Ball valves are essential components in various industries, known for their reliability, durability, and efficient control of fluid flow. Widely used in sectors like oil and gas, pharmaceuticals, water treatment, and even residential plumbing, ball valves offer versatility that few other valve types can match. In this comprehensive guide, we’ll explore the fundamentals of ball valves, covering everything from their construction and types to their many applications and maintenance tips. Whether you’re selecting a ball valve for an industrial project or just curious about how they work, this guide has you covered.
What is a Ball Valve?
A ball valve is a type of quarter-turn valve that uses a hollow, perforated, and pivoting ball to control the flow of liquids, gases, or other substances through a pipeline. When the valve is open, the hole in the ball aligns with the flow path, allowing the fluid to pass through with minimal resistance. A 90-degree turn of the valve handle rotates the ball, bringing its solid side against the pipeline, which stops the flow entirely. This simple mechanism makes ball valves extremely effective for applications requiring quick shut-off and reliable sealing.
Ball valve components
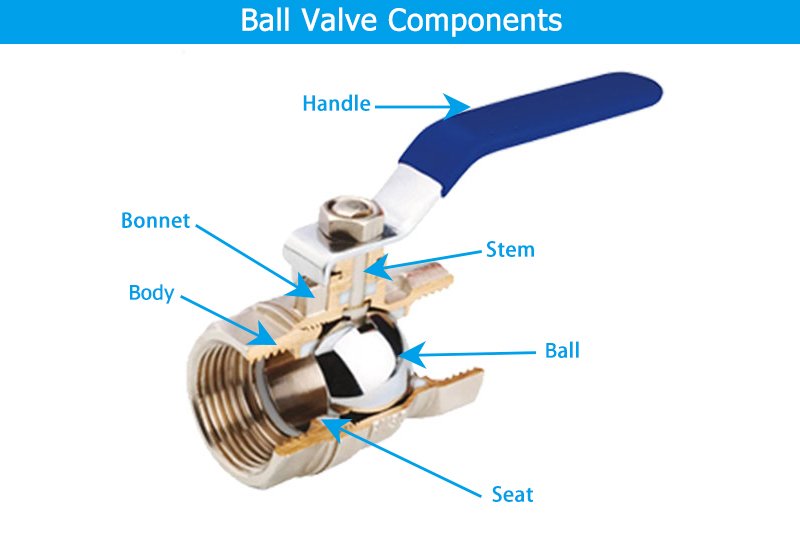
- Body: The body of the ball valve is the outer casing that holds all internal parts. Manufacturers can make it from various materials like stainless steel, brass, or PVC, depending on the application. They often select the body’s material based on the environment and the type of fluid it will handle.
- Ball: The ball is the core part of the valve, featuring a hole or port through its center. This ball rotates within the valve body to open or close the flow. The size and shape of the hole can vary, with full-port designs offering an unrestricted flow and V-port designs allowing for controlled flow rates.
- Seat: The seat is a ring-shaped sealing element that surrounds the ball. Made from soft materials like PTFE (Teflon) or other elastomers, the seat creates a tight seal when the ball is in the closed position. This seal is essential for preventing leaks and ensuring that the valve operates effectively even under high pressures.
- Stem: The stem is a shaft that connects the ball to the external handle or actuator. It transmits the rotation from the handle to the ball, allowing for manual or automated operation. High-quality ball valves often include anti-blowout stems for added safety in high-pressure applications.
- Handle or Actuator: The handle attaches to the stem on manually operated valves, enabling the user to turn the valve on or off. In automated valves, an actuator—pneumatic, hydraulic, or electric—replaces the handle, allowing for remote and precise control in industrial applications.
- Bonnet: The bonnet is a secondary enclosure, often used to secure the stem and other internal parts. It helps protect the valve’s internal components from external factors and contributes to the valve’s structural integrity.
Key Characteristics
Ball valves are well-regarded for their straightforward operation and minimal wear on internal parts. Their tight sealing and robust construction make them ideal for both industrial and residential applications. They can handle high pressures and temperatures with ease, while requiring minimal maintenance due to the simplicity of their design. This makes ball valves highly reliable, especially for applications where frequent shut-off and quick flow control are necessary.
Types of Ball Valves
Based on Design
Several design variations cater to specific needs:
- Full Port: These have a ball with a hole equal to the pipe diameter, allowing unrestricted flow and ideal for high flow rate applications.
- Reduced Port: Also known as standard port, these feature a smaller opening that slightly restricts flow, often chosen for cost-efficiency.
- V-Port: With a “V”-shaped ball, these allow for more controlled flow rates, making them useful for applications requiring gradual adjustments rather than a simple on/off function.
Based on Body Style
- Single-Piece Ball Valves: Made as a single unit, these valves are economical and simple to use but cannot be disassembled for repair or cleaning.
- Two-Piece Ball Valves: These are easier to maintain than single-piece models and can be disassembled for cleaning, making them popular in applications where cleanliness is essential.
- Three-Piece Ball Valves: These versatile valves are easy to repair and maintain without disconnecting the pipeline, making them ideal for industries that prioritize convenience and maintenance.
