In industrial manufacturing, transition joints are vital components, connecting materials or structures with varied properties. Welded transition joints, specifically, are essential for specialized applications that require a robust, stable bond. To ensure these joints meet rigorous standards, optimizing welding quality is crucial. This guide outlines essential methods and best practices to improve welding quality, making joints more durable and reliable for industrial applications.
What Are Welded Transition Joints?
Welded transition joints are connectors used to join two different materials or components, each with unique thermal, physical, or mechanical properties. They are widely used in industries like oil & gas, automotive, and heavy machinery manufacturing, where they provide seamless, strong connections that withstand high pressures and demanding environments. Ensuring the quality of these joints through optimized welding processes can greatly extend the lifespan and reliability of the connected components.
Types of Transition Joints in Welding
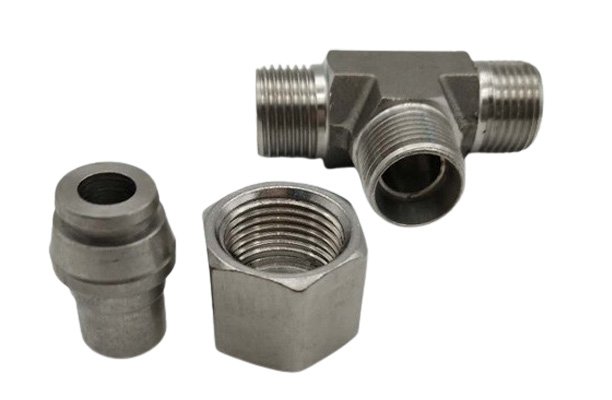
Several types of transition joints are used across industries, each suited for specific applications:
- Tube-to-Pipe Transition Joints: Common in HVAC and plumbing, these joints connect tubes to larger pipes.
- Flanged to Threaded Joints: Ideal for systems requiring disassembly, like maintenance-heavy equipment.
- Adapter Transition Joints: Used to join components of different diameters, frequently found in fluid handling systems.
Selecting the right type based on the application helps ensure optimal performance and durability.
Step-by-Step Guide to Improving Welding Quality for Transition Joints
1. Choose the Right Welding Materials
Selecting suitable welding materials is fundamental to achieving high-quality welds. Based on the transition joint’s materials and intended application, choose welding wires or rods compatible with both. Quality materials can minimize issues like cracking or porosity, ensuring that joints remain strong under stress.
2. Master Pre-Welding Preparation
Thorough preparation is crucial. Clean the joint surface to remove contaminants such as oils, dust, or rust, as these can weaken the weld. Ensure proper alignment and a smooth bonding surface, both of which contribute to a stronger, more durable weld.
3. Control Heating and Cooling Processes
Controlling heat is essential to prevent structural issues like cracking. Gradually heat the joint to avoid thermal shock and allow it to cool slowly. Rapid cooling can cause brittleness, which weakens the weld. Proper heating and cooling ensure a stable, resilient joint.
4. Optimize Welding Parameters
Adjusting parameters—voltage, current, and speed—is key to achieving stable and high-quality welds. Tailor these settings based on factors such as material type, thickness, and joint configuration to prevent common issues like spattering or incomplete fusion.
5. Use Protective Equipment for Quality and Safety
Welding protection equipment is crucial for both safety and quality. Shields, screens, and ventilation protect the joint from external factors like drafts or contaminants that can affect the weld pool’s stability. This equipment also ensures a safe environment, allowing welders to focus on precision.
6. Ensure a Clean Welding Environment
A clean environment is essential to avoid contaminating the weld. Dust, debris, and other pollutants can weaken the joint, leading to potential defects. Prioritize cleanliness before and during the weld process to maintain weld strength and integrity.
7. Apply Post-Weld Testing and Inspections
After completing the weld, conduct thorough testing to identify any hidden defects. Non-destructive testing (NDT) methods, such as ultrasonic or dye penetrant testing, are ideal for ensuring weld quality without damaging the joint. This step confirms that the joint meets industry standards for strength and durability.
8. Implement Regular Maintenance and Quality Control
Routine inspection and maintenance ensure that welded joints remain reliable over time. Periodic checks for signs of wear, corrosion, or other degradation can prevent issues before they become costly. Establishing a maintenance plan is key for high-stress applications.
9. Stay Updated on Advanced Welding Techniques
Emerging technologies such as laser or robotic welding provide higher precision, minimizing human error. Staying updated on these techniques allows manufacturers to refine welding practices, resulting in more durable and consistent joints.
