Hydraulic hoses are vital components in a wide array of machinery, from construction and agriculture equipment to industrial automation systems. Despite their crucial role in ensuring fluid power transmission, these hoses are often overlooked—until they fail. A hydraulic hose failure can result in significant downtime, hazardous working conditions, costly repairs, and even life-threatening injuries. Recognizing early warning signs is not just a best practice—it’s a necessity.
This guide explores the most critical danger signals of hydraulic hose failure and provides practical advice for prevention, inspection, and emergency response. Whether you’re a maintenance technician, safety officer, or machine operator, this information is essential for keeping operations safe and efficient.
Understanding Hydraulic Hose Systems
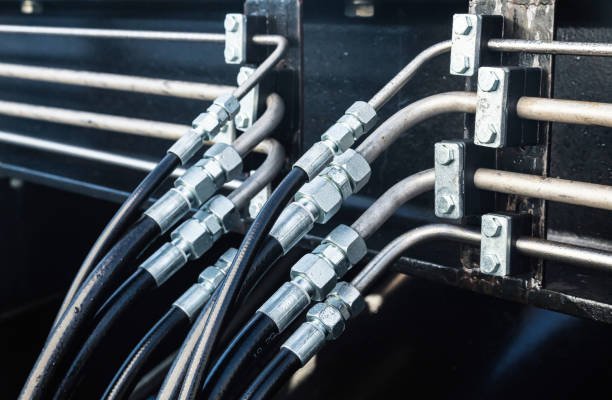
A hydraulic hose system consists of flexible hoses, fittings, adapters, and crimp connections that carry pressurized fluid to various parts of a machine. These hoses are engineered to withstand high pressures, extreme temperatures, and varying loads. Typically made from layers of synthetic rubber and braided steel wire, they are designed to offer both strength and flexibility.
The main purpose of a hydraulic hose is to transmit hydraulic fluid between components like pumps, valves, actuators, and motors. When functioning properly, these systems provide controlled force and motion. However, wear and tear, improper use, or environmental factors can significantly reduce their reliability, making it critical to monitor their condition regularly.
The Hidden Dangers of Hydraulic Hose Failures
Hydraulic hose failures are not merely inconveniences—they can pose severe safety and financial risks. One of the most dangerous outcomes is a high-pressure fluid injection injury, which occurs when hydraulic fluid punctures the skin, potentially leading to amputation or death if untreated. These injuries often look minor on the surface but can be medically catastrophic.
Beyond personal safety, a hose failure can halt production lines, damage expensive machinery, and cause environmental contamination through oil spills. Organizations may also face legal liabilities and fines if safety standards are not met. As such, understanding the danger signals and acting promptly can mitigate these risks effectively.
Common Causes of Hydraulic Hose Failures
Hydraulic hoses endure extreme operating conditions, making them susceptible to several types of failure. Understanding the common causes is key to preventing system breakdowns:
- Abrasion and Wear: Constant rubbing against surfaces or incorrect routing can wear down the hose cover, exposing the reinforcement layers underneath.
- Improper Installation: Poorly fitted hoses can lead to excessive bending, twisting, or kinking, all of which reduce service life.
- Temperature Extremes: Both high and low temperatures can degrade hose materials, causing brittleness, softening, or cracking.
- Hose Aging and UV Exposure: Over time, hoses naturally degrade due to environmental exposure, especially to UV rays in outdoor environments.
- Fluid Incompatibility: Using hydraulic fluid that isn’t compatible with the hose material can lead to chemical breakdown and leakage.
Addressing these factors through proper selection, installation, and maintenance is the first step in ensuring long-term hose reliability.
Top 10 Hydraulic Hose Danger Signals You Must Watch For
Being proactive starts with knowing what to look—and listen—for. These ten critical danger signals can indicate that a hydraulic hose is on the verge of failure:
- Bulging on the hose surface
- Continuous oil seepage at connections
- Abnormal hose vibration
- Oil temperature exceeding 80°C
- Pressure fluctuations exceeding ±15%
- Cracking or blistering on the hose surface
- Exposed wire reinforcement
- Whining or hissing noises from the hose
- Burnt smell or discoloration of fluid
- Stiff or brittle hose texture
Let’s explore each of these signals in detail, starting with one of the most visually obvious signs of trouble—bulging.
