Introduction to Hydraulic Fittings
The Role of Fittings in Hydraulic Systems
Hydraulic systems depend heavily on fittings to manage the direction, control, and flow of pressurized fluids. These components play a vital role in minimizing leakage, enhancing safety, and improving overall performance. Without the right fittings, even the most advanced hydraulic setup can become inefficient or prone to failure.
Importance of Choosing the Right Type of Swivel
Choosing the appropriate swivel fitting is crucial for ensuring flexibility, durability, and long-term efficiency in hydraulic applications. The decision between a general swivel fitting and a 90 degree live swivel can significantly impact system layout, performance under pressure, and ease of maintenance.
What Are Swivel Fittings?
Definition and Design Overview
Swivel fittings are mechanical connectors that allow rotational movement between two connected components. They are engineered to reduce stress from hose twisting and bending, allowing hoses to pivot and adjust during machine operation without compromising seal integrity.
Types of Swivel Fittings
There are several types of swivel fittings, including straight swivel joints, 45-degree swivel fittings, and live swivels. Each is tailored to specific spatial and dynamic needs within hydraulic systems. Materials typically used include brass, stainless steel, and carbon steel to ensure compatibility with a range of fluids and environmental conditions.
How They Function in Motion Applications
In mobile or constantly moving equipment, swivel fittings reduce wear and tear by allowing free movement. This functionality minimizes hose fatigue and enhances system longevity, especially in dynamic machinery like forklifts, agricultural sprayers, and construction vehicles.
What Are 90 Degree Live Swivels?
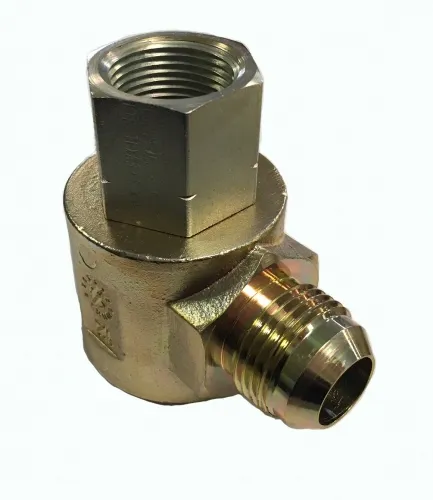
Structural and Functional Overview
90 degree live swivels are a specific type of swivel fitting designed to provide a right-angle turn in fluid pathways while allowing continuous rotation. These fittings are engineered with precision-machined ball bearings or bushings to maintain free rotation even under high pressure.
Key Mechanical Advantages
The main advantage of 90 degree live swivels lies in their ability to fit compact spaces while enabling hose articulation. This results in a more ergonomic hose layout, reduced space requirements, and less mechanical stress on connected hoses.
Common Use Cases and Industries
These fittings are particularly common in hydraulic equipment where space is constrained, such as boom arms, mobile cranes, and compact utility vehicles. Industries like mining, agriculture, and material handling rely on 90 degree live swivels for their combination of compactness and fluid motion capabilities.
Comparative Overview: Swivel Fittings vs 90 Degree Live Swivels
Design Differences
Swivel fittings generally come in straight or angled variations and may or may not support full rotation under pressure. In contrast, 90 degree live swivels are explicitly engineered for high-performance articulation at a right angle, often incorporating ball bearing systems for smoother motion and greater reliability.
Installation Flexibility
Standard swivel fittings are more versatile in positioning and can be adapted for various layout configurations. However, 90 degree live swivels excel in tight or angled installations where space is a limiting factor. This makes them a preferred choice in systems requiring right-angle turns with rotational flexibility.
Pressure and Temperature Tolerances
Both types are built to endure hydraulic pressures, but live swivels often outperform standard swivel fittings in high-load, high-pressure scenarios due to their robust internal construction. Temperature tolerance is generally similar, although material choice can affect resilience in extreme conditions.
