When working with fluid transfer systems, whether it’s in an automotive, plumbing, or HVAC setup, selecting the right type of flare fitting can make a huge difference in the safety, efficiency, and durability of your project. Two common types you’ll encounter are the 37-degree flare and the 45-degree flare fittings. But how do they differ, and when should you use one over the other? Let’s break it all down for you!
What Are Flare Fittings?
Flare fittings are a type of compression fitting commonly used to connect metal tubing to other components in fluid systems. They work by “flaring” the end of a tube, which is then secured against a male cone-shaped fitting, creating a strong, leak-resistant seal. This type of connection is often found in high-pressure environments like hydraulic systems, automotive fuel lines, refrigeration, and HVAC applications.
But why are flare fittings so popular? Let’s break it down by discussing their advantages.
Advantages of Flare Fittings
- Leak-Resistant
The primary advantage of flare fittings is their exceptional sealing capability. The flare creates a strong metal-to-metal seal, making it highly resistant to leaks. This is crucial in systems like fuel or hydraulic lines where even a minor leak can lead to dangerous situations. - Pressure-Handling
Flare fittings can handle a wide range of pressures, depending on the angle of the flare and the material of the tubing. Manufacturers commonly use 37-degree flare fittings in high-pressure hydraulic systems, while 45-degree flare fittings suit lower-pressure environments like HVAC systems. - Durability
Because they form a metal-to-metal seal, flare fittings are incredibly durable and resistant to wear and tear. They’re less prone to loosening over time, making them a long-lasting solution, even in harsh environments. - Reusability
Unlike soldered or welded joints, you can easily disassemble and reuse flare fittings, making them ideal for systems that may need future maintenance or modifications. Just loosen the nut, and you can re-flare or replace the connection without replacing the entire fitting. - Corrosion Resistance
When paired with the right materials (e.g., stainless steel, copper, or brass), flare fittings can offer excellent corrosion resistance, ensuring a longer life span in harsh environments, such as marine applications or refrigeration systems.
Detailed Overview of 37-Degree Flare Fittings
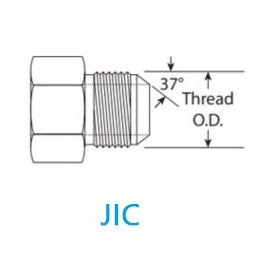
37-degree flare fittings, often referred to as JIC fittings, are a popular choice in industries that demand high pressure and reliable performance. These fittings follow SAE J514 and ISO 8434-2 standards, which make them widely recognized and trusted across industries like automotive, aerospace, and hydraulic systems.
Key Features:
- Narrow Flare Angle: The 37-degree angle allows for greater pressure resistance compared to wider flares, making them suitable for hydraulic systems that operate at extremely high pressures.
- Metal Types: Typically used with stainless steel, aluminum, or steel tubing, which are materials that can handle more stress without deforming. This combination of metal and flare angle helps the fitting create a solid and durable seal.
- Common Uses: You’ll frequently find 37-degree flare fittings in fuel systems, aerospace hydraulics, and marine applications where reliability under pressure is non-negotiable.
Advantages:
- Handles high-pressure applications: Perfect for use in hydraulic systems and high-performance fuel lines.
- Less prone to deforming: Due to the use of harder metals and the narrower flare, they are less likely to experience wear from repeated use.
- Widely used in critical industries: Their use in aerospace and automotive hydraulics speaks to their high reliability and durability.
Limitations:
- Higher Cost: Because of their specialized use and the materials involved (e.g., stainless steel or aluminum), they tend to be more expensive than 45-degree flare fittings.
- Not Ideal for Soft Metals: These fittings aren’t compatible with softer metals like copper or brass, limiting their versatility in lower-pressure systems.
Detailed Overview of 45-Degree Flare Fittings
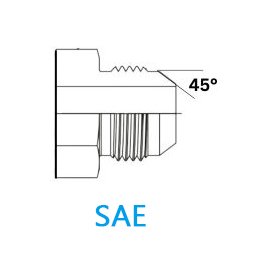
On the other hand, manufacturers widely use 45-degree flare fittings in lower-pressure applications, and these fittings follow the SAE J512 standard. They are the go-to fittings in plumbing, HVAC, refrigeration systems, and some automotive brake lines.
