Hydraulic systems are an integral part of modern machinery, allowing industries to operate with precision and power. From construction equipment to manufacturing processes, hydraulic systems offer unparalleled strength and flexibility. But what makes these systems tick? What are the essential components that ensure their smooth operation?
In this detailed guide, we’ll break down the key components of hydraulic systems, exploring their functions, types, and real-world applications. Whether you’re a professional working with hydraulics daily or just someone eager to learn more, this post has something for everyone.
Let’s dive into the heart of hydraulic systems and explore their most critical components.
What Are Hydraulic Systems?
Before we dissect the components, it’s worth understanding the basics of hydraulic systems. A hydraulic system is essentially a system that uses pressurized fluid (usually oil or water-based) to transmit power. These systems are commonly used in heavy machinery, vehicles, and even aviation because they can generate massive amounts of force efficiently and with precise control.
Hydraulic systems are made up of several components that work together to perform specific tasks. From generating power to transferring it to the right place and applying it effectively, each component has a unique role to play. Let’s explore these components in detail.
1. Hydraulic Pump – The Heart of the System
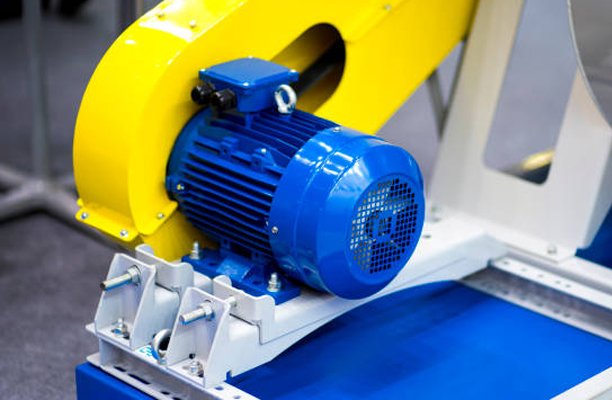
The hydraulic pump is often referred to as the heart of the hydraulic system—and for a good reason. Without it, the entire system comes to a standstill. The pump is responsible for creating the flow of hydraulic fluid, which is essential for generating pressure and enabling other components to function.
How Does a Hydraulic Pump Work?
A hydraulic pump works by converting mechanical energy from a motor or engine into hydraulic energy. As the pump operates, it creates a vacuum at its inlet, allowing hydraulic fluid to flow in from the reservoir. It then pressurizes the fluid and sends it into the system through the outlet.
Types of Hydraulic Pumps
There are three main types of hydraulic pumps, each designed for specific applications:
- Gear Pumps: Simple and cost-effective, gear pumps are ideal for low-pressure systems.
- Vane Pumps: More efficient and quieter than gear pumps, vane pumps are commonly used in mid-pressure systems.
- Piston Pumps: Highly efficient and capable of handling high pressures, piston pumps are used in heavy-duty applications.
Application of Hydraulic Pumps
In an excavator, the hydraulic pump powers the arm, allowing it to lift heavy loads or dig through dense soil.
2. Hydraulic Actuator – The Muscle of the System
If the pump is the heart of the hydraulic system, the actuators are its muscles. These components are responsible for converting the hydraulic energy back into mechanical energy to perform physical tasks. Actuators come in two main types: cylinders and motors.
Hydraulic Cylinders
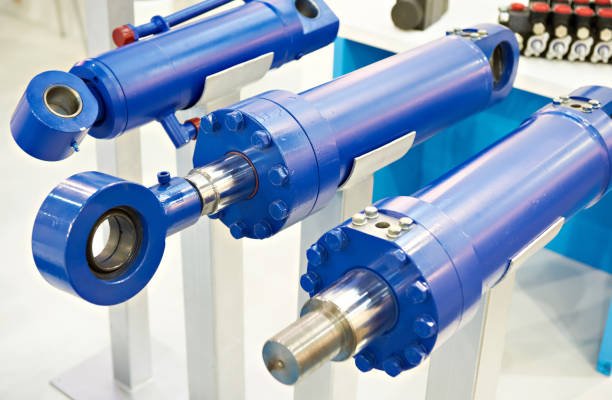
Cylinders provide linear motion, making them perfect for tasks like lifting, pushing, and pulling. They’re commonly found in construction equipment like bulldozers and cranes.
