In hydraulic systems, ensuring the reliability and safety of fluid transfer is paramount, and this heavily depends on the quality of the connectors used. Stainless steel hydraulic fittings are critical for maintaining the integrity of hydraulic systems by providing secure, leak-free connections between hoses, tubes, and pipes. Renowned for their exceptional corrosion resistance, strength, and durability, these fittings are the preferred choice in industries where high pressure and harsh environmental conditions are common, such as marine, aerospace, and chemical processing applications.
What Are Stainless Steel Hydraulic Fittings?
Stainless steel hydraulic fittings are specialized connectors designed to link different components of a hydraulic system, such as hoses, pipes, and tubes. They ensure the efficient transfer of hydraulic fluids, maintain system integrity, and prevent leaks. Moreover, the unique properties of stainless steel, including its resistance to corrosion and its ability to withstand high pressures and extreme temperatures, make these fittings indispensable. Consequently, they are essential in critical industries such as oil and gas, food processing, and marine engineering.
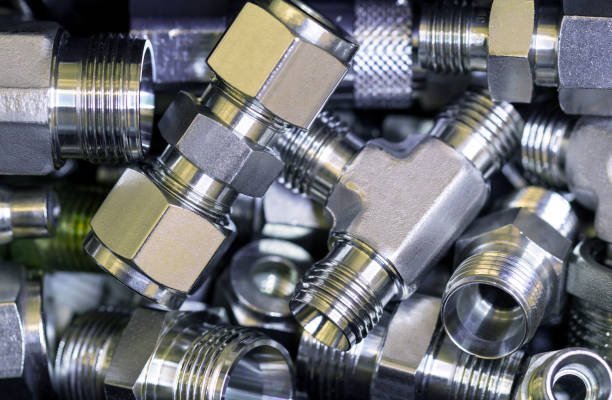
Types of Stainless Steel Hydraulic Fittings
Stainless steel hydraulic fittings come in various types, each designed to meet specific system requirements:
1. Compression Fittings
Compression fittings connect tubes by compressing a ferrule onto the tubing, creating a secure seal. Ideal for high-pressure applications, they are easy to install and remove.
2. Crimp Fittings
Crimp fittings are used with hydraulic hoses and require a crimping tool to secure the fitting to the hose. They provide a leak-proof connection, commonly used in mobile and industrial hydraulic systems.
3. Flare Fittings
Flare fittings work with tubing that has been flared at the ends. When the fitting is tightened against the flared tubing, it creates a strong, leak-free connection. Additionally, these fittings are commonly used in systems that are subject to vibration, which further highlights their reliability in demanding conditions.
4. O-Ring Face Seal (ORFS) Fittings
ORFS fittings are designed for high-pressure systems, featuring an O-ring in the fitting face that compresses against a flat surface on the mating part to create a seal.
5. JIC Fittings
Joint Industry Council (JIC) fittings are 37-degree flare fittings known for their reliability and ease of assembly and disassembly, commonly used in hydraulic applications.
Advantages of Stainless Steel in Hydraulic Fittings
Stainless steel offers numerous advantages when used in hydraulic fittings, making it the material of choice for demanding applications:
1. Corrosion Resistance
Stainless steel resists rust and corrosion, essential for applications in harsh environments, ensuring long-lasting performance.
2. High Strength
The material’s strength makes it suitable for high-pressure applications where durability is paramount.
3. Temperature Tolerance
Stainless steel maintains its properties across a wide temperature range, making it ideal for systems operating in extreme heat or cold.
4. Longevity
The long lifespan of stainless steel fittings reduces the need for frequent replacements, lowering maintenance costs.
5. Hygiene
Stainless steel’s non-porous surface is easy to clean, making it ideal for food processing and pharmaceutical applications.
Corrosion Resistance in Stainless Steel Hydraulic Fittings
One of the most significant advantages of stainless steel hydraulic fittings is their corrosion resistance. This characteristic is particularly crucial in industries where fittings encounter corrosive substances. For example, saltwater in marine applications and aggressive chemicals in industrial settings both pose significant challenges. Therefore, stainless steel, especially grades like 316, is preferred because it contains molybdenum. Consequently, this addition enhances its resistance to chloride corrosion. This makes these fittings ideal for environments where other materials would quickly degrade, ensuring system reliability and longevity.
How Much Pressure Can Stainless Steel Fittings Hold?
Stainless steel fittings are designed to handle high-pressure environments. The exact pressure rating depends on the specific type of fitting and stainless steel grade used. Generally, stainless steel fittings can withstand pressures ranging from several thousand to tens of thousands of psi, making them suitable for demanding applications.