Key Features:
- Broader Flare Angle: The 45-degree flare provides a larger surface area for softer materials like copper and brass to seat against the fitting. This makes it ideal for low to moderate pressure applications where you don’t need the high stress tolerance that 37-degree fittings provide.
- Common Use with Copper: 45-degree flares are commonly paired with copper tubing, which is prevalent in plumbing, refrigeration, and HVAC systems.
- Standard Use in Refrigeration and HVAC: You’ll often see 45-degree flare fittings in systems like air conditioning units, refrigerators, and plumbing lines, where the pressures aren’t as intense, but a reliable seal is still necessary.
Advantages:
- More Affordable: 45-degree fittings are typically less expensive due to their widespread use in residential and commercial applications.
- Ease of Use: Because they are used with softer metals, installations are generally easier and less likely to require specialized tools or expertise.
- Readily Available: Since they are used in a broader range of applications, 45-degree flare fittings are easy to find in most hardware stores.
Limitations:
- Pressure Limitations: These fittings are not suitable for high-pressure environments. If used in systems with extreme pressure, there is a risk of leakage or deformation.
- Softer Materials: They are usually paired with softer materials like copper or brass, which may not hold up well in harsh conditions or over long periods in demanding environments.
Why Flaring Angles Matter: 37-Degree vs 45-Degree
While the difference in angle (37 degrees vs. 45 degrees) may seem small, it plays a critical role in performance. The 37-degree flare’s narrow angle allows it to handle higher pressures and work well with harder metals like steel and aluminum. In contrast, the broader 45-degree flare suits lower-pressure systems and softer metals like copper and brass better. Using the wrong angle in a specific application can lead to improper sealing, leaks, or even system failure.
A Quick Visual Breakdown:
- 37-Degree Flare: Narrower angle = High pressure, hard metals, industrial uses (aerospace, automotive, hydraulics).
- 45-Degree Flare: Wider angle = Lower pressure, softer metals, residential/commercial uses (HVAC, refrigeration, plumbing).
Key Differences Between 37-Degree Flare and 45-Degree Flare
Let’s dive straight into the key differences between the two types of fittings:
1. Flare Angle
- 37-Degree Flare: This type of flare has a 37-degree angle and is primarily used in high-pressure hydraulic applications. It’s common in industries like aerospace and automotive, especially in systems using stainless steel or aluminum tubing.
- 45-Degree Flare: The 45-degree flare, as the name suggests, has a 45-degree angle. It’s widely used in plumbing, refrigeration, and low-pressure applications like HVAC systems. It’s most compatible with copper and brass tubing.
2. Industry Standards
- 37-Degree Fittings: These are standardized under the SAE J514 specifications. They are often referred to as JIC (Joint Industry Council) fittings.
- 45-Degree Fittings: These follow SAE J512 and are commonly used for refrigeration and automotive brake lines.
3. Materials and Compatibility
- 37-Degree Fittings: Ideal for harder metals like stainless steel and aluminum, these fittings are designed to withstand the rigors of high-pressure systems. They are less likely to deform, which makes them more reliable in intense environments.
- 45-Degree Fittings: Typically used with softer metals such as copper and brass. The broader flare angle makes 45-degree fittings better suited for applications handling lower pressures.
4. Pressure Handling
- 37-Degree Fittings: Because of their narrower flare angle, 37-degree fittings are better at handling high-pressure environments. They are commonly seen in hydraulic and fuel systems where intense pressures are present.
- 45-Degree Fittings: These are more suited for lower-pressure systems. They work well in refrigeration systems, HVAC, and certain automotive uses, like brake lines, where extreme pressure isn’t a major factor.
Pros and Cons of 37-Degree Flare Fittings
Pros:
- High-pressure capability: Can withstand significantly higher pressures compared to the 45-degree flare.
- Durability: Perfect for rugged applications, especially with harder metals like steel and aluminum.
- Wide industrial use: Common in aerospace, automotive hydraulics, and other critical systems.
- Standardized: Follow SAE J514 and ISO 8434-2 standards, making them widely recognized and trusted globally.
Cons:
- Cost: Generally more expensive than 45-degree fittings due to their more specialized use and higher-pressure handling.
- Compatibility: Primarily compatible with steel or aluminum tubing, limiting its use with softer metals like copper.
Pros and Cons of 45-Degree Flare Fittings
Pros:
- Widespread use: Common in refrigeration, HVAC, and plumbing systems, making them easier to find and more affordable.
