Introduction
Threaded connections are vital in a broad range of engineering, plumbing, mechanical, and industrial systems. Two primary thread types—taper threads and parallel threads—play crucial roles in determining the reliability and safety of a system. While they may look similar at first glance, they serve different purposes and perform differently under varying conditions.
In this in-depth guide, we’ll explore the distinctions between taper and parallel threads, diving into their geometries, sealing mechanisms, applications, advantages, and installation tips. This knowledge is essential for engineers, mechanics, technicians, and contractors who want to ensure optimal component compatibility and system performance.
What Are Taper Threads?
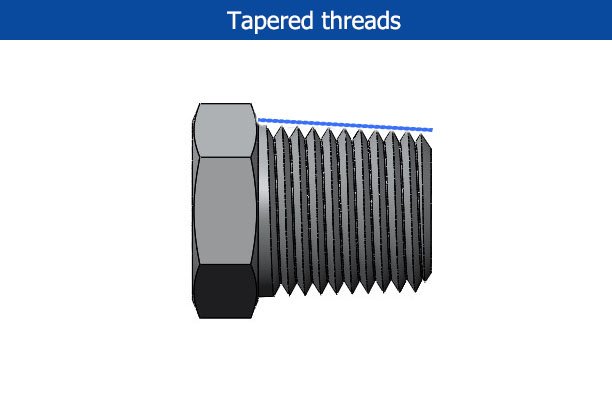
Definition
Taper threads are threaded connectors with a conical shape, meaning the diameter of the thread tapers or reduces along the thread length. This allows for a mechanical tightening action that enhances sealing, especially under pressure.
How They Work
As the male and female taper threads are tightened, they bind together due to the narrowing geometry. This wedging action compresses the threads, creating a high-pressure seal without relying solely on auxiliary sealing materials.
Common Standards
- NPT (National Pipe Taper): Predominantly used in North America.
- BSPT (British Standard Pipe Taper): Common in the UK and Commonwealth countries.
- ISO 7-1: International standard for pipe threads where pressure-tight joints are made on the threads.
Key Characteristics
- Taper angle: Approximately 1.7899° (or 1:16 taper ratio)
- Thread angle: Typically 60° for NPT and 55° for BSPT
- Sealing method: Metal-to-metal or with thread sealant
- Application range: High-pressure, high-sealing applications like gas and steam lines
What Are Parallel Threads?
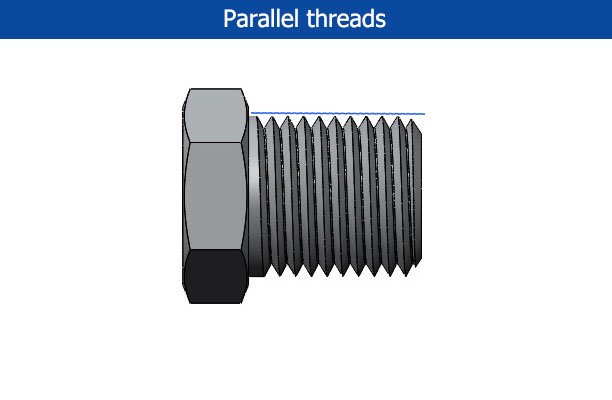
Definition
Parallel threads, also known as straight threads, maintain a consistent diameter throughout the entire thread length. These threads do not form a mechanical seal by themselves and thus rely on external sealing elements.
How They Work
Since parallel threads do not wedge into each other like taper threads, they require sealing washers, O-rings, or bonded seals to prevent leaks. These are positioned between the mating surfaces to ensure a tight, leak-proof fit.
Common Standards
- BSPP (British Standard Pipe Parallel): Used across Europe and Commonwealth regions.
