Hydraulic systems rely on fittings that ensure leak-proof and durable connections. In automotive applications, such as brake lines and fuel systems, choosing the right fitting is crucial. Two commonly used fittings are inverted flares and double flares. Each has unique characteristics that make it ideal for specific systems.
This guide explains:
- What inverted flares and double flares are
- The differences between them
- How they compare to other flaring methods
- Tips for installation, safety, and troubleshooting
By the end, you’ll be equipped to select the best fitting for your vehicle or project.
What is an Inverted Flare?
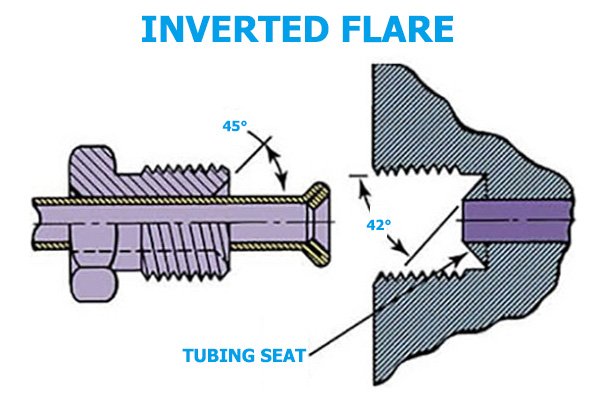
Inverted flare fittings are used in critical hydraulic systems, including:
- Brake lines
- Power steering
- Fuel systems
- Transmission cooler lines
The inverted flare technique folds the tubing inward before flaring it outward, creating a tight, leak-resistant seal. These fittings are durable and work well in systems that face frequent vibration or stress.
Key Benefits:
- Cost-Effective: Inverted flares are affordable and reusable.
- Vibration Resistance: Great for vehicles, as they hold up against movement.
- Durability: The threads and seats are internal, protecting them from corrosion.
What is a Double Flare?
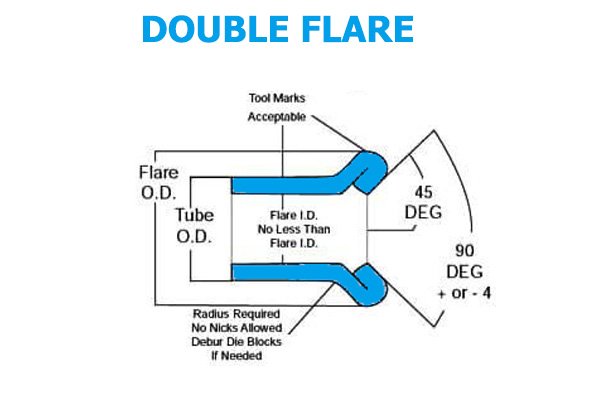
A double flare is a specialized fitting where the tube is folded over itself before being flared outward. This double layer provides extra strength, making it a popular choice in high-pressure systems such as brake lines in domestic cars and trucks.
Key Benefits:
- Tight Seal: The 45-degree flare creates a strong, leak-proof connection.
- Extra Strength: The double layer ensures durability in high-pressure systems.
- Wear Protection: Perfect for systems where fittings are often adjusted, reducing wear over time.
Inverted Flare vs Double Flare: What’s the Difference?
Here are the key differences between these two types of flares:
Feature | Inverted Flare | Double Flare |
---|---|---|
How It’s Made | Tubing is folded once and flared outward | Tubing is folded twice before being flared |
Uses | Brake lines, power steering, fuel systems | Brake lines in domestic vehicles, high-pressure systems |
Durability | Handles vibration well | Extra durable for frequent adjustments |
Cost | Easier and cheaper to make | More complex, but longer-lasting |
Both types are effective at creating strong seals, but double flares provide better protection for high-pressure systems and frequent use, while inverted flares offer a cost-effective solution for standard applications.
When to Use an Inverted Flare
Use inverted flare fittings when you need a low-cost solution that will stay strong over time. They are perfect for systems like:
- Brakes
- Power steering
- Fuel lines
These fittings hold up well against vibration and are protected from rust, making them last longer in rough environments.
When to Use a Double Flare
Double flares are best for high-pressure systems, especially when the fittings need to be tightened or adjusted often. This makes them ideal for brake systems in domestic cars and trucks.
Comparison with Other Flaring Method
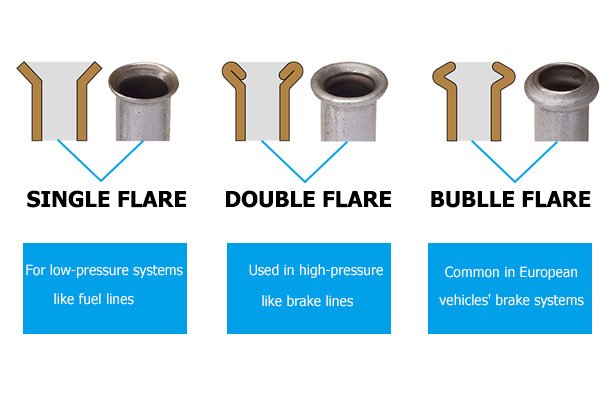
Single Flare
A single flare is a simpler fitting option where the tubing is only flared once outward. While easier and quicker to make, single flares are less durable compared to double and inverted flares. They are not recommended for high-pressure systems like brake lines due to the risk of cracking over time. They may be suitable for low-pressure applications where the connection isn’t subjected to constant stress or vibration.
Inverted Flare vs Bubble Flare
Bubble flares are commonly used in European vehicles. Instead of folding the tubing over or flaring it outward, the tube is shaped into a bubble before being connected. The bubble flare provides a moderate level of protection but doesn’t offer the same durability or pressure-handling capacity as double flares. It’s more specialized and primarily found in systems with lower pressure requirements, such as anti-lock brake systems (ABS) in European cars.