- Cost-effective: Cheaper than 37-degree flare fittings, especially when used with copper and brass.
- Simple installations: Easier to work with for less critical systems where extreme pressure isn’t a concern.
Cons:
- Pressure limitations: Not suitable for high-pressure environments, making them a poor choice for hydraulic or heavy-duty automotive applications.
- Deformation risk: More likely to deform if over-tightened or used in high-pressure situations.
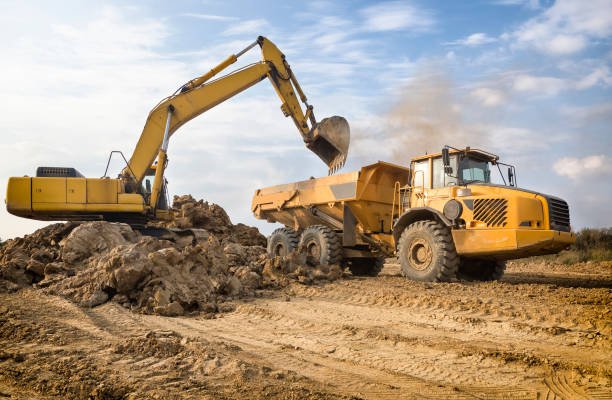
Applications of 37-Degree Flare Fittings
- Automotive Hydraulics: Engineers commonly use 37-degree fittings in aerospace hydraulic systems because they need reliability under extreme conditions.
- Aerospace: Engineers commonly use 37-degree fittings in aerospace hydraulic systems because they need reliability under extreme conditions.
- Marine Applications: Marine systems that require corrosion-resistant materials, like stainless steel, often utilize 37-degree flare fittings to ensure a leak-proof, high-pressure seal.
Applications of 45-Degree Flare Fittings
- Plumbing and HVAC: The 45-degree flare fitting is almost synonymous with copper tubing, especially in water systems, refrigeration, and HVAC lines. It’s perfect for low-pressure environments.
- Automotive Brake Lines: Mechanics still commonly use 45-degree flares in older vehicles or those with lower-pressure brake systems. They provide adequate sealing in systems where extreme pressures aren’t a concern.
- Refrigeration Systems: Manufacturers widely use 45-degree flares in air conditioning and refrigeration applications, often pairing them with copper tubing to create tight, low-pressure connections.
How to Choose Between 37-Degree and 45-Degree Flare Fittings
So, how do you decide which flare fitting is right for your project? Consider the following factors:
- Pressure Requirements: If your system operates under high pressure, such as in hydraulics or fuel injection, the 37-degree flare is the way to go. For low-pressure systems, like plumbing or HVAC, a 45-degree flare is sufficient.
- Tube Material: If you’re using stainless steel or aluminum tubing, the 37-degree flare is a better match. For copper or brass, the 45-degree flare fitting will serve you well.
- Industry Standards: Ensure you’re complying with the correct standards. For automotive hydraulics and aerospace, 37-degree (SAE J514) fittings are required. For HVAC and plumbing, the 45-degree (SAE J512) fittings are the go-to.
- Cost: If budget is a concern, and you’re working in a lower-pressure environment, 45-degree flares are generally more cost-effective.
- Future Maintenance: Consider the availability of fittings and parts for long-term maintenance. If you’re working in a specialized field (like aerospace), the 37-degree fitting might be harder to find locally and may require special ordering.
Conclusion
Choosing between 37-degree and 45-degree flare fittings isn’t just about preference; it’s about matching the right tool to the job. With the information shared above, you should now have a clearer understanding of which fitting is best for your project, ensuring optimal safety, performance, and cost-effectiveness. Whether you’re working on an automotive hydraulic system, a household plumbing job, or an HVAC setup, the right flare fitting will make all the difference.
FAQs
Can I interchange 37-degree and 45-degree fittings?
No, the two are not interchangeable. The different flare angles mean they won’t seat correctly, leading to potential leaks or fitting damage.
Which flare fitting is more durable?
While both are durable in their respective uses, the 37-degree flare fitting is generally more robust and better suited for high-pressure, high-stress environments.
Are there alternatives to flare fittings?
Yes, there are alternatives like compression fittings or push-to-connect fittings, but flare fittings offer a more reliable and secure seal in specific applications, especially those involving metal tubing.