The ISO 8434-2 standard defines the specifications for 37° flared connectors, a vital component in modern hydraulic systems. These connectors ensure secure, leak-free connections under high pressure, making them critical for various industries such as automotive, construction, and manufacturing.
What is ISO 8434-2?
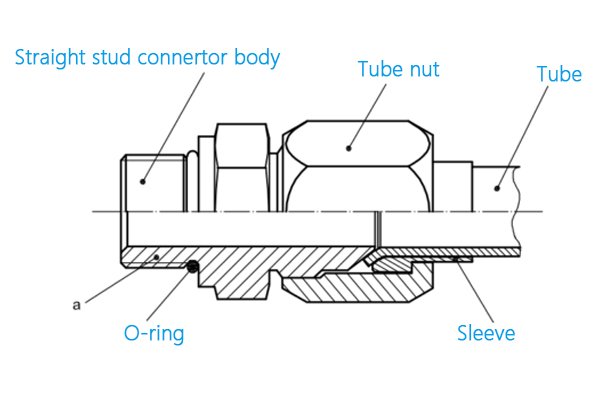
ISO 8434-2 is an international standard that governs the design and manufacturing of 37° flared hydraulic connectors. These connectors, with a 37° flare angle, offer a secure fit that minimizes leaks, withstands high-pressure environments, and ensures compatibility with global systems. The standard aligns with ANSI/SAE J514, which means it facilitates the use of these connectors in both metric and inch systems, enhancing global interoperability.
The purpose of ISO 8434-2 is to ensure that the 37° flared connectors meet rigorous quality standards, making them suitable for demanding applications. Compliance with this standard ensures that manufacturers and users benefit from components that offer safety, durability, and efficiency.
Key Specifications of ISO 8434-2: 37° Flared Connectors
ISO 8434-2 specifies various aspects of 37° flared connectors to ensure they meet quality and safety standards. Here are the main specifications covered:
1. Flare Angle
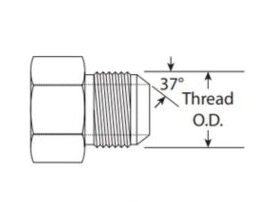
- 37° Angle: The standard specifies a 37° flare angle, which indicates the angle at which the manufacturer flares the tube or pipe. This angle is particularly effective for creating a robust seal and is compatible with high-pressure applications.
2. Dimensions and Sizes
- ISO 8434-2 specifies exact measurements for different connector sizes, allowing for consistency across manufacturers and ensuring users can interchange fittings.
- Common sizes range from 1/8 inch to 2 inches in tube outer diameter, though larger and smaller sizes may also be available depending on specific requirements.
3. Material Requirements
ISO 8434-2 specifies several materials to ensure longevity and reliability in diverse environments:
- Carbon Steel: Excellent strength for most industrial applications, resistant to wear and stress.
- Stainless Steel: High resistance to corrosion, perfect for harsh or corrosive environments.
- Copper Alloys: Suitable for less demanding conditions, providing a balance of durability and cost.
The material choice impacts the performance, making it essential for companies to choose connectors that align with their operational needs.
4. Pressure Ratings
- ISO 8434-2 specifies pressure ratings based on the material and size of the connector. For instance, stainless steel connectors may withstand higher pressures than brass ones. The typical pressure range for these fittings is up to 10,000 psi, depending on the application and material.
5. Testing Standards
- Burst Testing and Leakage Tests: The standard includes rigorous testing requirements to ensure that the connectors can hold up under real-world conditions. This includes burst testing to check the maximum pressure the fitting can handle and leakage tests to ensure a reliable seal.
6. Thread Types
- ISO 8434-2 supports UNF (Unified Fine Thread) and NPT (National Pipe Thread) standards, among others. The use of standardized threads allows for easier assembly and disassembly while maintaining a tight seal.
7. Temperature Range
- ISO 8434-2 specifies that 37° flared connectors are designed to operate in extreme temperatures, typically ranging from -40°C to 120°C or even higher, depending on the material.
Advantages of 37° Flared Connectors (ISO 8434-2 Compliant)
Choosing 37° flared connectors that comply with ISO 8434-2 offers several advantages, making them a preferred choice in many industries.
- High Pressure Tolerance: The 37° flared design withstands high pressures, making these connectors ideal for hydraulic applications.
- Leak Prevention: The metal-to-metal sealing reduces the risk of fluid leakage, even under high-pressure scenarios, enhancing system reliability.
