1. Introduction to Hydraulic Hose Banjo Fittings
What is a Banjo Fitting?
Install hydraulic hose banjo fitting correctly, and you’ll ensure a secure, compact, and leak-resistant connection in your hydraulic system. Banjo fittings are specialized connectors that allow fluid to flow through a hollow bolt and a round fitting, enabling efficient fluid transfer in tight spaces. Commonly used in automotive, industrial, and agricultural applications, they are essential components for high-pressure fluid systems where space and alignment matter.
Why Use Banjo Fittings in Hydraulic Systems?
Banjo fittings are favored for their compactness and efficiency in space-constrained hydraulic assemblies. They allow hoses to pivot or change direction without requiring multiple fittings or adapters. Their low-profile design reduces the risk of hose interference and simplifies routing in complex machinery. Moreover, they help prevent over-tightening, which can damage threads or crush washers, ensuring long-term durability and performance.
2. Tools and Materials You Will Need
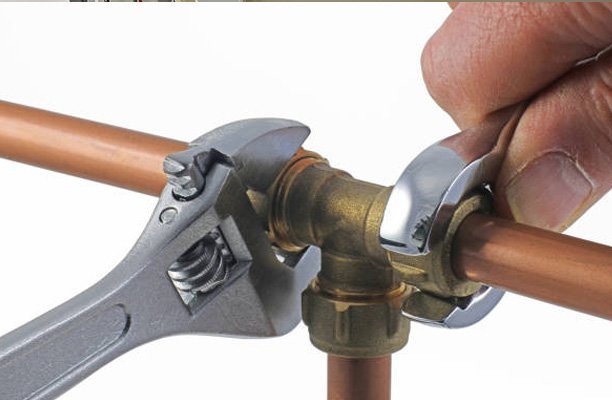
Essential Tools for Installation
Before beginning the installation, it’s essential to gather the correct tools and components. These include:
- Adjustable wrench or torque wrench
- Hydraulic hose cutter or sharp utility knife
- Clean lint-free cloths or rags
- Banjo bolt and two crush washers (usually copper or aluminum)
- Appropriate hydraulic fluid (check system specs)
- Thread locker (optional, if specified by manufacturer)
Choosing the Right Banjo Fitting and Hose
The banjo fitting must match the specifications of the hydraulic system. Key considerations include:
- Thread size and pitch of the banjo bolt
- Inner diameter of the hose
- Operating pressure and fluid compatibility
- Angle type: 0°, 45°, or 90°
Always refer to the manufacturer’s guidelines to ensure compatibility and avoid system failure due to improper fitting sizes.
3. Safety First: Preparing for Installation
Safety Gear Checklist
Working with hydraulic systems involves pressurized fluids, which can be dangerous. Personal protective equipment (PPE) should include:
- Safety goggles or face shield
- Cut-resistant gloves
- Protective overalls or coveralls
- Closed-toe work boots
Keep a first-aid kit and spill absorbent materials nearby in case of emergencies.
Depressurizing the Hydraulic System
Before installation, ensure the hydraulic system is completely depressurized to avoid injuries and fluid spray. Follow these steps:
- Turn off the hydraulic system and disconnect the power source.
- Operate the hydraulic actuator several times to relieve residual pressure.
- Slowly open the system’s bleed valve to release trapped fluid pressure.
- Drain the system if necessary and wipe down connection points with a clean rag.
Skipping this step can result in high-pressure leaks, serious injury, or equipment damage.
4. Step-by-Step Guide to Install a Banjo Fitting
Step 1: Identify the Banjo Bolt and Crush Washers
Begin by identifying the key components:
- Banjo bolt – a hollow bolt that allows fluid to pass through.
- Banjo fitting – the circular fitting with a central hole.
- Crush washers – soft metal washers (usually copper or aluminum) placed on either side of the fitting.
Ensure all components are clean and free from debris or old sealant, as contamination can lead to leaks or restricted flow.
Step 2: Attach the Banjo Fitting to the Hose
Depending on your system, the fitting may already be swaged (permanently crimped) to the hose, or it may be a reusable style. If not already assembled:
- Insert the hose into the banjo fitting barb or end connection.
- Secure using a high-pressure hydraulic crimping tool or clamps if it’s a reusable fitting.
- Make sure the connection is firm and correctly oriented for installation.
Check that there is no visible gap or play between the hose and fitting.
Step 3: Insert and Tighten the Banjo Bolt
Now assemble the connection:
- Place one crush washer on the banjo bolt.
- Insert the banjo bolt through the banjo fitting’s eye.
- Place the second crush washer on the other side of the fitting.
- Align the assembly with the threaded port of the hydraulic component.
- Hand-tighten the banjo bolt to seat the washers and fitting in place.
Ensure the fitting’s hose direction aligns with the system’s layout to prevent interference.
Step 4: Torque Specifications and Final Tightening
Using a calibrated torque wrench, tighten the banjo bolt to the manufacturer’s recommended torque. Over-tightening can crush the washers too much or strip threads, while under-tightening can lead to leaks.