Choosing the Right Weld Type for Transition Joints
The choice of weld type is critical to the durability and functionality of welded transition joints. Each weld type offers specific strengths and is suited to different applications, materials, and joint configurations. Here’s an in-depth look at common weld types used in transition joints and how to choose the best one for your application:
1. Butt Welds
- Overview: Butt welds involve joining two pieces end-to-end, aligning the surfaces in a single plane. They are one of the strongest weld types and are widely used in pipelines, structural applications, and high-pressure systems.
- Advantages: Butt welds are ideal for applications requiring high strength and durability. They allow for full penetration of the weld, creating a joint nearly as strong as the base materials.
- Applications: Common in pipe fittings, structural frameworks, and applications where maximum weld strength is essential.
- Considerations: Precise alignment is crucial for achieving a high-quality butt weld, as misalignment can compromise joint integrity. Proper edge preparation and thorough inspection (e.g., ultrasonic testing) are recommended.
2. Fillet Welds
- Overview: Fillet welds are used to join two surfaces at an angle, typically in a T-joint, corner joint, or lap joint. They do not require full penetration and are generally faster to execute than butt welds.
- Advantages: Fillet welds are versatile and effective for various structural applications. They are also easier to apply in hard-to-reach areas, offering flexibility in assembly.
- Applications: Commonly used in frameworks, machinery assembly, and applications where components are joined at angles.
- Considerations: Fillet welds may not be as strong as butt welds in high-stress applications. Ensuring consistent weld size and penetration is key for maximizing joint strength and reliability.
3. Socket Welds
- Overview: Socket welds involve inserting one pipe or fitting into a socket of another. The weld is applied around the outer edge, creating a secure, leak-proof joint.
- Advantages: These welds are particularly useful for high-pressure applications, as they offer strong, leak-resistant joints. Socket welds are easier to align than butt welds, reducing the likelihood of misalignment.
- Applications: Commonly used in piping systems, hydraulic systems, and chemical processing plants where secure, leak-proof joints are required.
- Considerations: Socket welds may introduce stress concentration, so they are best suited for smaller pipe sizes and moderate pressures. Proper heating and cooling during welding are essential to prevent cracking.
4. Lap Welds
- Overview: Lap welds are created by overlapping two components and welding along the edges. They are generally used for sheet metals and components of different thicknesses.
- Advantages: Lap welds are easy to implement and are ideal for thin materials or dissimilar thicknesses. They are also flexible in terms of weld position.
- Applications: Commonly used in automotive and fabrication industries, as well as applications requiring an overlap joint.
- Considerations: Lap welds may create stress concentration points at the edge of the weld, which can reduce joint strength. Selecting appropriate weld size and position is important to prevent fatigue in high-stress applications.
5. Seam Welds
- Overview: Seam welding is a continuous weld created by overlapping two sheets or plates, typically with a roller. This weld type forms a continuous, leak-tight seal.
- Advantages: Seam welds offer high strength and are ideal for leak-proof applications. The continuous weld provides excellent protection against leakage, making it suitable for fluid or gas containment.
- Applications: Used in tanks, pressure vessels, fuel systems, and applications requiring a long, continuous weld.
- Considerations: Seam welding requires specialized equipment, which may increase initial setup costs. Proper settings are essential to avoid burn-through, especially in thin materials.
6. Spot Welds
- Overview: Spot welding uses electric resistance to fuse small areas between two overlapping sheets. It is fast and efficient, commonly used for thin metal sheets.
- Advantages: Spot welding is cost-effective and quick, making it suitable for high-volume applications. It’s also effective for thin materials, creating a strong bond at specific points.
- Applications: Widely used in automotive manufacturing, electronic enclosures, and applications where multiple welds are required across a broad area.
- Considerations: Spot welds are not suitable for thick materials or applications requiring continuous weld strength. Their strength is limited to specific points, so they are best for applications with evenly distributed loads.
How to Choose the Right Weld Type
When selecting a weld type for transition joints, consider the following factors:
- Material Properties: Choose a weld type that accommodates the thermal expansion, melting point, and thickness of the materials being joined.
- Joint Configuration: The alignment, position, and shape of the joint impact the choice of weld. For instance, butt welds are ideal for straight alignments, while fillet welds work well for angled joints.
- Application Requirements: For high-pressure, leak-proof applications, consider options like socket or seam welds. For lightweight, less demanding structures, lap or spot welds may be more efficient.
- Load Conditions: Assess whether the joint will experience stress, bending, or shear forces. Stronger welds, like butt and fillet, are preferable for high-stress conditions.