Materials Used for Tubing and Fittings
Flaring success also depends on the material of the tubing:
- Copper Tubing: Often used in residential and low-pressure applications due to its softness and ease of flaring. However, copper is not suitable for high-pressure automotive systems.
- Steel Tubing: Common in automotive brake lines due to its strength and durability. It handles pressure well but can be prone to rust without proper coatings.
- Stainless Steel Tubing: Offers high resistance to corrosion and is widely used in marine and aerospace applications, where long-term durability and resistance to environmental factors are key.
- Aluminum Tubing: Lightweight and corrosion-resistant but less common in high-pressure automotive applications. It is more suited to air conditioning or refrigeration systems.
Common Applications of Inverted Flare and Double Flare in Different Industries
While inverted and double flares are most often associated with automotive systems, they also have applications in other industries:
- HVAC Systems: Inverted and double flares are used in air conditioning and heating systems to create tight seals that can withstand temperature changes and pressure fluctuations.
- Aerospace Industry: Double flares are essential in hydraulic and fuel systems of aircraft due to their ability to handle extreme pressure and vibration.
- Construction Equipment: Hydraulic machinery, such as excavators, rely on double flares to ensure leak-free operation under heavy loads and frequent use.
Detailed Tool Usage
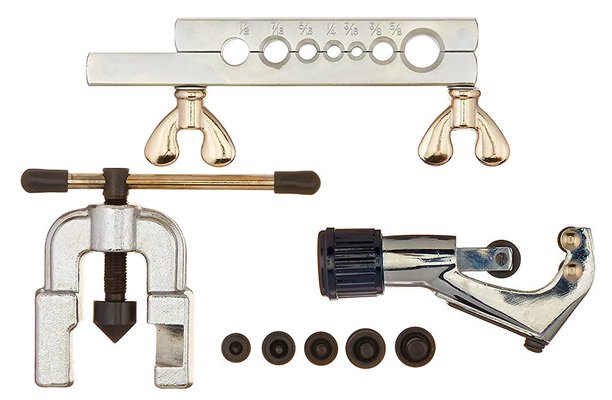
Creating a reliable flare requires the right tools and techniques. Here’s how you can make both inverted and double flares step by step.
Inverted Flare Tools and Process:
- Tube Cutter: Use a tube cutter to cut the tubing cleanly. Make sure the cut is smooth to avoid uneven flaring.
- Deburring Tool: Use a deburring tool to clean up the edges of the cut tubing. This step ensures that the tubing will seat properly in the fitting.
- Flaring Tool Kit: Insert the tubing into the flaring tool. Use the 45-degree cone to fold and flare the tubing outward.
Double Flare Tools and Process:
- Tube Cutter: Cut the tubing cleanly with a tube cutter.
- Deburring Tool: Clean the edges using a deburring tool to remove any sharp bits.
- Double Flare Kit: Insert the tubing into the double flare tool. First, fold the tubing inward to create the double layer, then use the 45-degree cone to flare it outward.
Common Problems and Solutions
Here are some common issues that occur with both inverted and double flares, along with troubleshooting tips:
- Leaking Connections: If the connection leaks, it could be due to improper flaring or debris in the flare. Check for any irregularities in the flare and clean the tubing.
- Cracking: Over-tightening can cause cracks in the flare. Make sure you follow manufacturer recommendations for tightening force.
- Corrosion: Exposure to harsh environments can lead to rust or corrosion, especially with steel tubing. Regularly inspect and replace fittings as necessary.
Importance of Flaring for Safety
In high-pressure systems like brake lines, the integrity of flaring is crucial for safety. A failed flare could lead to catastrophic system failure, which is especially dangerous in automotive or aerospace applications. Ensuring that the flare is done correctly not only enhances performance but also ensures the safety of the vehicle or system.
Compatibility with Fluids and Pressures
When choosing between inverted and double flares, consider the type of fluid being used:
- Brake Fluid: Both types of flares work well with brake fluid, though double flares are better suited for systems that face constant pressure changes and adjustments.
- Hydraulic Oil: In systems that use hydraulic oil under pressure, both flares perform well, though double flares may be more durable in high-pressure settings.
Pressure ratings for inverted and double flares are similar, but double flares offer better longevity and resistance to wear, especially in dynamic systems.
Conclusion
Choosing between inverted and double flare fittings depends on your system’s needs. Inverted flares are ideal for standard hydraulic systems that need reliable, vibration-resistant connections at a lower cost. On the other hand, double flares are perfect for high-pressure systems that require frequent adjustments, providing added durability and long-term reliability.
Whether you’re working on automotive brake lines, fuel systems, or other hydraulic applications, understanding these differences will help ensure that you select the best fitting for your project.
FAQs
1. What are inverted flare fittings used for?
Inverted flare fittings are primarily used in automotive systems, such as brake lines, power steering, and fuel lines. They provide reliable, leak-proof connections with good vibration resistance.
2. Can you use a double flare on fuel lines?
Yes, double flares are suitable for fuel lines, especially in high-pressure environments. They offer extra protection against wear and provide a more durable connection.
3. Is there a difference in pressure capacity?
There’s no significant difference in pressure rating between inverted and double flares. Both can handle high pressure, but double flares tend to last longer in systems that experience frequent adjustments.
4. Why are double flares best for brakes?
Double flares offer better resistance to wear, especially in brake systems where the fittings may be tightened or adjusted frequently. The double layer of tubing ensures a more secure, long-lasting seal.
5. Can you reuse inverted flare fittings?
Yes. Inverted flare fittings can be reused because their internal threads and seats are protected from corrosion and damage, which helps extend their life.