Performance & Efficiency
Rotational Motion Capabilities
Swivel fittings allow limited or fixed degrees of rotation depending on the model. 90 degree live swivels, however, are purpose-built to offer full rotational freedom without compromising seal integrity. This makes them ideal for dynamic hydraulic circuits where constant motion is present.
Leak Prevention and Maintenance
Modern swivel designs feature advanced sealing technologies such as O-rings and Teflon seals to prevent leakage. Live swivels typically provide better long-term sealing due to precision machining and specialized internal components. Maintenance is also easier as live swivels are designed for longevity and ease of inspection.
System Longevity Impact
Using the right swivel fitting can drastically improve system durability. Live swivels, with their enhanced motion range and minimal friction, contribute to extended hose and component life. Swivel fittings also help, but their benefit largely depends on application-specific conditions and usage intensity.
Pros and Cons of Swivel Fittings
Strengths in Diverse Systems
Swivel fittings are cost-effective, widely available, and suitable for a broad range of hydraulic and pneumatic systems. Their modularity makes them an excellent choice for general-purpose installations where movement is moderate and spatial constraints are minimal.
Situational Limitations
Swivel fittings can be limited in applications involving tight angles or where constant rotational movement is needed. In these cases, standard swivels may experience faster wear or contribute to inefficient fluid flow paths, especially under high pressure or continuous operation.
Pros and Cons of 90 Degree Live Swivels
Where They Outperform Other Fittings
90 degree live swivels shine in applications that demand a combination of directional change and full rotational movement. Their compact, angled design reduces the need for additional adapters or elbows, streamlining hydraulic circuit layouts and minimizing turbulence. Their ball-bearing mechanisms allow for smooth rotation, even under high pressure, which enhances performance in dynamic systems.
Limitations to Consider
Despite their benefits, 90 degree live swivels can be more expensive than standard swivel fittings. Their complex internal construction may also make them less accessible for on-the-spot repairs or field replacements. Additionally, improper installation can compromise the rotational ability, negating their advantages and potentially leading to early failure.
Material Considerations for Both Types
Stainless Steel vs Brass vs Composite Materials
The choice of material directly impacts the fitting’s performance and longevity. Stainless steel offers superior strength, corrosion resistance, and durability, making it ideal for harsh or marine environments. Brass is often used for its cost-effectiveness and resistance to rust in moderately corrosive conditions. Composite materials are lightweight and resist certain chemicals, but may lack the strength required for high-pressure applications.
Environmental Impact on Material Choice
Choosing the right material should consider the surrounding environment—temperature, fluid type, pressure, and exposure to chemicals or moisture. For example, systems operating in saltwater or chemical plants benefit greatly from stainless steel. In contrast, agricultural or general-purpose setups may find brass or composite fittings adequate and more economical.
Cost Comparison and Value Analysis
Upfront Cost vs Long-Term Value
Swivel fittings are generally less expensive upfront and serve well in basic hydraulic applications. 90 degree live swivels, while costlier, often justify their price through reduced hose wear, better efficiency, and longer service intervals. Evaluating cost should always include maintenance, downtime, and replacement cycles.
Maintenance and Replacement Frequency
Standard swivel fittings may require more frequent inspection and replacement, especially in high-stress environments. 90 degree live swivels, due to their robust build, typically last longer and demand less frequent servicing. Over time, this can result in significant savings and increased operational uptime.
Industry Applications
Agriculture and Heavy Machinery
In agricultural machinery, swivel fittings and 90 degree live swivels are essential for ensuring hose flexibility during equipment articulation. Tractors, sprayers, and harvesters benefit from these fittings as they allow for safe hose movement and reduce downtime due to hydraulic failures. Heavy machinery like excavators and loaders also rely on these components to withstand intense pressures and repetitive movements.
Automotive and Industrial Hydraulics
Automotive manufacturing lines and industrial automation systems often use high-pressure hydraulic circuits where spatial constraints demand precise component choices. 90 degree live swivels are commonly integrated into these systems to reduce stress on hoses and ensure efficient motion. Swivel fittings are often employed in less dynamic zones where some flexibility is needed but full rotation isn’t required.