Temperature Tolerance in Stainless Steel Hydraulic Fittings
Temperature fluctuations can significantly impact the performance of hydraulic systems. Stainless steel hydraulic fittings are highly resistant to both extreme heat and cold, making them suitable for a wide range of applications. Whether in the freezing conditions of the Arctic or the intense heat of industrial processes, stainless steel fittings maintain their structural integrity and performance, ensuring that hydraulic systems operate smoothly without the risk of failure due to thermal stress.
Stainless Steel Grades Used in Hydraulic Fittings
Different applications require specific grades of stainless steel, each offering unique properties:
1. 304 Stainless Steel
This grade is commonly used in less corrosive environments. It offers good corrosion resistance and is widely available, making it a cost-effective option for many applications.
2. 316 Stainless Steel
Known for its superior corrosion resistance due to the addition of molybdenum, 316 stainless steel is ideal for use in harsh environments, such as marine and chemical processing industries.
3. Specialized Grades
For specific applications, manufacturers may use other stainless steel grades like 303 for easy machining or 321, which is stabilized with titanium for better high-temperature resistance.
What Is the Difference Between 304 and 316 Stainless Steel Fittings?
- 304 Stainless Steel offers good corrosion resistance and is widely used in less corrosive environments. It is a cost-effective option for many applications but may not be suitable for very harsh conditions.
- 316 Stainless Steel on the other hand, is known for its superior corrosion resistance due to the addition of molybdenum. It is ideal for harsh environments, such as marine and chemical processing industries. It provides enhanced resistance to chloride corrosion compared to 304 stainless steel.
How Long Do Stainless Steel Fittings Last?
The lifespan of stainless steel fittings depends on several factors, including the operating environment, pressure levels, and maintenance practices. Generally, stainless steel fittings have a long lifespan due to their resistance to corrosion and high strength. With proper installation and maintenance, they can last for many years, reducing the need for frequent replacements.
Are Hydraulic Fittings Stainless Steel?
Although not all hydraulic fittings are made from stainless steel, many are because of the material’s superior properties. People prefer stainless steel for their strength, durability, and corrosion resistance. However, manufacturers also use other materials like brass or carbon steel for hydraulic fittings, depending on the application requirements.
Comparison with Other Materials for Hydraulic Fittings
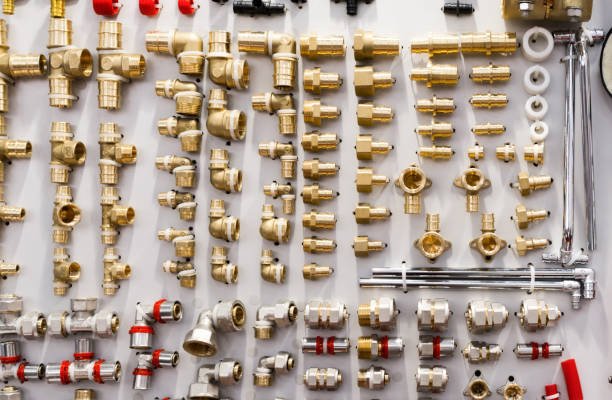
Stainless steel is often compared to other materials used in hydraulic fittings, such as brass and carbon steel:
1. Brass
While brass is easier to machine and cheaper than stainless steel, it lacks strength and corrosion resistance, making it unsuitable for high-pressure or corrosive environments.
2. Carbon Steel
Carbon steel fittings are strong and durable but are prone to corrosion, especially in harsh environments. They require protective coatings, which can wear off over time, reducing their lifespan.
3. Stainless Steel
Stainless steel offers a superior combination of strength, corrosion resistance, and temperature tolerance, making it the best choice for demanding applications.
Cost Considerations with Stainless Steel Hydraulic Fittings
It typically have a higher upfront cost compared to fittings made from other materials. However, their long-term benefits often justify the investment. The durability and corrosion resistance of stainless steel reduce the frequency of replacement and maintenance, leading to lower overall costs over the lifetime of the hydraulic system. Additionally, the reliability of stainless steel fittings in critical applications can prevent costly downtime and system failures, further enhancing their cost-effectiveness.
Custom Solutions and Manufacturing of Stainless Steel Hydraulic Fittings
In some applications, standard hydraulic fittings may not meet specific requirements, necessitating custom solutions. Many manufacturers, such as Taske, offer custom stainless steel hydraulic fittings tailored to the unique needs of a particular system. Designers craft these custom fittings to precise specifications, ensuring they are compatible with other system components and perform optimally under challenging conditions. Taske, known for its expertise in precision engineering, utilizes advanced manufacturing techniques, such as CNC machining and 3D printing, to produce these custom fittings with high precision and consistency.