- Interchangeability: Since ISO 8434-2 standardizes dimensions, users can interchange these connectors across different manufacturers, simplifying maintenance and repairs.
- Corrosion Resistance: The material requirements in ISO 8434-2 ensure that these connectors are resistant to corrosion, especially when made from stainless steel or brass, thereby extending their lifespan.
- Ease of Assembly: The standardization of thread types and sizes makes it easier to assemble and disassemble these connectors, reducing downtime and labor costs.
Applications of ISO 8434-2 37° Flared Connectors
Various industries widely use 37° flared connectors due to their versatility and performance.
- Automotive Industry: Used in hydraulic brake systems and fuel lines for ensuring leak-free, high-pressure connections.
- Construction Equipment: Essential for maintaining reliability in heavy machinery that operates under extreme pressure and environmental conditions.
- Aerospace and Aviation: Fuel and hydraulic systems frequently employ these connectors, where reliability and precision are critical.
- Manufacturing & Industrial Plants: High-pressure hydraulic systems in factories often rely on 37° flared connectors for smooth operations and to prevent costly leaks or equipment failures.
Comparison to Other Standards
Manufacturers often compare ISO 8434-2, which governs 37° flared connectors, to ANSI/SAE J514 because both standards cover similar products. However, many prefer ISO 8434-2 for international use due to its broader global recognition. Understanding these distinctions can help businesses choose the most appropriate standard for their needs.
Installation Tips for 37° Flared Connectors
Proper installation is essential to ensure the effectiveness of 37° flared connectors. Here are some tips:
- Inspect the Flare: Make sure the flare on the tube or pipe is smooth and free of any cracks or defects. A poorly made flare can lead to leaks.
- Use a Compatible Thread Sealant: Use a compatible thread sealant to further ensure a tight connection when recommended. However, check compatibility to avoid chemical reactions that could damage the material.
- Torque Specifications: Follow the manufacturer’s torque specifications during assembly. Over-tightening can damage the connector, while under-tightening may lead to leakage.
- Check Alignment: Misalignment can create stress points and lead to premature failure. Ensure correct alignment of the connectors before tightening.
- Regular Maintenance: Over time, fittings may wear or loosen. Routine inspections can help prevent issues and extend the life of the connectors.
Common Misconceptions About 37° Flared Connectors
Some common misconceptions could lead to issues if not properly addressed:
- “All 37° flared connectors are the same”: Not all connectors are created equal. ISO 8434-2 ensures standardization, but some manufacturers may offer lower-quality fittings. Always look for ISO certification.
- “Only metal-to-metal seals are needed for leak prevention”: Metal-to-metal seals reduce leakage, but using additional measures like thread sealant can enhance connection integrity.
- “Flared connectors don’t need maintenance”: Regular checks are essential, especially in high-vibration environments. A well-maintained connector lasts longer and ensures better performance.
Conclusion
Anyone involved in hydraulic, pneumatic, or fluid power systems must understand ISO 8434-2 standards for 37° flared connectors. These connectors offer a high-pressure, leak-resistant solution that’s both versatile and reliable, thanks to the standardization and material requirements outlined by ISO. By choosing ISO-compliant connectors, you can ensure better compatibility, reduce leakage risks, and ultimately boost the safety and longevity of your system.
Investing in ISO 8434-2 compliant 37° flared connectors not only enhances your system’s performance but also ensures you’re adhering to globally recognized safety and quality standards. So, the next time you’re sourcing connectors, make sure they meet the ISO 8434-2 requirements—your system (and your peace of mind) will thank you!
FAQs
1. What’s the importance of the 37° flare angle in these connectors?
The 37° flare angle creates a tight metal-to-metal seal, which helps prevent leaks in high-pressure systems.
2. Can I mix ISO 8434-2 connectors with non-ISO fittings?
It’s not recommended, as non-ISO fittings may not match in terms of dimensions and quality, potentially causing issues.
3. What materials are typically used for these connectors?
ISO 8434-2 connectors are commonly made from stainless steel, carbon steel, or brass for durability and corrosion resistance.
4. How often should these connectors be checked?
Annual inspections are recommended, though high-pressure or high-vibration systems may require more frequent checks.
5. Are 37° flared connectors suitable for gas systems?
Yes, they work for both hydraulic and pneumatic applications, minimizing leakage in gas systems.
6. What’s the max pressure rating for these connectors?
Typically up to 10,000 psi, depending on the material and size. Always verify with the manufacturer.