Danger Signal 1: Bulging on Hose Surface Indicates Imminent Wire Breakage
One of the most immediate red flags is a visible bulge on the surface of the hose. This abnormality often signals that the internal wire reinforcement has begun to break, compromising the hose’s structural integrity. When wire breakage occurs, the hose can no longer withstand normal operating pressure, putting it at risk of sudden and catastrophic failure.
“Internal pressure spikes, age-related material fatigue, or prior mechanical damage commonly cause bulging. If you detect any swelling or ballooning sections, remove the hose from service immediately and replace it with a certified equivalent.
Danger Signal 2: Continuous Oil Seepage at Connections (More Than 3 Drops/Minute)
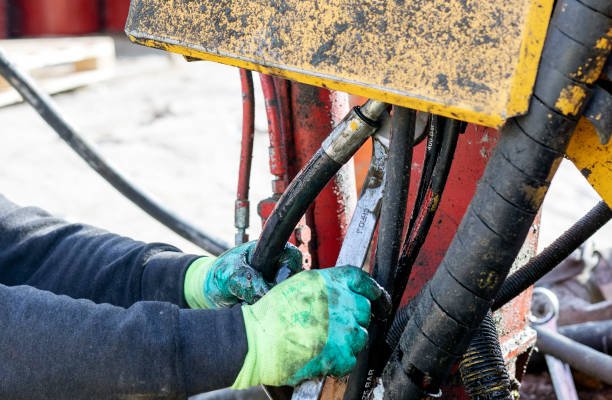
Frequent oil seepage at hose connections is more than just a nuisance—it’s a signal that your hydraulic system is leaking under pressure. When the rate exceeds three drops per minute, it often indicates a compromised fitting, degraded O-ring, or worn-out hose end. Over time, this can lead to significant pressure loss and contamination of the work environment.
Persistent seepage wastes expensive fluid, creates a slipping hazard, and increases the risk of fire. Inspect connection points regularly—especially after high-load operations—and replace seals or fittings as needed to keep the problem from escalating.
Danger Signal 3: Abnormal Hose Vibration (Frequency Over 2Hz)
Vibration in a hydraulic hose is normal to an extent, but if it exceeds 2Hz in frequency, it’s a warning sign of potential failure. Excessive vibration may result from incorrect hose routing, inadequate clamping, or internal fluid turbulence caused by pressure pulsations.
Over time, these vibrations can loosen fittings, cause fatigue cracks in the hose body, and eventually lead to hose rupture. Use vibration dampeners or supports where necessary, and make sure hoses are installed with enough slack to accommodate movement without strain.
Danger Signal 4: Sustained Oil Temperature Above 80°C Accelerates Hose Aging
Hydraulic fluid temperatures consistently exceeding 80°C (176°F) can significantly accelerate the aging process of hose materials. Prolonged exposure to high heat causes the rubber compounds to harden, crack, and lose elasticity, weakening the hose’s resistance to pressure and environmental stress.
High oil temperature can result from excessive load, clogged filters, or inefficient cooling systems. Monitoring fluid temperature with built-in sensors and implementing periodic system flushes can help maintain optimal thermal conditions and extend hose life.
Danger Signal 5: Pressure Fluctuations Exceeding ±15%, Indicating System Collapse
Hydraulic systems are designed to operate within a specified pressure range. If fluctuations exceed ±15% of the standard operating pressure, it’s a strong indication of internal instability—potentially caused by valve malfunctions, air entrapment, or a failing hose section.
These pressure swings not only reduce system efficiency but also place immense stress on hoses, fittings, and pumps. Continuous fluctuation may lead to hose ballooning, seal failures, and even full system collapse. It’s essential to use pressure gauges or digital monitors to track pressure consistency and address anomalies promptly.