Typical torque specs range from:
- 22–35 Nm (16–26 ft-lb) for small diameter fittings
- 40–60 Nm (30–45 ft-lb) for larger hydraulic lines
If no specs are provided, refer to a torque chart based on bolt size and washer material.
5. Common Mistakes to Avoid
Over-Tightening or Cross-Threading
One of the most common errors is over-tightening the banjo bolt, which can deform the crush washers and damage the mating surfaces. Similarly, cross-threading the bolt can strip the hydraulic port threads, necessitating expensive repairs. Always hand-start the bolt before torquing to ensure correct alignment.
Using Damaged or Incompatible Parts
Avoid using used or damaged crush washers, as they will not seal properly. Also, ensure that the banjo fitting, bolt, and port are made from compatible materials to prevent galvanic corrosion. Never mix metric and imperial thread systems—this can result in weak or leaking connections.
6. Testing for Leaks and Final Inspection
How to Check for Hydraulic Fluid Leaks
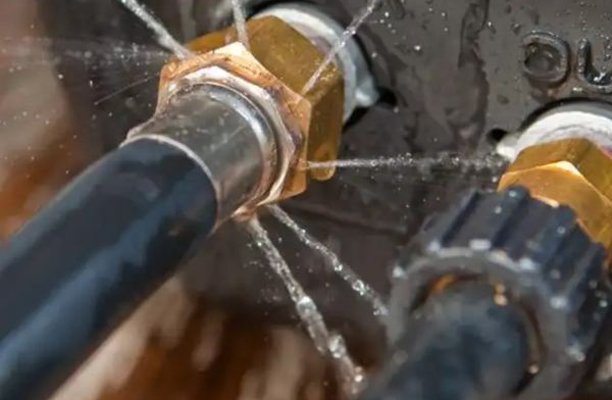
After installation, test the system for leaks before putting it into full operation:
- Slowly pressurize the hydraulic system while observing the new connection.
- Use a clean cloth to wipe around the fitting—any wetness may indicate a leak.
- Apply a leak-detection spray or soapy water if necessary (check compatibility with hydraulic fluid).
Never use your hands to check for leaks on a pressurized hydraulic line—fluid can penetrate the skin and cause serious injury.
Ensuring Proper Hose Orientation and Clearance
Finally, inspect the hose routing to ensure it isn’t kinked, twisted, or stretched. Ensure:
- A minimum bend radius is maintained.
- There’s adequate clearance from hot or moving components.
- Hose clamps or brackets are used if necessary to secure the hose in place.
Proper orientation extends hose life and maintains the integrity of your hydraulic system.
7. Maintenance Tips for Long-Term Performance
When to Re-Torque Banjo Fittings
Banjo fittings may require re-torquing after the initial installation due to crush washer compression. It is recommended to:
- Recheck torque after the first few hours of system operation.
- Inspect during regular maintenance intervals—typically every 100–250 hours depending on system usage.
Always use a torque wrench during re-tightening to avoid accidental over-torquing.
Signs of Wear or Failure
Banjo fittings can fail over time due to vibration, pressure spikes, or contamination. Look for:
- Visible fluid leakage around the fitting or hose
- Discoloration or corrosion near the bolt and washer area
- Cracked hoses or frayed reinforcements at the fitting junction
- Unusual system noises or performance drops
If any of these signs appear, promptly inspect and replace the faulty components to avoid system downtime or damage.
8. Applications and Use Cases
Automotive Braking Systems
Banjo fittings are widely used in automotive braking systems, especially in high-performance vehicles. Their compact design allows them to fit snugly against brake calipers, providing a secure and leak-resistant connection. They also help simplify routing in vehicles with limited space or complex suspension layouts.
Industrial Hydraulic Machinery
In industrial settings, banjo fittings are used in hydraulic cylinders, pumps, and control valves. Their ability to rotate and maintain compact profiles makes them ideal for robotic arms, CNC machines, and agricultural equipment. Their compatibility with high-pressure systems ensures reliable operation even in demanding conditions.
9. Troubleshooting Guide
Leakage After Installation
If you experience leakage immediately after installation:
- Ensure crush washers are new and properly seated.
- Double-check torque values against manufacturer specifications.
- Inspect the mating surfaces for burrs, dents, or contamination.
Disassemble the fitting, clean all components, and reassemble with fresh washers if needed.
Hose Slippage or Rotation
If the hose attached to the banjo fitting rotates or slips under pressure:
- Inspect the crimped end or clamp integrity (for reusable fittings).
- Ensure the correct hose diameter was used.
- Verify that the hose is not under excess tension or misalignment.
Rotation can lead to fitting fatigue and eventual failure, so resolving this early is essential.
10. Environmental Considerations
Disposal of Used Hydraulic Fluid
Hydraulic fluid is classified as a hazardous material and must be disposed of properly. To ensure environmental compliance:
- Collect used fluid in a sealable, clearly labeled container.
