In industries where precision and reliability are paramount, swage fittings (swaged fittings) have become a critical component. These fittings create secure, leak-proof connections, primarily in metal tubing systems used across various applications such as aerospace, automotive, and oil and gas industries. But what exactly are swage fittings, and why are they so essential?
What Is a Swage Fitting?
A swage fitting, also known as a swaged fitting, is a type of mechanical fitting used to connect metal tubing to various system components, ensuring a tight, secure, and leak-resistant connection. People commonly use these fittings in high-pressure environments where maintaining connection integrity is crucial. Swaged fittings offer durability, ease of installation, and the ability to withstand significant stress without compromising connection quality.
Types of Swage Fittings
Engineers design swage fittings to meet the diverse needs of various industries, providing secure and reliable connections in critical systems. To choose the right swage fitting for your application, understand the different types available. These types categorize based on their specific applications and operational designs.
Application-Based Types of Swage Fittings:
- Tube Fittings:
Tube fittings create secure connections in metal tubing systems, commonly used in industries like aerospace, automotive, and industrial manufacturing. They ensure fluid or gas systems remain leak-proof under high pressure and extreme conditions. Swage tube fittings, in particular, are crucial in hydraulic and pneumatic systems where tubing integrity is vital for optimal performance. - Hose Fittings:
Hose fittings connect flexible hoses to components like valves, pumps, or rigid pipes. They are essential in applications requiring flexibility and movement, such as in heavy machinery, automotive systems, and industrial equipment. Swage hose fittings ensure that the hose remains securely attached, even under high-pressure conditions, preventing leaks and ensuring efficient operation. - Cable Fittings:
Swage cable fittings secure and terminate cables in settings like marine, construction, and rigging applications. They create strong, durable connections that withstand significant tension and environmental stress. These fittings are essential in applications where safety and reliability are crucial, such as in load-bearing structures or safety lines.
Operational Design Types of Swage Fittings:
- Single Swage Fittings:
They are designed for applications where a one-time, permanent connection is required. The swaging process involves compressing the fitting around the tubing or hose, creating a tight seal that is resistant to leaks and disconnections. These fittings are ideal for high-pressure environments where the connection must remain secure over long periods without the need for maintenance or adjustment. - Double Swage Fittings:
They provide an added layer of security by requiring two swaging operations. This double compression ensures an even tighter seal, making these fittings suitable for the most critical applications where failure is not an option. They commonly fit systems that experience extreme pressure or where leaks could have catastrophic consequences, such as in aerospace or deep-sea operations. - Compression Swage Fittings:
They accommodate slight movements in the tubing, such as expansion or contraction caused by temperature changes. These fittings maintain a secure connection even when the tubing undergoes minor dimensional changes, making them ideal for systems exposed to varying temperatures or where the material properties of the tubing may change over time. - Flared Swage Fittings:
They involve flaring the end of the tubing before the swaging process. This design enhances the strength and reliability of the connection, particularly in high-pressure systems. The flaring process increases the surface area of the connection, which helps to distribute stress more evenly and reduce the risk of leaks or failures. People often use these fittings in fuel lines, brake systems, and other critical fluid transport systems.
Materials Used in Swage Fittings
Common Materials
Swage fittings are typically made from robust materials capable of withstanding the stresses of high-pressure environments. The most common materials include:
- Stainless Steel: Resistance and strength, often used in swage fittings, especially in harsh environments.
- Brass: Often used in less demanding applications, brass offers a good balance between cost and durability.
- Aluminum: Lightweight and resistant, used in applications where weight is a concern, such as in the aerospace industry.
- Titanium: Used in highly specialized applications, titanium fittings offer unmatched strength and resistance to extreme conditions, though at a higher cost.
Material Selection Criteria
When selecting materials for swage fittings, need consider factors such as the application’s operating environment, pressure requirements, and compatibility with the connected materials. The right material ensures longevity and reliability in the fitting’s performance.
Durability and Corrosion Resistance
Durability and corrosion resistance are critical factors in the effectiveness of swage fittings. For instance, materials such as stainless steel offer excellent resistance to corrosion. As a result, these fittings remain functional even in harsh environments like marine or chemical processing industries.
Manufacturing Process of Swage Fittings
The manufacturing of swage fittings involves several stages, such as material selection, machining, and swaging. Each stage is carefully designed to ensure that the final product meets the required specifications and standards. Consequently, this meticulous process guarantees high-quality fittings.
Steps Involved in Production
- Preparation: The tubing and fitting are prepared, ensuring that both are clean and free of any debris that could affect the connection.
- Insertion: The tubing is inserted into the swage fitting until it reaches a predetermined stop point, ensuring correct alignment.
- Swaging: The swaging tool is applied to the fitting, compressing the fitting around the tubing. This process deforms the metal, creating a tight, permanent connection.
- Inspection: After swaging, the connection is inspected for any signs of improper fitting or defects that could lead to leaks or failure.