Additional Visual and Sensory Clues
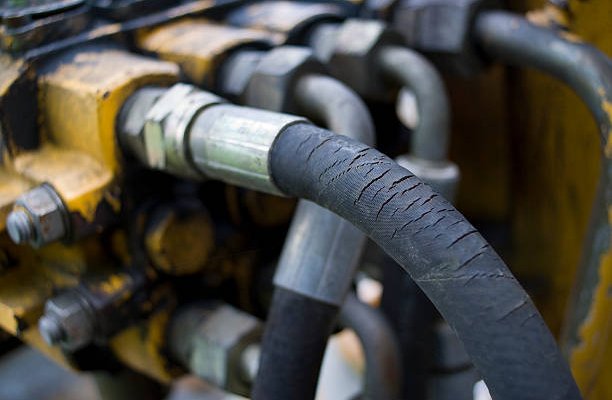
Aside from the major danger signals, subtle visual and sensory signs often precede hose failure:
- Cracking or blistering: Small cracks or surface bubbles suggest the inner tube or cover is deteriorating.
- Exposed wire reinforcement: Indicates the outer layer has worn through due to abrasion or UV exposure.
- Hissing or whining noises: These sounds can indicate fluid escaping from microcracks or a loose fitting.
- Burnt oil odor: Sign of overheating fluid or internal hose degradation.
- Stiff or brittle hose texture: Aged hoses lose flexibility and become prone to cracking under movement or pressure.
These signs should be treated as early warnings and addressed immediately to prevent full-blown hose failure.
Visual Inspection: Frequency and Techniques
Routine visual inspections are the frontline defense against hydraulic hose failures. Ideally, hoses should be inspected:
- Daily in high-duty or safety-critical applications
- Weekly in standard operational settings
- After any extreme weather conditions or heavy workloads
Use a consistent checklist to ensure nothing is overlooked. Look for external damage, improper routing, oil residues, fitting alignment, and hose integrity. Photos and logs can help document changes over time, aiding predictive maintenance efforts.
Incorporating inspection training for all operators ensures that warning signs are recognized early, long before a failure occurs.
Listen, Smell, and Feel: Sensory Detection Techniques
Human senses are powerful tools when it comes to identifying early hydraulic hose issues. Operators should be trained to trust their instincts and observe the following sensory cues:
- Listen: High-pitched whining, hissing, or pulsing sounds can suggest a pressure leak, loose fitting, or turbulent flow within a compromised hose.
- Smell: The scent of burnt oil or rubber often signals overheating or internal hose degradation. This should never be ignored as it typically precedes rupture.
- Feel: While always wearing gloves, gently pressing along the hose can reveal stiffness, brittleness, or soft spots that indicate internal damage or aging.
Encouraging a sensory-based inspection culture adds another critical layer of defense, especially in fast-paced environments where small changes are easily overlooked.
Emergency Self-Rescue Guide for Hose Burst Situations
In the event of a sudden hose rupture, quick thinking and safe actions can prevent further injury or equipment loss. Follow these steps immediately:
- Shut down the equipment: Turn off the engine or main hydraulic power source to stop fluid flow.
- Evacuate the area: High-pressure fluid can cause serious injuries. Clear nearby personnel quickly.
- Depressurize the system: Use the system’s designated relief method to reduce residual pressure safely.
- Contain the leak: Use absorbent materials or containment mats to prevent environmental contamination.
- Report and document: Notify the maintenance or safety team and document the failure for future analysis.
Always keep personal protective equipment (PPE) accessible and ensure all team members are trained for such emergencies. Remember, never touch a leaking hose with bare hands—fluid injection injuries are often invisible but extremely dangerous.
The Role of Preventive Maintenance and Predictive Monitoring
Preventive maintenance is one of the most effective strategies to avoid hydraulic hose failures. By replacing hoses based on usage intervals, operating conditions, and historical failure data, teams can proactively reduce risk. Typical maintenance tasks include:
- Regular inspection and replacement of worn or aged hoses
- Checking for loose fittings and tightening connections
- Cleaning hoses to remove debris and oil buildup
Predictive monitoring takes this a step further with technologies like pressure and temperature sensors, vibration monitors, and even AI-based analytics. These tools help detect hose degradation in real-time, enabling timely intervention before catastrophic failure occurs.
Core Safety Principles: Maintenance Guidelines and Best Practices
Adhering to core safety principles is vital to extending hose life and safeguarding personnel. Here are the best practices that should be included in every maintenance plan:
- Follow manufacturer specifications: Always use hoses that meet the recommended pressure, temperature, and fluid compatibility ratings.
- Maintain proper routing: Avoid sharp bends, kinks, and areas where hoses may rub against other surfaces. Use clamps and guides to support the hose path.