Hydraulic Motors
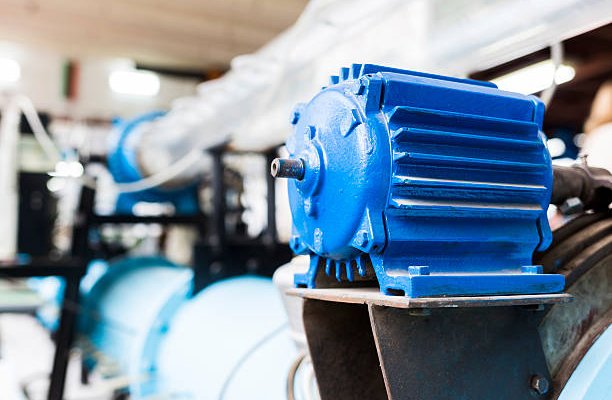
Motors provide rotary motion, which is essential for spinning wheels, conveyor belts, or rotating machinery.
How Do Actuators Work?
When pressurized hydraulic fluid enters the actuator, it forces the piston (in a cylinder) or the rotor (in a motor) to move. This motion is then used to perform work, such as lifting a load or driving a machine.
Examples of Actuator Use
- Hydraulic cylinders power the arms of forklifts and cranes.
- Hydraulic motors drive the propellers in ships or the wheels in off-road vehicles.
3. Hydraulic Reservoir – The Fluid Storage Tank
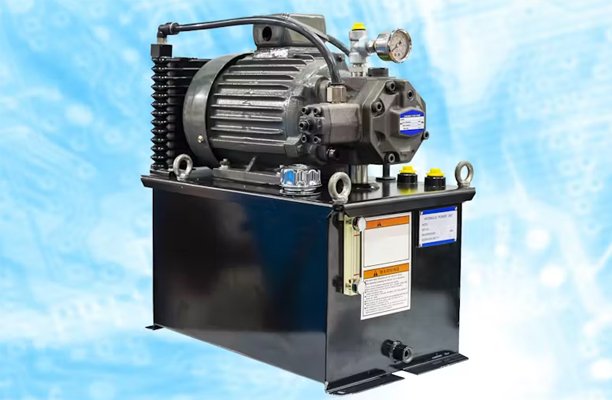
The reservoir is often overlooked, but it’s a critical component of any hydraulic system. Its primary function is to store hydraulic fluid, but it also plays a role in cooling and filtering the fluid.
Functions of a Hydraulic Reservoir
- Fluid Storage: The reservoir holds excess hydraulic fluid when it’s not being circulated.
- Heat Dissipation: As the fluid passes through the reservoir, it cools down, preventing overheating in the system.
- Contaminant Settling: The reservoir allows dirt and air bubbles to settle, improving fluid quality.
Sizing the Reservoir
The size of a hydraulic reservoir typically depends on the flow rate of the system. A good rule of thumb is to make the reservoir three to five times the system’s flow rate.
Maintenance Tips
- Regularly check fluid levels to ensure the reservoir isn’t running dry.
- Inspect for leaks or cracks that could cause fluid loss or contamination.
4. Hydraulic Valves – The Traffic Controllers
Valves are the unsung heroes of hydraulic systems. They regulate, control, and direct the flow of hydraulic fluid, ensuring that it reaches the right component at the right time and with the right pressure.
Types of Hydraulic Valves
- Pressure Control Valves: Prevent the system from exceeding safe pressure levels.
- Flow Control Valves: Regulate the flow rate of the hydraulic fluid.
- Directional Control Valves: Control the direction in which the fluid flows, allowing for precise movement of actuators.
How Valves Work
Valves are often controlled manually, electrically, or hydraulically. They open or close pathways within the system, ensuring fluid flows only where needed.
Example Use
In a backhoe loader, valves control the movement of the bucket arm, allowing the operator to dig, scoop, and dump materials with precision.
5. Hydraulic Fluid – The Lifeblood of the System
Hydraulic fluid isn’t just a medium for transmitting power—it’s also responsible for lubrication, cooling, and sealing within the system. Without high-quality fluid, the system wouldn’t function properly.
Functions of Hydraulic Fluid
- Power Transmission: Delivers the pressure and flow needed for system operation.
- Lubrication: Reduces friction between moving parts.
- Cooling: Absorbs and dissipates heat generated during operation.
- Sealing: Helps prevent leaks around seals and gaskets.
Types of Hydraulic Fluids
- Petroleum-Based Fluids: The most common type, suitable for most applications.
- Water-Based Fluids: Eco-friendly but less efficient than petroleum-based options.
- Synthetic Fluids: High-performance fluids designed for extreme conditions.
Pro Tip
Always monitor fluid quality and replace it as needed. Contaminated or degraded fluid can lead to system failures.
