Hydraulic hoses are essential components used across a wide range of industries, providing the necessary flexibility to transfer fluids under pressure. Whether in construction, agriculture, or manufacturing, choosing the right hydraulic hose is crucial to ensure system efficiency, safety, and longevity. In this guide, we’ll walk you through the key factors to consider when selecting a hydraulic hose, helping you make an informed decision.
Understanding Hydraulic Hoses
A hydraulic hose is a flexible tube used to carry pressurized hydraulic fluid in various machinery systems. These hoses are designed to withstand extreme pressures and temperatures, enabling safe and efficient fluid transfer.
What is a Hydraulic Hose?
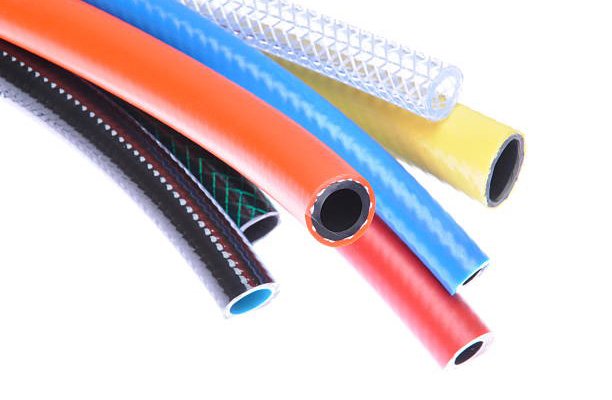
Hydraulic hoses are typically made from multiple layers of rubber, thermoplastic, or steel wire to ensure durability and flexibility. They come in various sizes, materials, and pressure ratings to accommodate different industrial applications. A hydraulic hose transfers hydraulic fluid from one part of the system to another, providing the necessary power for machines and vehicles to operate.
Common Applications of Hydraulic Hoses
Hydraulic hoses are used in many industries, including:
- Construction: For equipment like excavators, cranes, and loaders.
- Agriculture: In tractors, harvesters, and irrigation systems.
- Manufacturing: In automation and factory machinery.
- Automotive: In cars, trucks, and heavy-duty vehicles.
Key Factors to Consider When Choosing a Hydraulic Hose
Pressure Rating
The pressure rating of a hydraulic hose is one of the most critical factors to consider when making your selection. The hose must be able to withstand the working pressure of the system without bursting or causing leaks. There are two important pressure ratings to keep in mind:
- Working Pressure: The continuous pressure the hose can handle during operation.
- Burst Pressure: The maximum pressure at which the hose can fail. It’s typically four times higher than the working pressure.
To ensure optimal performance, select a hose with a pressure rating that exceeds the maximum pressure your system will operate at.
Temperature Range
The temperature at which the hydraulic system operates can significantly affect the performance of your hydraulic hose. Most hydraulic hoses are designed to function within a specific temperature range, typically from -40°F to 250°F (-40°C to 120°C). However, some specialized hoses can handle extreme temperatures, whether very hot or cold.
For high-temperature applications, look for hoses made of materials that can withstand heat without losing their strength, such as steel-braided or thermoplastic hoses. Similarly, low-temperature environments may require hoses designed to stay flexible in freezing conditions.
Fluid Compatibility
Hydraulic hoses are exposed to various fluids, including oils, water-based solutions, and synthetic fluids. It’s essential to choose a hose compatible with the specific fluid in your system. Some fluids can be corrosive or cause the hose material to degrade over time.
To ensure longevity and safety, select hoses that are resistant to the chemical properties of the fluid, as well as to common factors such as UV light, ozone, and abrasion.
Common Hydraulic Hose Materials and Their Benefits
Rubber Hydraulic Hoses
Rubber hydraulic hoses are one of the most commonly used types due to their excellent flexibility and cost-effectiveness. These hoses are made of synthetic rubber, which provides high resistance to oil, fuel, and abrasion, making them ideal for many industrial and agricultural applications.
Benefits:
- Highly flexible and suitable for tight bends.
- Relatively cost-effective compared to other materials.
- Resistant to oils, fuels, and abrasions.
Limitations:
- Can be susceptible to UV damage over time if exposed to direct sunlight.
- May not be ideal for high-temperature applications.
Rubber hoses are best used in systems with moderate pressure and temperatures, where flexibility is crucial for maneuverability and space constraints.
Thermoplastic Hydraulic Hoses
Thermoplastic hydraulic hoses are made from polymers that provide high resistance to chemicals, abrasion, and extreme environmental conditions. These hoses are lightweight, flexible, and can withstand a wider range of chemicals compared to rubber hoses.
Benefits:
- Excellent chemical resistance, ideal for harsh environments.
- Lightweight and highly flexible, making them easy to install and handle.
- Available in various pressure ratings and sizes.
Limitations:
- May not be as durable in high-temperature environments as rubber or steel-braided hoses.
- Less abrasion-resistant in some applications compared to rubber hoses.
Thermoplastic hoses are typically used in applications where chemical exposure and weight are significant concerns, such as in the chemical processing, pharmaceutical, and food industries.
Steel-Braided Hydraulic Hoses
Steel-braided hydraulic hoses feature a reinforcing layer of braided steel wire, which makes them extremely durable and capable of withstanding high-pressure environments. These hoses are ideal for heavy-duty applications that require strength, such as in mining, construction, and oil & gas industries.
Benefits:
- Offers superior pressure resistance and durability.