Applications of Stainless Steel Hydraulic Fittings
The versatility and reliability of stainless steel hydraulic fittings make them suitable for a wide range of industries:
- Marine Industry: Essential for hydraulic systems exposed to corrosive saltwater environments, ensuring long-term durability and reliability.
- Aerospace Industry: In aerospace applications, where high pressure, temperature extremes, and vibration are common, stainless steel fittings provide the necessary strength and reliability.
- Oil and Gas Industry: The harsh conditions of the oil and gas industry demand fittings that can withstand extreme pressures and corrosive environments, making stainless steel the material of choice.
- Food Processing Industry: Stainless steel’s hygienic properties and resistance to corrosion make it ideal for use in food processing, where cleanliness and contamination prevention are paramount.
- Chemical Processing Industry: The chemical resistance of stainless steel fittings makes them suitable for use in systems that handle aggressive chemicals and corrosive fluids.
Installation and Maintenance of Stainless Steel Hydraulic Fittings
Proper installation and maintenance are crucial for the performance and longevity of stainless steel hydraulic fittings:
- Correct Torque: Apply the proper torque during installation to avoid damaging the fitting or mating components, ensuring a secure and leak-free connection.
- Use of Sealants: Depending on the fitting type, appropriate thread sealants or O-rings should be used to prevent leaks, ensuring long-term system integrity.
- Regular Inspection: Regularly inspect fittings for signs of wear, corrosion, or damage. Early detection and replacement can prevent system failures and costly downtime.
- Avoiding Cross-Threading: Careful installation is necessary to avoid cross-threading, which can damage the fittings and lead to leaks.
Choosing the Right Stainless Steel Hydraulic Fittings
Selecting the appropriate stainless steel hydraulic fittings for your application involves considering several factors:
- Pressure Requirements: Ensure the fittings can handle the maximum pressure of your hydraulic system. Stainless steel fittings are available in various pressure ratings, so choose accordingly.
- Temperature Range: Consider the operating temperature of your system. Stainless steel fittings can handle extreme temperatures, but it’s essential to choose a fitting rated for your specific application.
- Chemical Compatibility: If chemicals are present in your hydraulic system, ensure that the stainless steel grade of the fittings matches those chemicals to prevent corrosion.
- Size and Configuration: The size and configuration of the fittings must match the other components in your hydraulic system. Proper sizing ensures a leak-free connection and optimal system performance.
- Industry Standards: Make sure the fittings comply with industry standards relevant to your application. This is particularly important in regulated industries such as aerospace and food processing.
Conclusion
Stainless steel hydraulic fittings are essential components for reliable and durable hydraulic systems, especially in industries where corrosion resistance, high strength, and temperature tolerance are critical. These fittings offer numerous advantages, from superior corrosion resistance to longevity, making them the preferred choice in demanding applications. By selecting the right type of stainless steel fitting and ensuring proper installation and maintenance, you can significantly enhance the performance and lifespan of your hydraulic system.
FAQs
What makes stainless steel hydraulic fittings superior to other materials?
Stainless steel hydraulic fittings offer superior corrosion resistance, high strength, and durability compared to fittings made from other materials like brass or carbon steel. They are especially suitable for high-pressure applications and harsh environments.
Can stainless steel hydraulic fittings be used with any hydraulic fluid?
Stainless steel hydraulic fittings are compatible with a wide range of hydraulic fluids, including synthetic, petroleum-based, and water-based fluids. However, it is essential to verify chemical compatibility, especially in systems exposed to aggressive fluids.
How do I choose the right stainless steel grade for hydraulic fittings?
The choice of stainless steel grade depends on the specific application and environmental conditions. For example, 316 stainless steel is preferred in marine and corrosive environments, while 304 stainless steel is suitable for less aggressive conditions.
Are stainless steel hydraulic fittings reusable?
For example, people prefer 316 stainless steel in marine and corrosive environments, while they use 304 stainless steel in less aggressive conditions. However, always inspect the fittings for signs of wear or damage before reusing them.
What are the common causes of leaks in stainless steel hydraulic fittings?
Leaks in stainless steel hydraulic fittings can result from improper installation, insufficient torque, damaged threads, or worn seals. Regular maintenance and correct installation practices can prevent most leaks.
How often should stainless steel hydraulic fittings be inspected?
The inspection frequency depends on the operating conditions and the criticality of the hydraulic system. Specifically, in high-pressure or corrosive environments, it is important to inspect the fittings more frequently. By doing so, you can ensure that they remain in good condition and continue to function effectively.