When it comes to maintaining machinery, knowing how to remove a grease gun from fittings is essential. This process ensures that you can efficiently lubricate your equipment and troubleshoot any issues that may arise during maintenance. Properly detaching a grease gun from fittings not only saves time but also helps extend the life of your tools.
What is a Grease Gun?
A grease gun is a manual or powered tool used to apply lubricant to mechanical components, ensuring they operate smoothly and efficiently. By delivering a precise amount of grease to specific locations, grease guns play a crucial role in maintaining machinery, vehicles, and various equipment. Their design allows for easy application, making them indispensable in workshops and garages.
Components of a Grease Gun
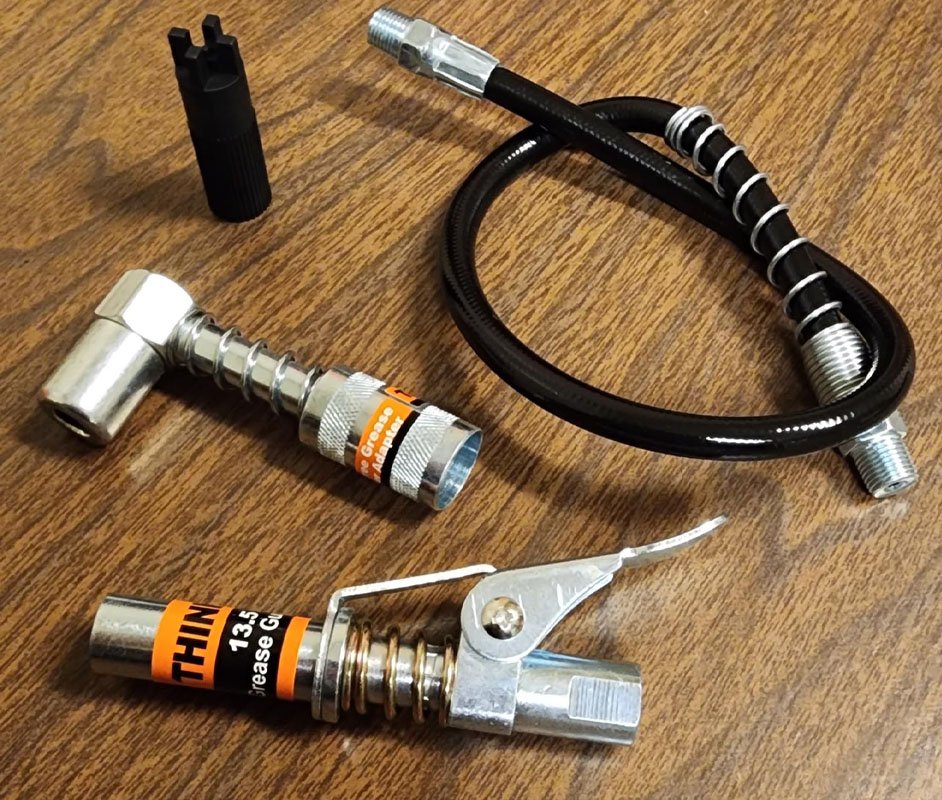
A typical grease gun consists of several key components:
- Barrel: The main body where the grease is stored.
- Plunger: A piston-like mechanism that dispenses grease when pushed.
- Nozzle: The end part that connects to the grease fitting.
- Trigger or Lever: Used to control the flow of grease.
Understanding these components helps users operate grease guns effectively.
How Grease Guns Work
Grease guns operate on a simple principle: as the plunger is pushed, grease is forced out through the nozzle and into the fitting. The pressure created by the plunger allows the grease to flow, making it easy to fill bearings and other components. Different types of grease guns utilize various mechanisms (manual, pneumatic, or electric) to achieve this task, but the core function remains the same.
Types of Grease Guns
Grease guns come in several types, each designed for specific applications:
Manual Grease Guns
Manual grease guns require physical effort to dispense grease. They are versatile and cost-effective, making them popular for small-scale maintenance tasks.
Pneumatic Grease Guns
Pneumatic grease guns use compressed air to dispense grease, making them ideal for high-volume applications. They provide consistent pressure and can speed up the lubrication process significantly.
Electric Grease Guns
Electric grease guns are powered by batteries or electricity. They offer convenience and ease of use, particularly in hard-to-reach areas. Their automatic dispensing capability minimizes effort and ensures a precise application.
Cordless vs. Corded Grease Guns
Cordless grease guns offer portability and ease of use without the hassle of cords. In contrast, corded models provide continuous power but limit mobility. The choice between the two often depends on the specific needs of the user.
Types of Grease Fittings
Grease fittings, also known as Zerk fittings, are small metal connectors that allow grease guns to inject lubricant into machinery. Different types of grease fittings include:
Zerk Fittings
Zerk fittings are the most common type, designed to accept grease from a grease gun. They typically feature a ball check valve that prevents grease from leaking out.