Installation Guidelines and Best Practices
Tools Required
Installing swivel fittings and 90 degree live swivels typically requires a set of hydraulic wrenches, thread sealants or tape (depending on the fitting type), torque tools for accurate tightening, and in some cases, alignment tools to ensure rotational functionality. Always refer to the manufacturer’s instructions for torque specifications and compatibility.
Avoiding Common Installation Mistakes
One of the most frequent issues is over-tightening, which can damage the seal and restrict the swivel’s ability to rotate. Misalignment during installation can also lead to hose twisting or premature wear. It’s vital to ensure that the fitting is correctly oriented before tightening and to avoid contaminating the internal bearing system with dirt or debris.
Maintenance and Troubleshooting
Inspection Tips
Routine inspections should focus on signs of leakage, unusual noise during operation, and restricted movement in the swivel joint. It’s also recommended to check hose alignment and ensure that there’s no visible strain on the fitting or surrounding components. Periodic cleaning can help maintain internal mechanisms, especially in dusty or dirty environments.
Diagnosing Issues Quickly
If a swivel fitting is leaking, it may be due to worn seals, improper torque, or damage to the rotating surface. In 90 degree live swivels, difficulty in rotation could signal internal contamination or bearing failure. Prompt diagnosis and part replacement can prevent broader system failures and costly downtime.
Expert Tips for Choosing the Right Fitting
Matching Specifications to System Needs
Selecting the right fitting begins with understanding your system’s operating pressure, temperature, and movement dynamics. Ensure the fitting’s rated PSI exceeds system pressure by a safety margin and that its design matches the spatial layout. If movement is a major factor, lean toward live swivels with proven durability in rotation-heavy applications.
Consulting Manufacturer Datasheets
Always consult the technical datasheets provided by manufacturers. These documents offer precise dimensions, torque recommendations, material specifications, and compatibility charts that are critical for choosing the optimal component for your system. Failure to review these can lead to performance mismatches and early failure.
Future Trends in Hydraulic Fittings
Smart Fittings and IoT Integration
The future of hydraulic systems lies in smart technology integration. Manufacturers are developing fittings with embedded sensors that monitor rotation, temperature, and pressure in real time. These smart swivels can alert technicians of issues before they cause downtime, making preventive maintenance more efficient and accurate.
Sustainability in Design
As industries shift toward sustainability, the use of recyclable materials and energy-efficient production methods is gaining traction. Future swivel fittings may incorporate bio-based polymers or low-carbon metals, while designs will aim to reduce waste during installation and operation.
Conclusion
Choosing between swivel fittings and 90 degree live swivels depends on your specific application needs. For systems with moderate movement and flexible layout options, standard swivel fittings are cost-effective and easy to install. However, in compact, high-motion, or high-pressure environments, 90 degree live swivels offer superior performance and reliability.
Making an Informed Decision
Always balance initial cost with long-term value. Consider space constraints, movement frequency, maintenance accessibility, and system pressure before selecting your fitting. With the right component, you can significantly enhance your hydraulic system’s performance and lifespan.
FAQs
1. What is the primary function of a swivel fitting?
Swivel fittings allow rotation between connected components to prevent hose twisting and reduce mechanical stress in hydraulic systems.
2. Are 90 degree live swivels better than standard swivel fittings?
They are better suited for compact, high-movement, or high-pressure environments, but may be costlier and overengineered for simpler systems.
3. Can I retrofit 90 degree live swivels into existing systems?
Yes, provided the system pressure ratings and dimensions match. Always check compatibility using manufacturer datasheets before retrofitting.
4. What materials are best for corrosive environments?
Stainless steel is the preferred material for corrosive or marine environments due to its excellent resistance to rust and chemical damage.
5. How often should swivel fittings be inspected?
Inspection frequency depends on usage, but generally every 3 to 6 months for high-use systems and annually for low-movement applications.