- Production Efficiency: For large-scale manufacturing, methods like spot and seam welding can be time-saving and cost-effective, while also ensuring consistency in quality.
Tools and Equipment for Optimized Welding of Transition Joints
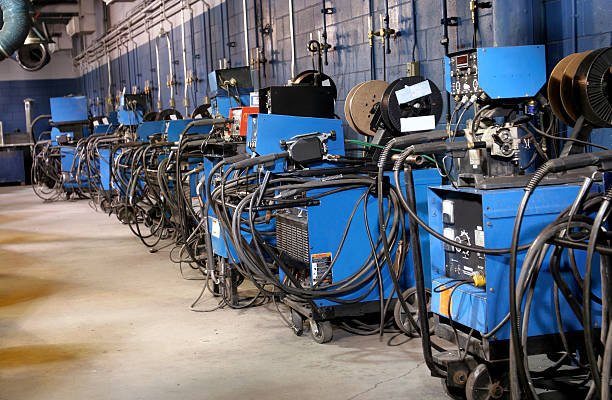
The right tools can significantly enhance welding accuracy and efficiency. Essential equipment for welding transition joints includes:
- Welding Machine: Choose one suited to the materials involved, such as MIG, TIG, or stick welding machines.
- Clamps and Jigs: These stabilize the joint, ensuring precision and minimizing movement during welding.
- Heat Shields: Protect nearby components from heat exposure and maintain weld pool stability.
- Protective Gear: Helmets, gloves, and respirators ensure safety, contributing to both quality and consistency.
By using the appropriate tools, welders can achieve a precise and strong joint while maintaining safety standards.
Common Challenges in Welding Transition Joints and Solutions
Welding transition joints presents specific challenges, including cracking, warping, and incomplete fusion. To address these:
- Material Compatibility: Choose materials compatible with both metals.
- Thermal Management: Gradually control heating and cooling to minimize stress.
- Alignment: Use jigs and tack welds to maintain alignment and prevent distortion.
Each of these practices ensures a more stable, defect-free weld.
Best Practices for Pre-Weld Joint Preparation
Effective joint preparation includes surface cleaning, precise alignment, and, if needed, applying surface treatments. Clean, contaminant-free surfaces help achieve a smooth, consistent bond, while proper alignment prevents defects and enhances weld strength.
Welding Safety Tips for Transition Joints
Proper safety measures protect both welders and the quality of the weld. Use suitable PPE (personal protective equipment), ensure good ventilation, and handle hazardous materials safely. Prioritizing safety helps welders focus on precision and reduces the risk of workplace injuries.
Material Compatibility and Its Impact on Welded Transition Joints
Different materials, such as stainless steel, aluminum, or copper alloys, require tailored techniques. For example, using materials with similar thermal expansion rates minimizes stress during welding and extends joint longevity. Ensuring compatibility improves performance and minimizes potential for joint failure.
Emerging Technologies and Techniques in Transition Joint Welding
Innovations such as robotic and laser welding offer higher precision and faster execution, reducing weld defects. These methods also enable higher consistency, which is crucial for industries that require a high level of accuracy and efficiency.
Industry Applications of Welded Transition Joints
Welded transition joints are integral across various industries:
- Oil & Gas: High-strength, pressure-resistant joints for pipelines.
- Automotive: Durable joints for lightweight structures, such as exhaust systems.
- Manufacturing: Reliable connections between different materials for equipment and machinery.
Highlighting industry applications helps readers understand the versatility and importance of transition joints in modern industry.
Conclusion
Enhancing welding quality for transition joints requires the right combination of materials, techniques, and environmental controls. By adhering to these best practices, manufacturers can produce stronger, more reliable joints that withstand the demands of industrial applications. Staying updated with advanced welding methods also helps maintain high-performance standards and operational safety.
FAQs
1. What is a welded transition joint?
It’s a connector used to join two materials with different properties, commonly used in industrial settings for its durability and strength.
2. How do I select the right welding material?
Choose materials compatible with the base metals involved and ensure they meet the application’s requirements for strength and durability.
3. Why is cooling control important after welding?
Controlled cooling prevents brittleness and cracking, ensuring a strong, stable weld.
4. What tools are essential for welding transition joints?
Tools like welding machines, clamps, protective shields, and PPE are key to achieving safe and accurate welds.
5. What testing methods ensure joint quality?
Non-destructive testing, like ultrasonic and dye penetrant testing, help identify flaws without damaging the weld, confirming it meets quality standards.
6. How often should joints be inspected?
Regular inspections, depending on usage and stress, are recommended to ensure longevity and reliability in high-stress applications.