Quality Control Measures
Quality control is a crucial aspect of manufacturing swage fittings. Testing methods such as pressure testing, dimensional inspection, and material analysis are used to ensure the fittings meet industry standards and perform reliably in their intended applications.
Applications
Swage fittings are versatile and find applications in numerous industries. Their primary use is in hydraulic systems where high-pressure fluids are transported through metal tubing. However, they are also common in the following sectors:
- Aerospace: In aircraft systems, swage fittings ensure secure connections in fuel, hydraulic, and pneumatic systems.
- Automotive: These fittings are used in brake lines and other critical systems where reliable fluid transport is necessary.
- Oil and Gas: Swage fittings are essential in pipelines, where they provide leak-proof connections in high-pressure environments.
- Chemical Processing: The fittings are used to connect tubing in systems that handle corrosive substances, ensuring safety and reliability.
How to Install a Swage Fitting
Proper installation of swage fittings, or swaged fittings, is essential for ensuring their performance and longevity. Follow these steps to ensure a proper installation:
- Cut the Tubing: Cut the tubing to the desired length using a tube cutter. Ensure the cut is clean and square.
- Deburr the Edges: Use a deburring tool to remove any burrs from the cut edge of the tubing, which could interfere with the fitting’s seal.
- Clean the Tubing: Wipe the tubing with a clean, lint-free cloth to remove any oil, dirt, or debris.
- Insert the Tubing: Insert the tubing into the swage fitting until it reaches the stop point.
- Apply the Swaging Tool: Attach the swaging tool to the fitting and activate it to compress the fitting around the tubing.
- Inspect the Connection: After swaging, inspect the connection to ensure it is secure and free of defects.
Maintaining
Proper maintenance of swage fittings is crucial to ensure long-term reliability and safety. Here are some tips for maintaining swage fittings:
- Regular Inspections: Periodically inspect the fittings for signs of wear, corrosion, or damage. Replace any fittings that show signs of degradation.
- Tightening: Over time, fittings may loosen due to vibration or pressure changes. Check and tighten fittings as needed to maintain a secure connection.
- Cleaning: Keep the fittings clean and free of debris, which can affect their performance.
- Lubrication: In some cases, applying a suitable lubricant to the fittings can help prevent corrosion and make future maintenance easier.
What Are the Advantages of Swaged Fittings?
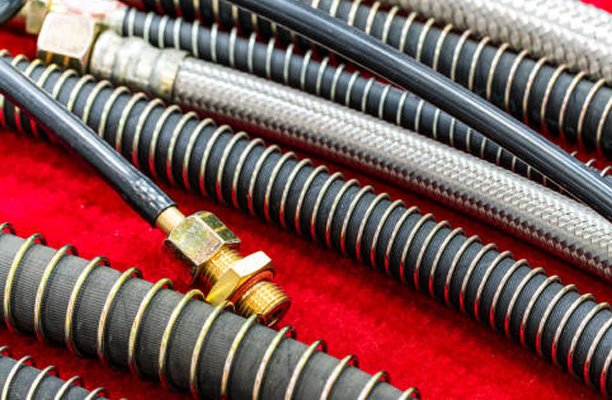
Swaged fittings, particularly Swage Hydraulic Fittings, are favored in many industries due to their numerous advantages. Here’s a closer look at why swaged fittings are often the preferred choice for critical hydraulic applications:
1. Superior Leak Resistance:
One of the primary advantages of swaged fittings is their ability to create a leak-proof seal. The swaging process compresses the fitting tightly around the tubing, ensuring no gaps or weak points that could lead to leaks. This is particularly important in high-pressure hydraulic systems where leaks can be costly and dangerous.
2. High Durability:
Swage hydraulic fittings are built to withstand harsh conditions, including extreme pressures, temperatures, and corrosive environments. The materials used, such as stainless steel and titanium, further enhance the durability and longevity of these fittings, reducing the need for frequent replacements.
3. Secure and Permanent Connections:
Once a swage fitting is installed, it forms a permanent connection that is highly resistant to loosening or failure. This makes swage fittings ideal for critical applications where long-term reliability is essential.
4. Versatility Across Applications:
Swage fittings offer high versatility and suit a wide range of applications, including aerospace, automotive, and oil and gas industries. Their ability to perform reliably in diverse environments makes them a go-to solution for many engineers and technicians.
5. Cost-Effectiveness:
Although swage fittings may need more precise installation tools and techniques, they often prove to be more cost-effective over time. Their durability and reliability reduce the need for repairs and replacements, leading to lower maintenance costs over time.
6. Compatibility with Various Tubing Materials:
Swage fittings connect with various types of metal tubing, including stainless steel, aluminum, and titanium. This compatibility ensures secure connections in systems with specific material requirements, no matter the tubing material.