- Transport it to a certified recycling center or hazardous waste facility.
- Never pour hydraulic fluid down drains, into soil, or into water sources.
Check local regulations, as improper disposal can result in significant fines and environmental damage.
Eco-Friendly Banjo Fittings
Some manufacturers now offer environmentally conscious options such as:
- Recyclable aluminum fittings with lower carbon footprints
- Biodegradable crush washers and seal materials
- Fittings designed for compatibility with eco-friendly hydraulic fluids
Choosing sustainable components supports green initiatives while ensuring high-performance standards.
11. Expert Tips and Industry Recommendations
OEM vs Aftermarket Fittings
Original Equipment Manufacturer (OEM) fittings are generally designed to match specific systems and ensure exact compatibility. They typically offer:
- Higher build quality and tested reliability
- Compliance with strict industry certifications
- Longer warranties and support services
Aftermarket fittings, while often more affordable, can vary in quality. It’s crucial to purchase from reputable brands and verify specifications before installation.
Certifications and Compliance
When selecting banjo fittings, always check for compliance with relevant standards, such as:
- SAE J514 / ISO 8434 – Hydraulic fittings specifications
- RoHS compliance – Restriction of hazardous substances
- REACH regulations – Chemical safety compliance
Certifications ensure safety, compatibility, and longevity, especially in regulated industries like aerospace, agriculture, and manufacturing.
12. Cost Breakdown and Time Estimates
Average Cost of Parts
Installing a hydraulic hose banjo fitting is relatively cost-effective. On average:
- Banjo fitting: $5–$15 USD each
- Banjo bolt: $3–$10 USD
- Crush washers (set of two): $1–$5 USD
High-performance or specialized fittings can cost more, particularly for stainless steel or proprietary applications.
DIY vs Professional Installation
A skilled DIYer with the right tools can install a banjo fitting in 30 to 60 minutes. However, hiring a professional is advisable when:
- The system is critical (e.g., aircraft hydraulics or heavy equipment)
- You lack proper torque equipment
- The installation is in a confined or complex space
Professional installation costs range from $50 to $150 depending on labor rates and system complexity.
13. Best Brands and Where to Buy
Top Rated Banjo Fitting Brands
For reliability and safety, it’s essential to purchase banjo fittings from trusted manufacturers. Top-rated brands include:
- Parker Hannifin – Known for precision-engineered hydraulic components.
- Eaton Aeroquip – Offers fittings for high-performance and industrial-grade systems.
- Brembo – Renowned for automotive braking systems and premium hydraulic parts.
- Swagelok – Specializes in leak-tight fittings for critical fluid systems.
Online and Local Retailers
Banjo fittings and accessories are widely available at:
- Amazon – Offers a wide selection, including customer reviews and bundle kits.
- Grainger – Industrial-grade fittings with technical support options.
- Hydraulic supply stores – Provide expert guidance and part matching services.
- Local auto parts retailers – Ideal for automotive applications.
Always verify the part number and specs before purchasing to ensure a correct fit.
14. FAQs About Hydraulic Banjo Fittings
Can I Reuse Banjo Bolts?
Technically, you can reuse banjo bolts if they are undamaged and clean. However, crush washers should never be reused, as they deform upon installation and won’t seal effectively a second time.
Are Banjo Fittings Universal?
No. Banjo fittings vary by thread type (metric vs. imperial), bolt diameter, angle, and pressure rating. Always verify dimensions and thread compatibility with the target hydraulic system before purchase.
Conclusion
Installing a hydraulic hose banjo fitting may seem intimidating, but with the right tools, components, and attention to detail, it can be a smooth and rewarding task. This guide covers everything from safety prep to final inspection, ensuring a secure and leak-free connection.
Hydraulic systems operate under high pressure and require precision, but many maintenance and installation tasks are DIY-friendly when approached carefully. Always wear protective gear, follow torque guidelines, and prioritize safety. With patience and practice, you can save money while maintaining system performance.
FAQs
1. What type of hydraulic fluid should I use with banjo fittings?
It depends on your system. Most banjo fittings are compatible with mineral-based fluids, synthetic blends, or biodegradable oils. Always check the fitting material and system compatibility before use.
2. Do banjo fittings require sealant or tape?
No. Banjo fittings rely on crush washers for sealing. Applying thread tape or sealant can interfere with sealing surfaces and should be avoided unless specified by the manufacturer.
3. How do I know if my banjo fitting is leaking internally?
Look for a gradual loss of hydraulic pressure, fluid seepage around the joint, or unusual system behavior. An internal leak may not be immediately visible, so pressure tests can help diagnose the issue.
4. Can I use banjo fittings for air or gas applications?
Banjo fittings are primarily designed for fluid systems. For air or gas, use fittings specifically rated for those applications to avoid safety hazards or poor sealing performance.
5. How often should hydraulic banjo fittings be inspected?
Inspect fittings during every scheduled maintenance cycle or after 100–250 operating hours. High-vibration systems may require more frequent checks to prevent early failure.