Based on Valve Actuation Method
- Manual Ball Valves: Operated by hand using a lever, these are suitable for simple applications where automation isn’t necessary.
- Automated Ball Valves: Actuated by pneumatic, hydraulic, or electric systems, these valves are preferred in industrial settings where remote control or automation is required.
Materials Used in Ball Valve Construction
Common Materials and Their Benefits
- Stainless Steel: Known for its corrosion resistance and strength, stainless steel is a preferred choice in industries handling corrosive chemicals and high temperatures.
- Brass: Cost-effective and resilient, brass ball valves are often found in plumbing and HVAC systems.
- PVC: Lightweight and corrosion-resistant, PVC ball valves are commonly used in low-pressure water applications.
Specialty Materials for Industry Needs
In certain industries, specialized materials are necessary to handle unique conditions:
- High-Temperature Alloys: These ball valves are designed to withstand extreme temperatures, making them suitable for power generation and other high-heat applications.
How Does a Ball Valve Work
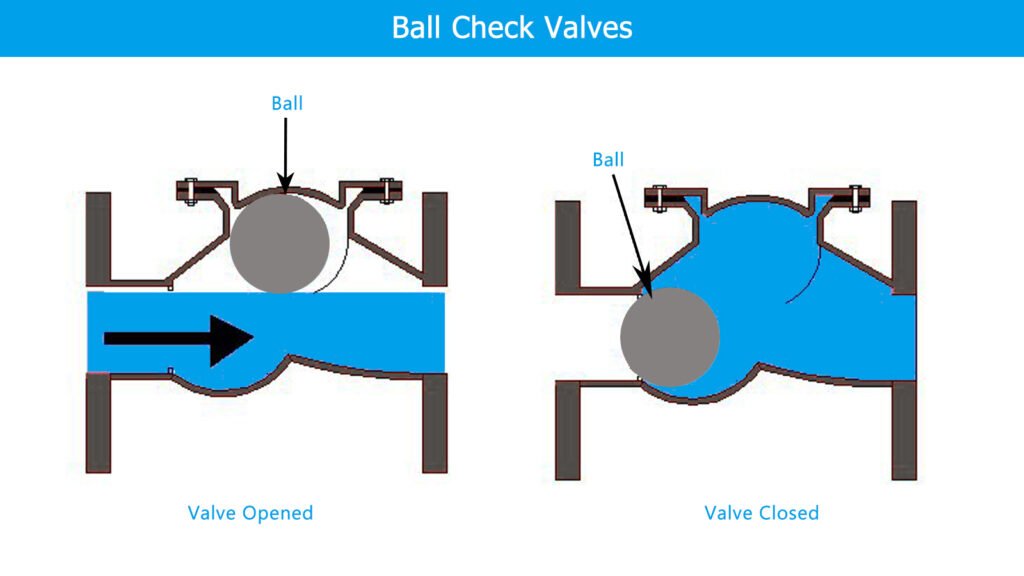
Basic Working Mechanism
The core mechanism of this valve is simple yet effective. When the handle is turned 90 degrees, the ball inside rotates, aligning its hole with the flow pathway to allow fluid to pass. Turning the handle back blocks the pathway and stops the flow. This straightforward operation makes it easy to control and highly reliable, ideal for on/off applications.
Different Flow Control Options
- Single Flow: Standard ball valves allow fluid to flow in one direction, ensuring controlled shut-off and flow.
- Double Flow: Some ball valves enable bidirectional flow, commonly used in systems where reverse flow is necessary.
- Multi-Port Flow: These ball valves, often with “T” or “L” shapes, allow fluid to be directed in multiple directions, useful in complex piping systems requiring different flow paths.
Advantages
Ball valves are widely chosen for industrial applications because of their unique advantages:
- Durability: The robust construction makes them highly resistant to wear and tear, capable of handling harsh environments and long periods of inactivity without losing performance.
- Cost-Efficiency: Ball valves are affordable to produce and require minimal maintenance, helping companies reduce operational costs.
- High-Pressure Tolerance: These valves are suitable for high-pressure applications, thanks to their tight sealing mechanism that prevents leaks.
- Minimal Maintenance: With fewer moving parts than other types, ball valves have a lower risk of mechanical failure and are easier to maintain.
Comparing Ball Valves with Other Valves
- Ball Valves vs. Gate Valves: While both are shut-off valves, ball valves provide quicker shut-off and are less prone to leaks, making them better for applications requiring a reliable seal.
- Ball Valves vs. Butterfly Valves: While butterfly valves are often preferred for larger pipe diameters, ball valves provide a tighter seal, making them ideal for applications where precise flow control and leak prevention are critical.
Applications
- Oil and Gas: Ball valves can withstand high-pressure environments, making them perfect for controlling the flow of oil, gas, and other petrochemical products.
- Water Treatment: Ball valves are frequently used in water treatment plants for their reliability and resistance to corrosion, ensuring smooth flow control.
- Pharmaceuticals: In the pharmaceutical industry, it helps maintain strict sanitary standards, as they can be easily cleaned and sterilized.
- Food Processing: Food-grade ball valves made from stainless steel are essential in controlling fluid flow in food and beverage processing without contamination risks.