Standard vs. Metric Fittings
Grease fittings come in both standard and metric sizes. Understanding the difference is essential when selecting the appropriate grease gun for your equipment.
Flush Fittings
Flush fittings are designed to be installed flush with the surface of the machinery. This design prevents damage from protruding fittings and is often used in tight spaces.
Angle Fittings
Angle fittings allow for lubrication at awkward angles, making them useful for hard-to-reach areas. Their design provides flexibility in dispensing grease.
Push-to-Close Fittings
These fittings feature a mechanism that closes automatically when the grease gun is removed, preventing leaks and ensuring a clean connection.
Step-by-Step: How to Remove a Grease Gun from Fittings
Removing a grease gun from fittings can be straightforward if done correctly. Here’s a step-by-step guide:
- Inspect the Connection: Before removal, check both the grease gun and fitting for any visible damage. This will help prevent further issues during removal.
- Ensure Proper Alignment: Make sure the nozzle of the grease gun is properly aligned with the fitting. Misalignment can lead to cross-threading.
- Apply Gentle Pulling: Start by gently pulling the grease gun straight off the fitting. Avoid any abrupt movements that could cause damage.
- Use a Twisting Motion: If the grease gun does not come off easily, try twisting it slightly while pulling. This can help break any seal formed by hardened grease.
- Implement a Rocking Motion: Another effective method is to rock the grease gun back and forth as you pull. This can help release stubborn connections.
- Apply Heat if Necessary: If the gun is still stuck, gently apply heat using a heat gun or hairdryer. This can soften the grease and make removal easier.
- Clean the Fitting: After removing the grease gun, wipe away any excess grease from the fitting. Keeping fittings clean prevents buildup and makes future connections easier.
Maintenance of Grease Guns and Fittings
Regular maintenance of both grease guns and fittings is crucial for optimal performance. Here are some tips:
- Clean the Gun After Use: Wipe the nozzle and any grease residue to prevent clogs.
- Inspect for Damage: Regularly check the gun and fittings for wear and replace any damaged components.
- Lubricate Fittings: Apply a compatible lubricant to fittings to ensure smoother connections and removals.
Choosing the Right Grease Gun and Fittings
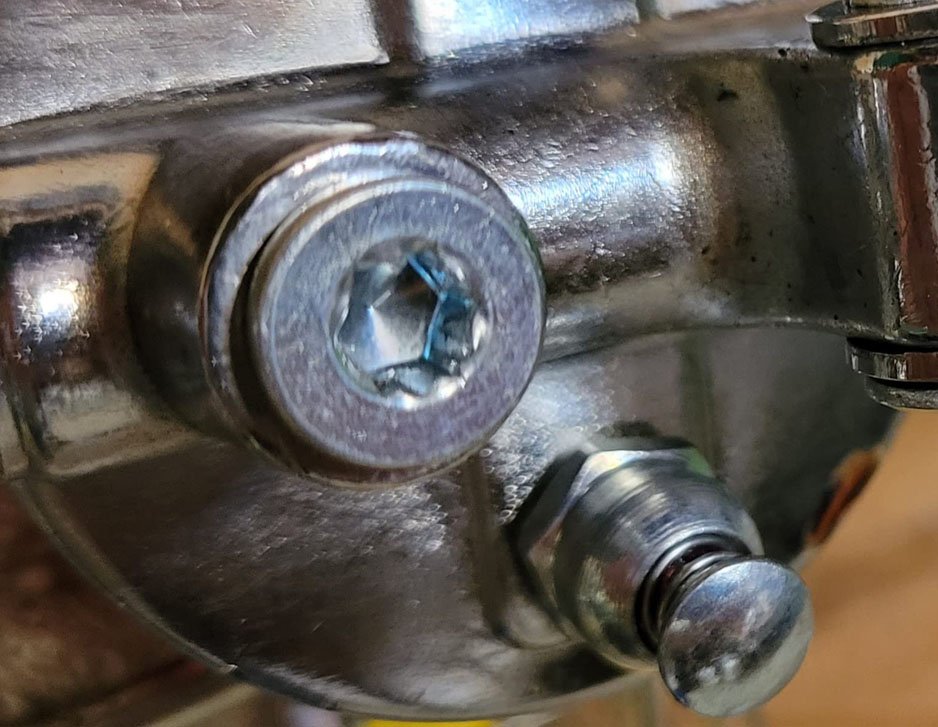
Selecting the appropriate grease gun and fittings depends on various factors, including the type of machinery, the volume of grease needed, and accessibility. Consider the following when making your choice:
- Application Needs: Assess whether you need a manual, pneumatic, or electric model based on your workload.
- Compatibility: Ensure that the fittings match your equipment specifications.
- Budget: Consider the cost of the grease gun and fittings in relation to their intended use.
Common Problems and Solutions
While grease guns are essential tools for lubrication, users may encounter several common issues. Understanding these problems and how to troubleshoot them can significantly enhance performance and extend the life of your equipment. Here are some common problems, their causes, and effective solutions:
Sticking Connection
Symptoms: The grease gun does not easily detach from the fitting.