Common Issues in Installation and How to Avoid Them
Even with the best tools and materials, issues can arise during the installation of swage fittings. Here are some common problems and tips on how to avoid them:
- Incorrect Tubing Alignment: If the tubing is not properly aligned during insertion, the swage fitting may not create a proper seal. Always ensure the tubing is straight and fully inserted before swaging.
- Insufficient Swaging Force: Applying insufficient force during the swaging process can lead to a weak connection. Ensure the swaging tool is properly calibrated and capable of delivering the necessary force.
- Contaminated Surfaces: Dirt, oil, or other contaminants on the tubing or fitting can prevent a proper seal. Always clean the surfaces before installation.
- Improper Tool Selection: Using the wrong swaging tool or die can result in an improper fit. Make sure to use tools that are specifically designed for the type and size of fitting you are installing.
Swage Fitting vs. Other Fitting Types
Swage fittings are not the only type of fittings available, and it’s important to understand how they compare to other options:
- Compression Fittings: Unlike swage fittings, compression fittings rely on a nut and ferrule to create a seal. While easier to install, they may not offer the same level of security as swage fittings in high-pressure environments.
- Threaded Fittings: These fittings use threads to create a connection. They are common in low-pressure systems but may not provide the same leak-proof assurance as swage fittings in high-pressure applications.
- Welded Fittings: Welding provides a permanent connection, but it requires more skill and equipment compared to swaging. Swage fittings offer a more accessible solution without the need for welding expertise.
What is the Difference Between Crimp and Swage?
When it comes to securing hydraulic connections, both crimp and swage fittings are popular choices. However, they operate differently and are suitable for different applications. Understanding the key differences between crimp and swage fittings can help you choose the right option for your hydraulic system.
Crimp Fittings:
Crimp fittings involve compressing a sleeve or ferrule around the tubing using a crimping tool. This method creates a secure connection that is strong enough for many hydraulic applications. Crimping is generally quicker and easier to perform than swaging, making it a popular choice for field installations where time and simplicity are crucial.
Swage Fittings:
On the other hand, involve deforming the fitting itself around the tubing through a swaging process. This method provides a more robust and leak-proof connection compared to crimping, especially in high-pressure environments. Applications like aerospace and high-pressure hydraulic systems typically prefer swage fittings when maximum reliability is essential.
Key Differences:
- Strength and Reliability: Swage fittings offer a stronger, more secure connection that is less likely to fail under high pressure or stress. Crimp fittings, while strong, may not provide the same level of security in extreme conditions.
- Ease of Installation: Installing crimp fittings is easier and faster, making them ideal for applications that require quick assembly. Swage fittings require more precise installation but result in a more permanent and reliable connection.
- Application Suitability: Medium-pressure hydraulic systems often use crimp fittings, while high-pressure systems requiring maximum reliability typically rely on swage fittings.
Innovations in Technology
The technology behind swage fittings continues to evolve, with new innovations enhancing their performance and ease of use. Some of the latest advancements include:
- Quick-Connect Swaged Fittings: These fittings allow for faster installation without compromising on security or reliability, ideal for applications where time is critical.
- Corrosion-Resistant Coatings: New coatings are being developed to enhance the corrosion resistance of swage fittings, extending their lifespan in harsh environments.
- Smart Swaging Tools: Advances in tool technology include digital readouts and automated systems that ensure precise swaging with minimal user input, reducing the risk of human error.
Conclusion
Swage fittings are an indispensable component in many high-pressure and high-stakes environments. Their ability to provide secure, leak-proof connections makes them a preferred choice across industries. To ensure the reliability and longevity of swage fittings, it is crucial to understand the different types, the materials they are made from, and the correct installation process. As technology advances, it will continue to evolve, offering even greater performance and ease of use in the future.
FAQs
What is the primary use of swage fittings?
High-pressure environments primarily use swage fittings, also known as swaged fittings, to create secure, leak-proof connections in metal tubing systems, commonly found in industries like aerospace, automotive, and oil and gas.
How does a swage fitting differ from a compression fitting?
While both create secure connections, swage fittings use a swaging process that deforms the fitting around the tubing, providing a more robust and leak-proof seal compared to the nut and ferrule system of compression fittings.
Can swage fittings be reused?
Designers generally create swaged fittings for single-use. Once installed, the fitting is permanently deformed to create a secure connection, making it difficult to reuse without compromising the integrity of the seal.
What materials are swage fittings made from?
Manufacturers typically make swaged fittings from durable materials like stainless steel, brass, aluminum, and titanium, depending on the application and environmental conditions.
What tools are needed for installing swage fittings?
Installing swage fittings requires a swaging tool, which applies the necessary radial force to compress the fitting around the tubing. The specific type of tool may vary depending on the fitting and tubing size.
Are swage fittings suitable for all types of tubing?
They are most commonly used with metal tubing, such as stainless steel or aluminum. They may not be suitable for use with non-metallic tubing, as the swaging process relies on the deformation of the metal to create a secure seal.