Specific Use Cases
- High-Pressure Environments: Ball valves are suitable for pipelines requiring high-pressure handling, like those found in hydraulic and pneumatic systems.
- Corrosive Environments: Ball valves made from corrosion-resistant materials are ideal for handling chemicals in industries like mining and chemical processing.
- High-Temperature Environments: Specialty ball valves designed for high-temperature conditions are essential in industries such as power generation and steam distribution.
- Chemical-Resistant Materials: For handling aggressive chemicals, these materials provide protection against corrosive substances, enhancing the valve’s longevity and safety.
How to Select the Right Ball Valve for Your Needs
Key Factors to Consider
- Material Compatibility: Make sure the material (e.g., stainless steel, PVC) matches the type of fluid it will handle. For corrosive or high-temperature fluids, select a valve with materials designed to withstand those conditions.
- Pressure Ratings: Different ball valves have specific pressure tolerances. Always check the valve’s pressure rating to confirm it can handle the operational pressure of your system.
- Temperature Requirements: High-temperature applications demand specialty valves that can withstand extreme conditions. Choosing a valve outside of its temperature rating can compromise performance and safety.
Matching the Ball Valve to Industry Requirements
Each industry has its unique requirements, based on factors like fluid type, operational demands, and environmental conditions:
- Food and Beverage: Use stainless steel valves with sanitary connections to maintain cleanliness and prevent contamination.
- Pharmaceutical: Select valves with easy cleaning and sterilization capabilities to comply with strict hygiene standards.
- Oil and Gas: High-pressure and corrosion-resistant valves are essential for these industries, ensuring longevity and operational safety.
Installation and Maintenance Tips
Installation Best Practices
- Positioning: Install the valve in an accessible location where it can be easily operated and maintained.
- Tightening: Avoid over-tightening connections, as this can damage the valve seals. Use proper torque settings as per manufacturer recommendations.
- Testing: After installation, test the valve for any leaks or operational issues to confirm it’s functioning as expected.
Maintenance Tips
Regular maintenance can prevent unexpected failures and prolong the lifespan. Consider the following maintenance practices:
- Inspection: Periodically check for signs of wear, corrosion, or leaks. Early detection can prevent costly repairs or replacements.
- Lubrication: Lubricate the valve components as needed, especially in applications where the valve is frequently operated.
- Repair or Replace Worn Parts: Replace any damaged seals, seats, or other components to maintain a proper seal and prevent leaks.
Troubleshooting Common Issues
Identifying Potential Problems
They can experience common issues, such as leaks, corrosion, or operational stiffness, that may impair their function. Identifying these issues early can help in troubleshooting effectively:
- Leaks: Leaks are often caused by worn-out seals or improper installation. Inspect the valve and replace damaged seals as needed.
- Corrosion: Corrosion is common in valves exposed to harsh chemicals or moisture. Using corrosion-resistant materials can help prevent this issue.
- Operational Stiffness: If the valve becomes difficult to operate, it may be due to sediment build-up or lack of lubrication. Cleaning and lubricating the valve can help restore functionality.
Tips for Quick Troubleshooting and Repair
Here are some simple steps to troubleshoot and repair issues:
- Check for Loose Connections: Ensure all connections are properly tightened to prevent leaks.
- Clean the Valve Internally: Sediment or debris build-up can block the valve, so periodic cleaning is essential, especially in systems with unfiltered fluids.
- Replace Worn Parts: If seals or seats show wear, replace them promptly to prevent further issues.
Conclusion
Ball valves play a critical role across multiple industries, offering durability, reliability, and effective flow control. Whether for high-pressure environments, corrosive conditions, or residential plumbing, the versatility of ball valves makes them indispensable. Selecting the right one, maintaining it well, and understanding its operation can greatly enhance the efficiency and longevity of your systems. By choosing the right material, design, and actuation method, you can ensure that your ball valve meets your application’s needs and contributes to seamless operational performance.
FAQs
What are the main benefits of using ball valves over other types?
Ball valves are highly durable, offer a tight seal with minimal risk of leaks, and provide quick shut-off control. They are also easy to operate, require little maintenance, and are suitable for high-pressure and high-temperature applications, making them versatile for various industries.
Can ball valves handle high-pressure applications?
Yes, manufacturers often design ball valves to withstand high pressures, especially when made from materials like stainless steel or brass. Industries like oil and gas frequently use them, where handling high pressure is essential.
What is the best material for ball valves in corrosive environments?
In corrosive environments, people typically prefer stainless steel and other corrosion-resistant materials. For highly aggressive chemicals, they may also use special alloys or coatings to enhance the valve’s longevity and resistance to corrosion.
Are ball valves suitable for residential plumbing?
Ball valves serve as popular choices in residential plumbing for water shut-off because of their durability and easy operation. They are especially common in areas needing a reliable shut-off, such as water heaters, faucets, and main water supply lines.
How do I choose between manual and automated ball valves?
Manual ball valves suit straightforward, low-maintenance applications that don’t require automation. In contrast, automated ball valves work best in industrial environments where remote control or integration into automated systems is needed.