and chemical manufacturing. A slight deviation in flow rates can disrupt production and lead to substandard products. For example, a pharmaceutical manufacturer relying on precise chemical mixing would be unable to produce consistent medicines without accurate flow control systems.
By ensuring uniform flow rates and precise ingredient mixing, flow control systems help industries maintain product quality, meet regulatory standards, and build customer trust.
4. Reduces Downtime
Unplanned downtimes can wreak havoc on industrial operations. Without proper flow control, systems can overheat, pressure can build up to dangerous levels, and components can wear out faster.
Flow control devices continuously monitor system parameters and make real-time adjustments to prevent failures. Predictive maintenance, enabled by IoT sensors and data analytics, alerts operators to potential issues before they escalate. For example, in a power plant, monitoring steam flow rates ensures turbines operate efficiently, reducing the risk of expensive breakdowns.
5. Minimizes Environmental Impact
Sustainability is a growing concern across industries. Leaks, spills, and resource wastage not only harm the environment but also attract heavy fines and damage a company’s reputation.
Flow control systems help industries adhere to environmental regulations by preventing leaks, optimizing resource use, and reducing emissions. For instance, in water treatment facilities, flow meters ensure precise water usage, minimizing waste. Similarly, in oil refineries, automated systems prevent harmful gas emissions by keeping pressure levels in check.
Industries That Depend on Flow Control
Flow control plays a pivotal role across numerous industries. Let’s examine how specific sectors benefit from it:
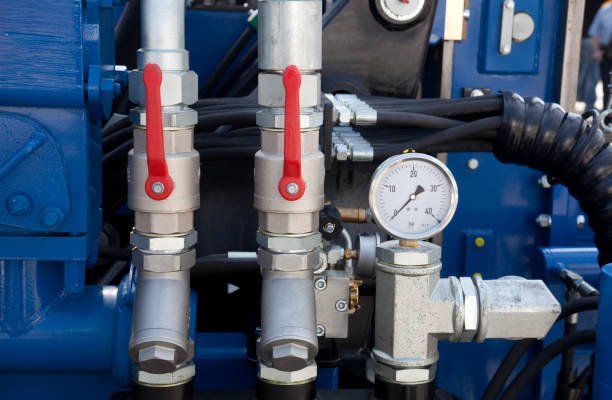
1. Oil and Gas
In the oil and gas industry, flow control ensures the efficient and safe movement of crude oil, natural gas, and refined products. Pipelines are often subject to high pressures and temperatures, making precise control essential to prevent leaks and maintain safety standards.
For example, offshore drilling operations rely on flow control devices to manage the extraction of oil from deep reservoirs. Similarly, refineries use automated valves to regulate the flow of crude oil through different processing units, ensuring optimal production rates.
2. Water and Wastewater Treatment
Flow control systems are at the heart of municipal water plants and wastewater treatment facilities. Valves, flow meters, and pumps work together to ensure clean water reaches households while wastewater is safely treated and discharged.
Take a wastewater facility, for instance. Without flow control, untreated waste could overflow into surrounding environments, causing pollution and health hazards. Flow meters help operators monitor water levels, while pumps ensure waste moves through each stage of treatment efficiently.
3. Manufacturing and Automation
In manufacturing, consistency and precision are paramount. Flow control systems regulate the flow of materials—whether it’s paint, chemicals, or gases—through production lines.
For example, in car manufacturing, precise paint flow ensures vehicles are evenly coated, reducing waste and ensuring a flawless finish. Automated flow control systems are also critical in 3D printing, where the material flow must be consistent to produce accurate designs.
4. Chemical Processing
The chemical industry involves handling volatile and reactive materials. Flow control systems help maintain safe and accurate production processes by regulating pressure, temperature, and flow rates.
For instance, in a fertilizer plant, flow control ensures that ammonia and other chemicals are mixed in the correct proportions. Even minor deviations in flow rates could lead to unsafe reactions, putting workers and equipment at risk.
5. Power Generation
From hydropower to nuclear plants, flow control is a cornerstone of power generation. Systems regulate the flow of water, steam, or gases to optimize energy production while ensuring safety.
Take a nuclear power plant, for example. Precise flow control ensures that cooling water circulates at the right rate, preventing overheating and maintaining safe reactor operations.
How to Optimize Flow Control in Industrial Systems
To maximize the benefits of flow control, industries must adopt best practices and stay ahead of technological advancements:
- Invest in Quality Equipment: Choose durable and reliable flow control devices that meet the specific demands of your industry. Poor-quality equipment often leads to inefficiencies and higher maintenance costs.
- Automate with IoT: Integrating IoT-enabled sensors and actuators allows for real-time monitoring and control. For instance, an IoT system can detect pressure drops in a pipeline and automatically activate a backup pump to maintain flow.
- Implement Predictive Maintenance: Preventive maintenance is good, but predictive maintenance is even better. Use data analytics to predict when flow control devices will need repairs or replacements.
- Train Staff: Ensure that your workforce is trained to operate and troubleshoot flow control systems effectively. This minimizes human errors and improves overall system performance.
- Analyze Data: Use data from flow meters and sensors to identify inefficiencies, optimize operations, and make informed decisions.
Conclusion
Flow control is the backbone of industrial systems, ensuring efficiency, safety, and sustainability across a wide array of industries. From regulating water distribution in treatment plants to maintaining consistent chemical ratios in manufacturing, flow control systems make industrial operations smoother, safer, and more reliable.
By leveraging advanced technology, investing in high-quality equipment, and adopting best practices, industries can harness the full potential of flow control to maximize performance and minimize risks.
FAQs
Q1: Why is flow control critical in industrial systems?
Flow control ensures efficient, safe, and consistent operations by regulating the movement of fluids and gases in industrial processes.
Q2: What are the common flow control devices?
Common devices include valves, flow meters, pumps, sensors, and actuators.
Q3: Can flow control systems be automated?
Yes, modern flow control systems often integrate with IoT and automation technologies for real-time monitoring and control.
Q4: What industries use flow control the most?
Industries like oil and gas, water treatment, manufacturing, chemical processing, and power generation heavily rely on flow control.
Q5: How does flow control improve safety?
By maintaining consistent pressure and flow rates, flow control devices prevent leaks, overflows, and other potentially hazardous situations.
Q6: What’s the difference between manual and automated flow control?
Manual flow control means someone physically adjusts valves or pumps to control flow, which is simple and low-cost but can be slow and prone to mistakes.
Automated flow control uses sensors and smart devices to adjust flow automatically in real-time. This makes it faster, more accurate, and safer, especially in industries like oil and gas or chemical plants where quick action is crucial.