- Highly resistant to abrasion and external damage.
- Ideal for heavy-duty and high-pressure applications.
Limitations:
- Less flexible compared to rubber or thermoplastic hoses.
- More expensive than other hose types due to the steel braiding.
Steel-braided hoses are the best choice for high-pressure, high-strength applications where durability and performance are critical, such as in hydraulic systems in heavy machinery.
How to Install and Maintain Hydraulic Hoses
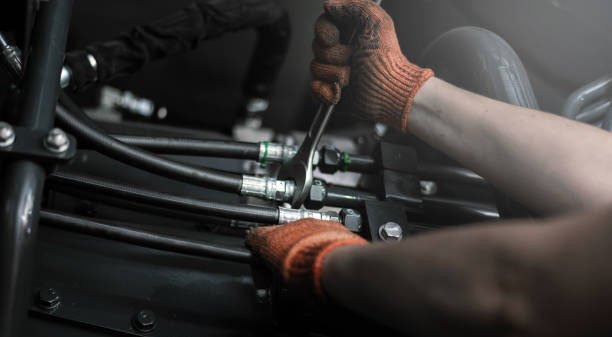
Installation Tips
Proper installation is crucial to the longevity and performance of your hydraulic hoses. Here are a few key tips:
- Avoid sharp bends: Hoses should not be bent too tightly. Doing so can weaken the hose and cause early failure. Use hose guides or supports to keep the hose in the proper shape.
- Use correct fittings: Always choose the appropriate size and type of fittings for your hose. Mismatched fittings can cause leaks or even rupture the hose.
- Minimize vibration: Ensure that hoses are routed in such a way that they are not subjected to excessive vibration, as this can cause wear and tear over time.
Following these installation best practices will help ensure the hydraulic hose functions efficiently, providing maximum performance and reducing the risk of failure.
Maintenance Best Practices
Regular maintenance is essential to keep your hydraulic hoses in good working condition. Here are some maintenance tips:
- Inspect regularly: Check hoses for signs of wear, cracks, or leaks. Look for external abrasions, bulges, or any fluid leaks around the fittings.
- Keep hoses clean: Clean the hoses regularly to prevent contaminants from entering the system and causing blockages or damage to the fluid inside.
- Check for kinks: Hoses should never be kinked, as this restricts the flow of hydraulic fluid and can damage the hose material.
By maintaining your hydraulic hoses properly, you can extend their life and prevent costly repairs or replacements.
Signs of a Faulty Hydraulic Hose
Leaking Fluid
One of the most common signs of a faulty hydraulic hose is fluid leakage. Leaks may occur due to cracks, abrasions, or damage to the hose material. Any visible fluid around the hose or fittings should be addressed immediately to avoid system inefficiency or failure.
Why it’s a problem: A leaking hydraulic hose can lead to reduced fluid pressure, which impacts the overall performance of the hydraulic system. Leaks also pose safety hazards, as hydraulic fluid can be hazardous to workers and the environment.
Increased Vibration or Noise
Increased vibration or unusual noise from the hydraulic system can indicate a problem with the hydraulic hose. When hoses lose their integrity, they may cause pressure fluctuations that affect the efficiency of the system.
Why it’s a problem: Persistent vibrations or noise indicate that the hydraulic fluid is not flowing correctly, which could result in poor equipment performance and, in the worst case, damage to other components of the system.
Decreased Performance
If your equipment is experiencing decreased performance, it may be due to a malfunctioning hydraulic hose. This can happen when the hose has been compromised, causing reduced fluid pressure or flow rates.
Why it’s a problem: A compromised hydraulic hose can lead to inefficient operation, causing the machinery to struggle with normal tasks. This can increase wear and tear on other components, leading to further damage and higher repair costs.
Conclusion
Choosing the right hydraulic hose is essential for ensuring the efficiency, safety, and longevity of your hydraulic system. Consider factors like pressure rating, temperature range, and fluid compatibility when making your decision. Additionally, selecting the appropriate hose material based on your application’s needs will contribute to optimal performance. Regular maintenance and prompt replacement of faulty hoses can help extend the life of your equipment and reduce downtime.
By understanding the different types of hydraulic hoses available and following best practices for installation and maintenance, you can ensure the smooth operation of your hydraulic systems and avoid costly repairs. If you’re unsure about which hose is right for your application, always consult a professional to help make the most informed decision.
FAQ
- What is a hydraulic hose? A hydraulic hose is a flexible tube used to carry hydraulic fluid in a hydraulic system, transferring energy to power machinery or equipment.
- Why is the material of a hydraulic hose important? The material determines the hose’s durability, flexibility, and resistance to factors like pressure, temperature, and chemicals, making it crucial for system performance.
- How do I choose the right hydraulic hose? When selecting a hydraulic hose, consider factors like fluid compatibility, pressure ratings, temperature ranges, and hose material based on your application’s requirements.
- Can hydraulic hoses be reused? While it’s generally best to replace worn-out hoses, hydraulic hoses in good condition can sometimes be reused after proper inspection and testing for leaks or damage.
- What causes hydraulic hose failure? Common causes of hydraulic hose failure include improper installation, exposure to high pressures, extreme temperatures, abrasion, or chemical damage.
- How often should hydraulic hoses be checked? Hydraulic hoses should be inspected regularly, typically every 3-6 months, for signs of wear, leaks, cracks, or other damage, especially in high-pressure systems.