Causes:
- Hardened Grease: Over time, grease can harden around the fitting, creating a bond that makes removal difficult.
- Misalignment: If the nozzle is not properly aligned with the fitting, it can cause cross-threading, leading to a stuck connection.
Solutions:
- Twist and Pull: Gently twist the grease gun while pulling it straight off. This can help break the seal created by hardened grease.
- Heat Application: Use a heat gun or hairdryer to warm the fitting slightly. This can soften the grease, making it easier to detach.
- Lubrication: Apply a small amount of penetrating oil around the fitting to loosen any hardened grease. Allow it to sit for a few minutes before attempting to remove the gun again.
Excess Grease
Symptoms: Grease spills out of the fitting during or after application.
Causes:
- Overfilling: Applying too much grease can overwhelm the fitting, causing excess to escape.
- Faulty Fitting: A damaged or worn fitting may not seal properly, leading to leaks.
Solutions:
- Monitor Grease Application: Use the grease gun in short bursts and observe how much grease is being dispensed. Adjust accordingly to avoid overfilling.
- Check the Fitting: Inspect the fitting for any signs of wear or damage. If it’s faulty, replace it to ensure a proper seal.
- Wipe Excess Grease: Clean the fitting area after application to remove any leftover grease and prevent contamination.
Leaks from the Grease Gun
Symptoms: Grease leaks from the gun itself, often around the nozzle or connection points.
Causes:
- Worn Seals: The seals within the grease gun may wear out over time, causing grease to leak.
- Improper Assembly: If the gun was not assembled correctly, it may not function properly, leading to leaks.
Solutions:
- Inspect Seals: Regularly check the seals for wear and replace them if they appear cracked or damaged.
- Reassemble Properly: If you suspect improper assembly, disassemble the grease gun and reassemble it carefully, following the manufacturer’s instructions.
- Use Compatible Grease: Ensure that you’re using the correct type of grease for your gun, as incompatible grease can cause internal issues leading to leaks.
Air Bubbles or Loss of Pressure
Symptoms: The grease gun does not dispense grease properly, or you hear air hissing when attempting to use it.
Causes:
- Air in the System: Air bubbles can form in the grease chamber, preventing proper grease flow.
- Clogged Nozzle: A clogged nozzle can hinder grease flow, making it seem like there is a loss of pressure.
Solutions:
- Bleed the Grease Gun: To remove air bubbles, hold the grease gun upright and pull the trigger until grease begins to flow without air. This may require a few attempts.
- Clear Clogs: Inspect the nozzle for clogs and clean it with a wire or compressed air. If the nozzle is removable, consider soaking it in a cleaning solution to dissolve any built-up grease.
Difficulty Priming the Grease Gun
Symptoms: The grease gun does not start dispensing grease even after several attempts.
Causes:
- Empty Cartridge: The grease cartridge may be empty or improperly installed.
- Faulty Plunger: The plunger mechanism might be stuck or damaged, preventing grease from being dispensed.
Solutions:
- Check the Cartridge: Ensure that the grease cartridge is full and properly seated in the gun. Replace it if necessary.
- Inspect the Plunger: Remove the barrel and check the plunger for any signs of damage or debris. Clean or replace it as needed to ensure smooth operation.
- Lubricate Moving Parts: Apply a small amount of oil to the moving parts of the grease gun to ensure they operate smoothly.
Conclusion
Understanding grease guns and fittings is essential for effective maintenance of machinery. By knowing their types, functionalities, and proper usage techniques, users can ensure their equipment operates efficiently and has a prolonged lifespan. Regular maintenance and proper handling will help avoid common issues, making the lubrication process smooth and effective.
FAQs
What is the purpose of a grease gun?
A grease gun is used to apply lubricant to mechanical components, ensuring they operate smoothly. It delivers a precise amount of grease to specific locations, preventing friction and wear on moving parts.
How do I know when to replace the grease fitting?
You should replace a grease fitting if you notice any signs of wear, such as cracks, leaks, or difficulty in securing a grease connection. Regular inspections can help identify these issues before they lead to problems.
Can I use any type of grease with my grease gun?
No, it’s important to use the type of grease recommended by the manufacturer of your grease gun and equipment. Using incompatible grease can lead to clogs or damage to the grease gun and machinery.
Why is my grease gun leaking?
Leaks can occur due to worn seals, improper assembly, or using the wrong type of grease. Regularly inspecting seals and ensuring correct assembly can help prevent leaks.
What should I do if my grease gun doesn’t dispense with grease?
If your grease gun won’t dispense grease, check for air bubbles in the system, an empty cartridge, or a clogged nozzle. Bleeding the system or clearing clogs usually resolves this issue.
How can I maintain my grease gun for optimal performance?
To maintain your grease gun, clean it after each use, check seals for wear, and ensure the correct type of grease is used. Regularly inspect and replace any damaged components to keep the gun in good working order.