- ISO Metric Threads (ISO 261 / ISO 965): Standardized metric parallel threads
- UN/UNF (Unified National Thread / Unified Fine Thread): Common in hydraulic fittings
Key Characteristics
- Thread angle: 55° (BSPP) or 60° (UN, Metric)
- Sealing method: O-ring or bonded washer
- Application range: Systems requiring frequent disassembly or low-pressure fittings
Key Differences Between Taper and Parallel Threads
1. Thread Geometry
- Taper Threads: Diameter decreases along the thread length
- Parallel Threads: Constant diameter
2. Sealing Method
- Taper Threads: Achieve seal through wedging and optional sealants (e.g., PTFE tape)
- Parallel Threads: Depend on additional sealing components
3. Pressure Resistance
- Taper Threads: Better suited for high-pressure systems due to the tight, wedging fit
- Parallel Threads: Suitable for moderate to low-pressure applications
4. Ease of Assembly
- Taper Threads: Require careful alignment and torque control to avoid over-tightening
- Parallel Threads: Easier to assemble and disassemble repeatedly
5. Common Use Cases
- Taper Threads: Fire protection, natural gas, fuel lines
- Parallel Threads: Hydraulic systems, pneumatics, test equipment
Advantages of Taper Threads
- Provides mechanical strength and leak-tight seal without gaskets
- Better suited for dynamic environments with vibration and pressure changes
- Reduces reliance on secondary seals
Disadvantages of Taper Threads
- Requires precise torque during installation
- Can damage threads if over-tightened
- Reusability is limited due to thread deformation after initial use
Advantages of Parallel Threads
- Ideal for equipment requiring frequent maintenance and disassembly
- Provides consistent thread engagement and alignment
- Compatible with a variety of sealing washers and O-rings for leak-proof assembly
Disadvantages of Parallel Threads
- Not inherently pressure-tight
- Seal performance depends heavily on the quality and compatibility of sealing elements
Applications of Taper Threads
- Oil and Gas: Taper threads are used extensively in fuel lines and gas cylinders
- Water Supply Systems: Often found in older piping systems and municipal infrastructure
- Fire Protection Systems: Used in sprinkler systems for reliable pressure sealing
- Steam and High-Pressure Systems: Ensures safety under fluctuating pressure conditions
Applications of Parallel Threads
- Hydraulics: Common in hydraulic fittings where reusable seals are needed
- Pneumatics: Used in air compressors and valve assemblies
- Lab and Medical Equipment: Offers precision and flexibility for controlled systems
How to Identify Taper vs Parallel Threads
1. Visual and Physical Inspection
- Taper: Observe the decreasing thread diameter and test with a thread gauge at two points
- Parallel: Uniform diameter from end to end, typically finishes flush with the mating part
2. Use of Gauges
- Thread plug and ring gauges can accurately determine thread type
- Use a profile projector or caliper for diameter comparison along the length
Standards Comparison Table
Standard | Thread Type | Thread Angle | Application Region |
---|---|---|---|
NPT | Taper | 60° | North America |
BSPT | Taper | 55° | UK/Commonwealth |
BSPP | Parallel | 55° | UK/Commonwealth |
ISO Metric | Parallel | 60° | Global |
UN/UNF | Parallel | 60° | North America |
How to Choose the Right Thread Type
- Evaluate Pressure Requirements: Use taper threads for high-pressure; parallel for low to medium
- Consider Maintenance Needs: Choose parallel threads where frequent assembly/disassembly is required
- Check Compatibility: Ensure matching standards to avoid cross-threading or leaks
- Sealing Expectations: Choose based on the need for dry-seal or flexible-seal fittings
Installation Tips for Taper Threads
- Clean threads before installation
- Use PTFE tape or pipe dope compatible with fluid type
- Tighten with a torque wrench to prevent over-tightening
Installation Tips for Parallel Threads
- Use the correct O-ring or bonded washer
- Hand-tighten first, then apply measured torque
- Avoid using taper sealants unless specifically required
Common Mistakes to Avoid
- Mixing taper and parallel threads
- Omitting sealing elements on parallel threads
- Over-torquing taper threads, leading to cracks or leaks
- Assuming BSP and NPT are interchangeable without adapters
Conclusion
Choosing between taper and parallel threads is not just a matter of preference—it’s a critical decision that affects safety, efficiency, and functionality. Taper threads offer superior sealing under pressure, while parallel threads excel in applications requiring precision and ease of maintenance. By understanding the characteristics, standards, and proper use cases, professionals can make informed decisions and avoid costly errors.
FAQs
1. Can I use taper and parallel threads together?
No, combining these threads can lead to leakage, damage, or catastrophic failure due to mismatched geometries and sealing methods.
2. Which thread type is better for high pressure?
Taper threads are typically more reliable in high-pressure systems due to their inherent sealing action.
3. Are BSP and NPT threads compatible?
Not directly. They have different angles, thread forms, and pitch, which can result in leaks or cross-threading.
4. Do parallel threads always require a washer or O-ring?
Yes, for leak-free operation, a compatible sealing element is necessary.
5. How can I identify thread type without tools?
Visual cues help: taper threads appear conical; parallel threads remain cylindrical. However, for accuracy, use thread gauges or calipers.