6. Filters – The System’s Guard Dogs
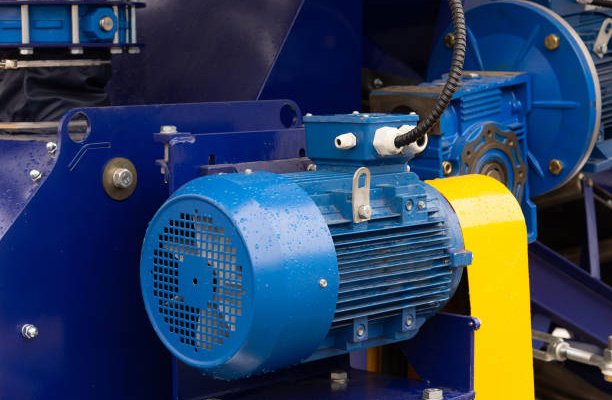
Contaminants like dirt, debris, and water are a hydraulic system’s worst enemy. Filters ensure that only clean fluid circulates through the system, protecting sensitive components from wear and tear.
How Filters Work
Filters trap particles and contaminants in the hydraulic fluid, preventing them from reaching critical components.
Types of Filters
- Suction Filters: Installed at the pump’s inlet to protect it from debris.
- Return-Line Filters: Capture contaminants as fluid returns to the reservoir.
- Pressure-Line Filters: Provide extra protection for high-pressure components.
7. Hydraulic Hoses and Fittings – The Circulatory System
Hydraulic hoses and fittings are the pathways through which fluid flows, connecting the various components of the system.
Key Features of Hoses and Fittings
- Durability: Designed to withstand high pressures and harsh conditions.
- Flexibility: Allow for movement and vibration without breaking.
8. Heat Exchangers – The Cooling System
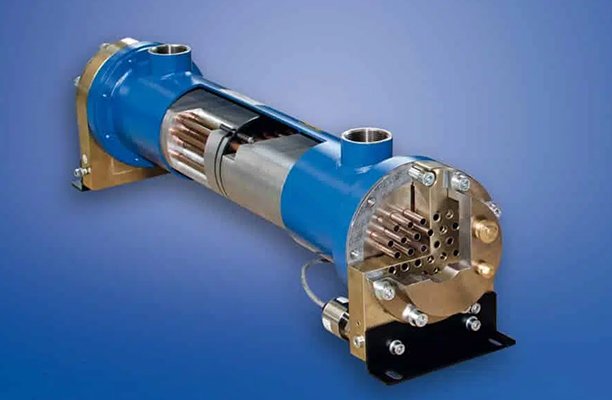
Hydraulic systems generate a lot of heat, and excessive temperatures can damage components or reduce efficiency. Heat exchangers solve this problem by cooling the hydraulic fluid.
Conclusion
Hydraulic systems are marvels of engineering that rely on the synergy of pumps, actuators, valves, and other components. Each part plays a vital role in ensuring the system operates efficiently and reliably.
Keep your system in tip-top shape with regular maintenance, and you’ll enjoy years of reliable performance.
FAQs
Q1: What happens if the hydraulic pump fails?
A1: If the hydraulic pump fails, the system won’t be able to generate the necessary pressure or flow of hydraulic fluid. This can cause the entire system to stop functioning, as the pump is essential for powering actuators and other components.
Q2: Can I use any type of hydraulic fluid in my system?
A2: No, it’s crucial to use the type of hydraulic fluid recommended by the equipment manufacturer. Using the wrong fluid can cause damage to components, reduce system efficiency, or lead to costly repairs.
Q3: How do I know when my hydraulic filter needs to be replaced?
A3: Signs that your hydraulic filter needs replacement include reduced system performance, unusual noises, increased fluid temperature, or visible contamination in the fluid. Regularly scheduled maintenance is the best way to avoid filter issues.
Q4: Why is the hydraulic reservoir important?
A4: The reservoir stores hydraulic fluid, helps dissipate heat, and allows air and contaminants to settle. Without a properly functioning reservoir, the system may overheat or circulate dirty fluid, causing long-term damage.
Q5: What is the most common cause of hydraulic system failure?
A5: The most common cause of failure is contamination of hydraulic fluid. Dirt, water, and other contaminants can damage sensitive components like valves, pumps, and actuators, leading to reduced performance or complete breakdowns.
Q6: How often should I inspect my hydraulic system?
A6: Hydraulic systems should be inspected regularly, with checks on fluid levels, hose condition, filter cleanliness, and overall performance. A thorough inspection every few months, along with routine maintenance, can prevent costly failures.