- Establish replacement intervals: Even if a hose appears functional, replace it based on the manufacturer’s recommended service life or when signs of aging appear.
- Store hoses properly: Keep spares in a cool, dry place away from direct sunlight, ozone sources, or chemicals that can accelerate degradation.
- Train your team: Ensure that machine operators and maintenance staff are trained to spot early warning signs and know emergency procedures.
Integrating these maintenance habits into daily operations minimizes the risk of hose failures and improves system longevity.
Choosing the Right Hose for the Job
Not all hydraulic hoses are created equal. Choosing the right one can dramatically impact system safety and performance. Factors to consider include:
- Working pressure rating: Ensure the hose can handle the maximum pressure of the system, including spikes and surges.
- Fluid compatibility: Match the hose material with the type of hydraulic fluid (mineral oil, synthetic, water-glycol, etc.).
- Temperature range: Consider both ambient and fluid temperatures the hose will be exposed to.
- Flexibility requirements: Use bend radius charts to ensure proper routing and avoid over-flexing.
- Brand reputation: Invest in high-quality hoses from trusted manufacturers known for performance and safety compliance.
Using the wrong hose not only voids warranties but also puts operators at serious risk. Always refer to technical data sheets and consult with hydraulic specialists when unsure.
When to Call the Professionals: Repair vs. Replacement
While some minor hydraulic repairs can be managed in-house, many situations require professional expertise. Here’s when to bring in a certified technician:
- Visible bulging, cracking, or oil spraying from the hose
- Signs of pressure instability or erratic system behavior
- Unknown compatibility between replacement parts and existing system
- Repeated failures at the same connection point
Professionals ensure hoses are cut, crimped, and installed to precise tolerances, minimizing the risk of premature failure. They also verify pressure ratings and fluid compatibility to maintain safety and compliance with industry standards.
Industry Standards and Workplace Regulations
Hydraulic hose maintenance and safety are governed by industry-specific standards and regulatory requirements that ensure consistent, safe practices across sectors:
- ISO Standards (e.g., ISO 18752, ISO 4413): These define performance classifications, system safety, and hydraulic component selection criteria.
- SAE Standards (e.g., SAE J517): Offer guidelines on hose construction, testing, and application.
- OSHA Regulations: Workplace safety mandates that include requirements for equipment maintenance, employee training, and emergency procedures.
Adhering to these standards not only improves operational safety but also ensures legal compliance. Ignoring them can lead to fines, equipment confiscation, or injury lawsuits—especially in regulated industries like manufacturing, aviation, and construction.
Conclusion
Hydraulic hose failures can be catastrophic—but they’re rarely without warning. By recognizing the key danger signals such as bulging, fluid seepage, excessive vibration, and abnormal temperatures, operators and maintenance teams can intervene before disaster strikes.
Implementing proper inspection techniques, following maintenance guidelines, and adhering to industry standards are all essential components of a safe and reliable hydraulic system. Ultimately, investing time and resources into monitoring and replacing hoses pays off in reduced downtime, safer workplaces, and longer equipment lifespan.
FAQs
1. What causes a hydraulic hose to suddenly burst?
Sudden hydraulic hose bursts are typically caused by internal pressure spikes, hose aging, material fatigue, or unnoticed bulging. Poor maintenance, improper hose routing, and using incompatible fluids can also contribute to unexpected failures.
2. How can I tell if my hydraulic hose is about to fail?
Warning signs include visible bulges, cracks, oil seepage at connections, abnormal vibration, and temperature over 80°C. Auditory cues like hissing and burnt fluid smells are also key indicators of impending hose failure.
3. How often should hydraulic hoses be inspected?
Hydraulic hoses should be visually inspected daily in high-use environments and at least weekly in standard operations. Additional inspections are recommended after heavy workloads, extreme temperatures, or visible warning signs.
4. Can I replace a hydraulic hose myself?
While minor replacements are possible for experienced personnel, it’s generally safer to have a certified technician handle hydraulic hose replacements. Incorrect installation can lead to system damage, personal injury, and compliance violations.
5. What is the typical lifespan of a hydraulic hose?
The average lifespan of a hydraulic hose is 1 to 5 years, depending on usage intensity, environmental exposure, fluid compatibility, and maintenance practices. Regular preventive maintenance can help maximize service life.